Chinese - Translation is available for Altium Designer 18.0:
Go to the page
Parent article: The Routing
Routing is the process of defining a connective path between the nodes in each net. This path is defined by placing PCB design objects, such as tracks, arcs, and vias, on the copper layers to create a continuous connection between the nodes. Rather than placing these objects one by one to build up the connective path, you interactively route the connection.
In the PCB editor, interactive routing is an intelligent process. After launching the command, click on a pad to select a connection to be routed. The interactive router then attempts to define a route path from that pad, all the way to the current cursor location.
The size of the track that is placed is controlled by the applicable Routing Width design rule, and the clearance from other net objects is controlled by the applicable electrical Clearance design rule. How the interactive router responds to existing objects, such as pads and routing on other nets, depends on the current Routing Conflict Resolution mode. The mode determines whether the router will Walkaround the obstacle, or attempt to Push it, or Stop, or Ignore it.
Interactive routing can be performed on:
- A single net - Route » Interactive Routing
- Two nets configured as a differential pair - Route » Interactive Differential Pair Routing
- A set of selected nets - Route » Interactive Multi-Routing
This article describes the process of interactively routing a single net, and the settings that control that process. If you are looking for information on specialized routing techniques, such as differential pair or controlled impedance routing, refer to the links on The Routing page.
Interactive Routing Tips
Below are some useful tips for interactive routing, a number of these are demonstrated in the video below:
- Run the Route » Interactive Routing command (Ctrl+W) then click on an object that has a net attribute to start routing. This can be a pad, a connection line, an existing via, a track end on a partially routed net, in fact, any object that belongs to the net.
- The PCB editor will jump to the nearest electrical object on that net, such as the center of a pad or the end of a track segment, then attempt to define a route path from there to the current cursor location.
- If you prefer working in a panel to using shortcuts, press Tab to pause routing and open the Interactive Routing mode of the Properties panel.
- The ability of the Interactive Router to reach the current cursor location depends on the current Routing Conflict Resolution mode, which is displayed on the Status bar and the Heads Up Display (Shift+H to toggle on/off) when the Interactive Routing command is running.

- Press Shift+R to cycle through the available conflict resolution modes. You can configure which modes are available on the Interactive Routing page of the Preferences dialog.
- If the mode is set to Walkaround, Push and Hug or Push, the Interactive Router will attempt to find a path around and between existing objects, as shown in the video below.
- Potential route path segments are displayed as hatched (placed on next click) or hollow (the look ahead segment; use this to work out where the previous segment should end).
- Click the mouse button to place all hatched segments.
- Press Spacebar to toggle the corner direction.
- Press Shift+Spacebar to cycle through the available corner modes (learn more).
- Press Backspace to "rip up" the last-placed segment(s).
- To switch to the next available signal layer and insert a via:
- Press the * key on the numeric keypad, or
- Use the Ctrl+Shift+Wheel Scroll shortcut combination.
- Press the 8 key to select a Via Type from those available (learn more).
- Press L when you click to start routing on a through-hole pad or via and realize you are on the wrong layer, each press will step to the next-available signal layer.
- Press / on the numeric keypad to insert a via and release that connection (use this for fanouts).
- Press 2 to insert a via and not switch layers (continue routing on the same layer).
- Ctrl+Click to instruct the interactive router to attempt to automatically complete the current route. If it does not auto-complete, it does not mean the connection cannot be routed. It could be that the distance is too far or it could be that the termination point is on another layer.
- Press Shift+F1 to display a list of in-command shortcuts.
Interactively routing a connection - after launching the command and clicking on a connection line, the Interactive Router finds a path from the net object to the current cursor location, weaving around existing objects.
A click of the mouse button will place all hatched track segments, Ctrl+Click to auto-complete the route.
Press Shift+F1 while routing to display a menu of available in-command shortcuts. You can select a command from the menu or use the shortcut keystrokes displayed next to each command.
Understanding Connectivity
An important part of becoming proficient with the interactive router is to understand how connectivity is managed in the PCB editor. When the design is transferred from the schematic (Design » Update PCB), the components are placed on the PCB workspace and the connection lines are displayed. The connection lines indicate which pads connect to each other in each net. They are a useful guide during component placement as you locate and orient each component.
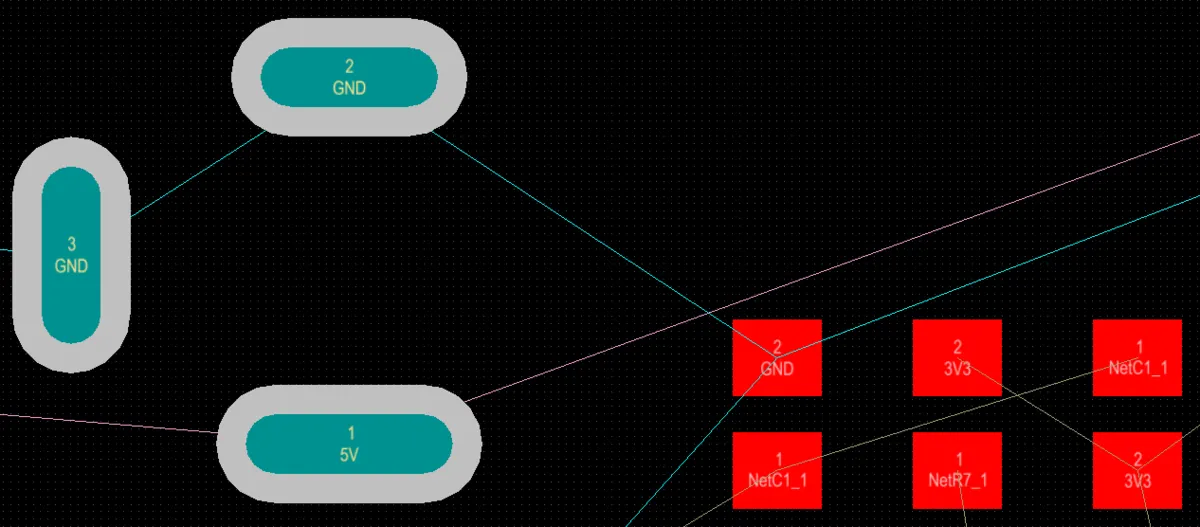
Connection lines are automatically created between each pad in the net in accordance with the applicable Routing Topology rule (the default is Shortest).
In this design, the GND and 5V nets use a different color for their connection lines.
Quick review of PCB connectivity
- The arrangement, or pattern, of the connection lines in a net is called the net topology. The topology is defined by the applicable Routing Topology design rule, with the default rule targeting All nets and applying a topology of Shortest.
- The PCB Editor includes a net analyzer that constantly monitors the location of all objects in the workspace and updates the connection lines when any net-type object is edited (including an object being moved). For example, when a component is moved, the far end of each connection from that component can jump from one target pad to another target pad, as they are updated to maintain the topology defined by the applicable design rule. An example of this is shown for the GND net in the video below; this net has a topology of shortest.
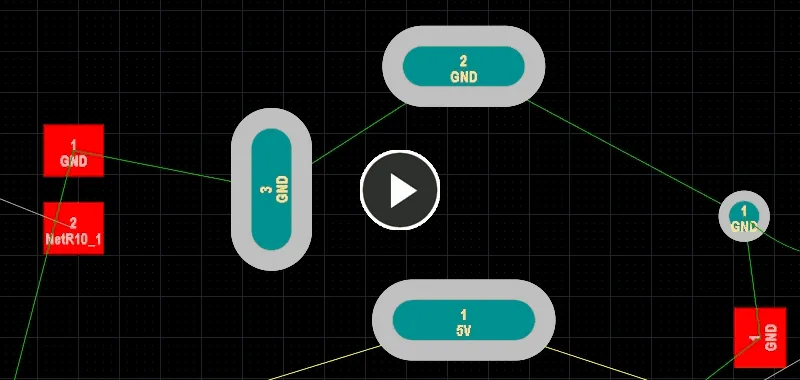
Note how the GND connection lines jump around as the resistor is moved, automatically being rearranged to keep the shortest overall connection length.
- The net analyzer monitors all the objects attached to a net, for example, when a connection is routed, the connection line between those two pads is automatically removed by the net analyzer. Or if a net is partially routed, then a shorter connection line will be displayed between the two closest route points on the net.
- It does not matter if you choose to ignore the connection line and route the net from/to a different location. As soon as routing is terminated, the net analyzer runs and removes the connection line if it is no longer required, as shown in the video below.
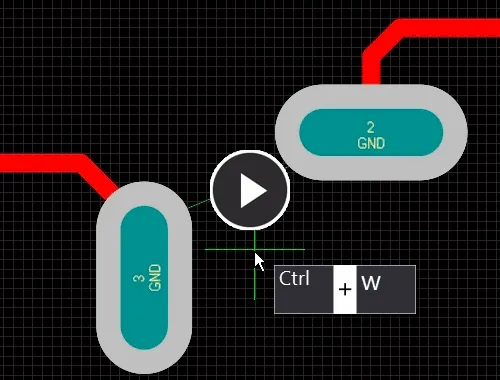
Even though the connection line connects the pad centers, you are free to route wherever you choose.
The net analyzer constantly monitors the routing progress and updates the connection line.
- Because the arrangement of connection lines is determined by the routing topology design rule, it is possible that the connection line will not attach to the end of the track and instead attach to some other point in the net that is closer to another point in the net. If preferred, connection lines can be forced to the track ends by enabling the Smart Track Ends option on the PCB Editing – General page of the Preferences dialog. The video below demonstrates this. Note that you can force the net analyzer to run and update the connection lines by performing an action that the software sees as you editing an object belonging to that net. Edit actions include: moving an object, clicking and holding on an object, or double-clicking to display that object's properties in the Properties panel.
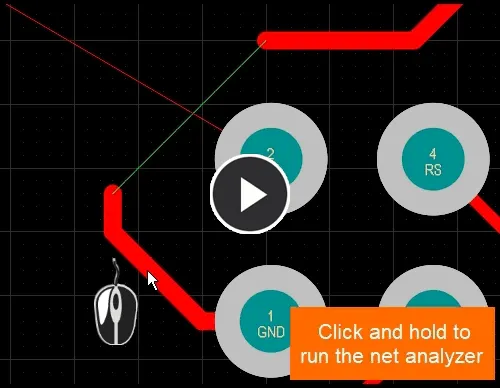
Note how the GND net connection line is attached to pad 1 instead of the end of the route. Once
Smart Track Ends has been enabled and an edit performed, the connection line jumps to the end of the route.
Finding a Net and Controlling the Color of the Connection Lines
- An un-routed board can appear intimidating - a mass of connection lines crisscrossing all over the board. A good approach to routing is to work from the schematic, where you can easily locate important components and critical nets. You can cross-select and cross-probe directly from the schematic components and nets, highlighting the equivalent item on the PCB. Learn more about Working Between the Schematic and the Board.
- You can also control the display of the connection lines by masking or hiding the nets in which you are not interested. Setting the color of important connection lines will also help you manage the routing process. Learn more about Finding a Net on the Board.
- Connection lines can also be hidden and selectively enabled via the View » Connections submenu.
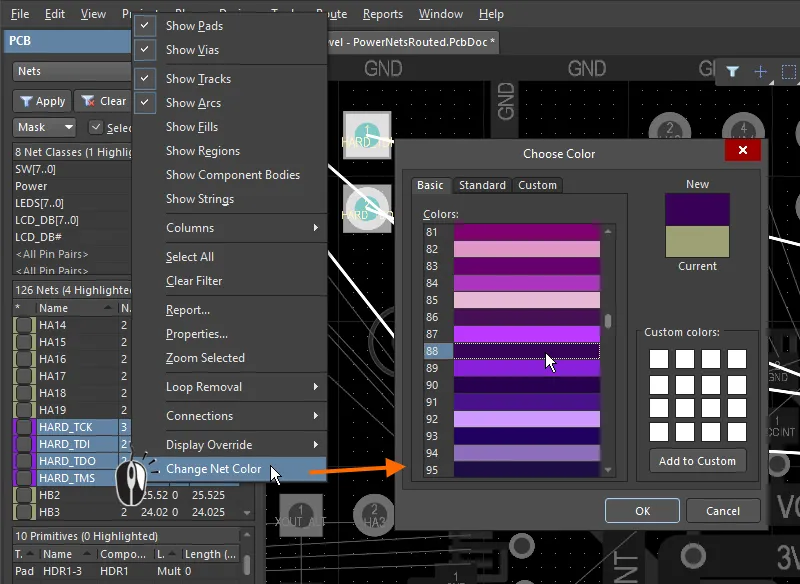
In the PCB panel, right-click on selected nets to change the color of their connection lines.
How the Routing is Located in the Workspace
The PCB editor is a grid-based editing environment, the default behavior is for your interactive routing to be placed on the current snap grid. As well as the snap grid, the software includes a number of additional snap features, designed to help you accurately position and align design objects. Together, these features are referred to as the Unified Cursor-Snap System.
The key elements of this system include:
- User-Definable Grids - available in both Cartesian and Polar formats.
- Object Snapping - enabling placed objects to pull the cursor into position, based on cursor proximity to that object's snap points (hotspots). Use this to pull the cursor to the center of an off-grid pad, for example.
- Snap Guides - that can be freely placed and provide a handy visual cue for object alignment.
- Axis Snapping - a feature to pull the cursor, in either the X or Y direction, so that it axially-aligns with a near-by object's hotspot.
Demonstration of the cursor-snap features.
► Learn more about the PCB Grids System
The Basics of Interactive Routing
When you launch the interactive routing command and click on a connection line, the interactive routing engine will add a chain of connected track segments from the nearest existing net object, such as a pad or existing track, along the shortest available path to the current cursor location.
Those track segments will be hatched, to show that they are proposed segments that have not yet been placed (uncommitted). When you left-click to place those segments they will become solid. These solid segments are actually referred to as soft commits - meaning the software recognizes them as segments you wish to retain, but the interactive routing engine may remove them or convert them back to uncommitted (hatched) if your routing path makes them redundant or creates an illegal shape. This behavior is demonstrated in the first video on this page.
Interactively routing a simple board.
When you click on a connection line to start routing the software will jump to the nearest existing net-object. To change which object on that net that has been chosen:
- Press 9 to switch to the net-object at the other end of the connection line.
- Press 7 to switch to another connection line leaving the same net-object, when there are two or more connection lines attached.
- Press Shift+F1 for a list of in-command shortcuts.
Configuring the Interactive Router
The default settings for interactive routing are configured in the PCB Editor - Interactive Routing page of the Preferences dialog, as shown below (click
to open). Many of the settings can also be changed during interactive routing, in the Interactive Routing mode of the Properties panel. Press Tab during routing to display the panel.
Configure the default interactive router settings in the Preferences dialog, then use the Properties panel to change settings as you route.
► The Interactive Routing options are described with the Interactive Sliding options, in the Interactive Routing and Interactive Sliding Options section.
The Properties panel automatically displays the properties of the currently selected object, or during routing, the currently selected command. Press Tab during routing to display and access the panel, after changing a setting click the Pause icon displayed on the screen (
) to return to routing.
Controlling the Corner Style
During interactive routing, the shape formed by the tracks and arcs that create a corner is referred to as the corner style. Diagonal corners are the most common, but curved corners (created by placing arcs), are also popular.
- Press Shift+Spacebar during routing to cycle through the corner styles, the current style is displayed on the Status bar (
) and in the Heads Up display.
- Press the Spacebar to toggle the corner direction.
- Alternatively, press Tab to open the Interactive Routing mode of the Properties panel and change the corner style there.
Corner Style |
Initial Corner Direction |
Alternate Corner Direction |
Notes |
Track 45 |
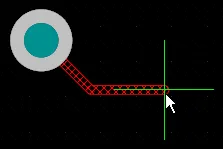 |
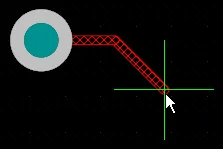 |
|
Line 45/90 With Arc |
 |
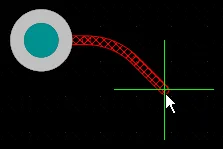 |
Use the & keys to interactively change the arc radius, hold shift to accelerate the radius change. |
Track 90 |
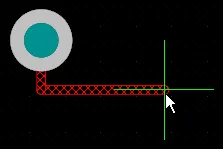 |
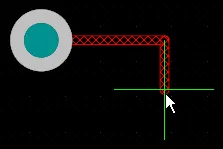 |
|
Line 90/90 Vertical Start With Arc |
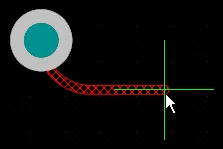 |
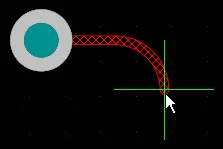 |
Use the & keys to interactively change the arc radius, hold shift to accelerate the radius change. |
Any Angle |
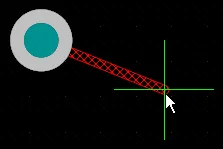 |
|
Use this mode in conjunction with Strong Glossing to perform snake routing. |
Miter or Curve the Corners
Corners can be defined using short, straight track segments, or they can be created using one or more arcs. The images below show the three most popular corner styles; Track 45, Line 45/90 With Arc and Any Angle.
Examples of three of the corner styles, Track 45, Line 45/90 With Arc and Any Angle, click to enlarge an image.
Note how in the first two images the interactive router is maintaining an overall orthogonal/diagonal pattern for the flow of the routing. In the Any Angle style the interactive router is finding the shortest path between the start location and the cursor location - this style of routing is called Snake Routing.
Mitered Corners
The most common routing corner shape is 45 degree mitered (diagonal) corners. Switch to the Track 45 corner mode to route diagonal corners. To ensure that it is not possible to inadvertently create acute corners during routing, both interactive routing and interactive sliding include a Miter Ratio option. The Miter Ratio multiplied by the current track width equals the separation between the walls of the tightest U-shape that can be routed for that miter ratio, as shown below. Enter a positive value equal to or greater than zero. Set the Miter Ratio to zero to create a right-angle corner.
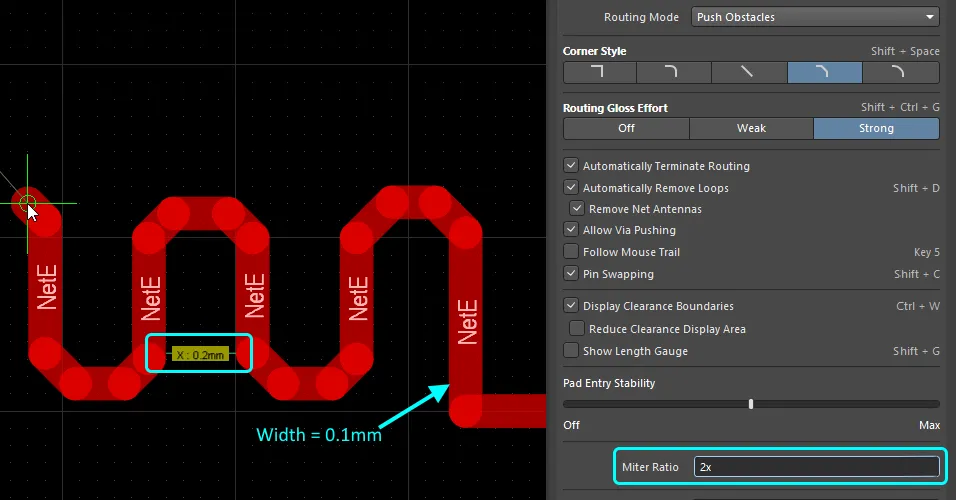
The current Miter Ratio value is used during interactive routing, interactive sliding, glossing and retracing. The default Miter Ratio is configured in the PCB Editor - Interactive Routing page of the Preferences dialog.
Arcs in Corners
Many designers require curved corners. Curved corners can be routed with either the Line 45/90 With Arc corner mode or the Line 90/90 With Arc corner mode. The Line 90/90 With Arc corner mode will force a 90-degree corner though, so use the Line 45/90 With Arc corner mode if the route needs to continue at 45 degrees. The arc can be interactively resized during routing using the
and
keys (hold Shift to accelerate the resizing process).
When a curved corner style is selected during interactive routing, the glossing engine will favor a tangential path around existing curved objects. That is, the arc placed to create the corner is located and radially sized to exactly curve around the existing object. This is designed to form smooth routing through a sea of curved shapes, for example the escape via pattern under a BGA. If the Routing Gloss Effort is set to Strong
it can result in the straight track segments between the arcs being placed at an angle other than horizontal or vertical.
If you require all of the straight track segments to placed exactly horizontal or vertical, with curved corners, it can be more efficient to route with diagonal corners and then gloss the routing to curve the corners. This is achieved by setting the Hugging Style set to Rounded
, and then running the Retrace Selected command. Retrace is used rather than the Gloss Selected because Retrace does not attempt to shorten the route path and reduce the number of corners, instead it focuses on glossing along the same path, in accordance with the current design rule settings. Alternatively, to use the Gloss Selected command set the Routing Gloss Effort to Weak
or Off
. Glossing is discussed below.
Curving the corners of existing routing.
Snake Routing
A style of flowing, point-to-point routing can be achieved by setting the corner style to Any Angle and the Routing Gloss Effort to Strong
. This creates what is referred to as Snake Routing. Use this when the routing requires any angle routes to flow through multiple curved objects, as shown in the example video below.
Snake routing, with the corner style set to Any Angle.
Glossing - Smoothing the Routes
Whenever you move the cursor to define a new route path, all of the proposed routing is automatically glossed. Glossing will attempt to reduce the path length, and also improve the shape of corners and reduce their number, generally resulting in neater routing created from fewer segments.
Glossing is applied during: Interactive Routing, Interactive Sliding, and by running the Gloss Selected or Retrace Selected commands.
Glossing has three settings; Off, Weak and Strong. Use the Ctrl+Shift+G shortcut to cycle through the settings during interactive routing or interactive sliding, or press Tab to open the Properties panel and select the setting:
- Off - in this mode, glossing is essentially disabled. Note, however, that cleanup is still run after routing/dragging occurs to eliminate, for example, overlapping track segments. This mode is typically useful at the end stage of board layout when the ultimate level of fine-tuning is required (for example, when manually dragging tracks, cleaning pad entries, etc.).
- Weak - in this mode, a low level of glossing is applied, with the Interactive Router considering only those tracks directly connected to or in the area of the tracks that you are currently routing (or tracks/vias being dragged). This mode of glossing is typically useful for fine-tuning track layout or when dealing with critical routes.
- Strong - in this mode, a high level of glossing is applied with the Interactive Router looking for shortest paths, smoothing out tracks, etc. This mode of glossing is typically useful in the early stages of the layout process when the aim is to get a good amount of the board routed quickly. Note that when Strong glossing is combined with one of the arc in corner modes, it also allows any-angle traces. The assumption here is that since the designer is curving the corners they will be comfortable with non-orthogonal routing between corners.
Along with the current Gloss Effort setting, Glossing also obeys these settings:
- Corner Style
- Hugging Style (during Interactive Sliding and also when the Gloss Selected or Retrace Selected commands are run)
- Miter Ratio
- Min Arc Ratio
Using these options, Glossing controls how tightly a corner is created and how the curved shape is formed in the route around a curved obstacle.
Existing routing can be glossed by running the Route » Gloss Selected command. Use this to your advantage to perform design changes, such as converting mitered corners to arcs, by configuring the Corner Style before running the command.
► Learn more about Post Route Glossing and Retracing
Temporarily Inhibit Glossing - Glossing is a core feature for interactive routing and sliding, but there will be situations where it prevents you from achieving the route shape you desire. Glossing can be temporarily inhibited by holding the Ctrl+Shift shortcut keys, when they are released glossing will be re-enabled at the current level.
Modifying Existing Routes
One of the most common tasks in routing is to modify the existing routing. This can be done by clicking and holding on an existing segment, and sliding it to a new location. This feature, known as Interactive Sliding (because it maintains the orthogonal/diagonal patterns defined in the original routing), can call on the same set of routing technologies that are available during interactive routing.
It is important to configure the sliding options to suit the routing style you have used on the board. For example, if you have routed with diagonal corners then the hugging style should be set to 45 Degree or Mixed. If it is set to Rounded then the glossing engine will curve (add arcs into) each corner affected by the sliding action.
Interactive Sliding Panel
To provide better visibility and control of the sliding process, the Properties panel includes an Interactive Sliding mode - press Tab during sliding to access the options in the panel. The default settings are configured in the PCB Editor - Interactive Routing page of the Preferences dialog.
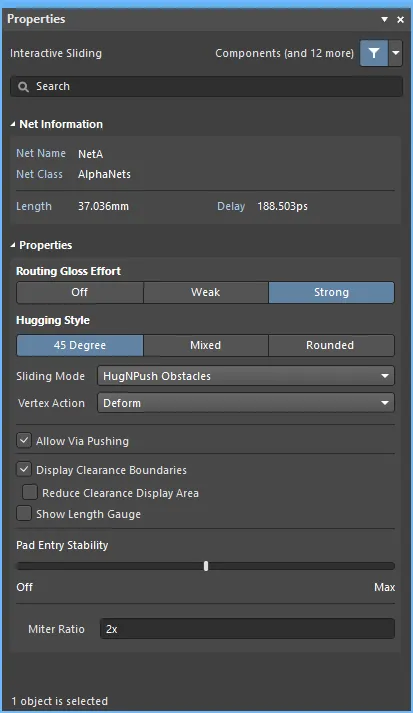
► The Interactive Sliding options are described with the Interactive Routing options, in the Interactive Routing and Interactive Sliding Options section.
Modifying the Routes
Examples of modifying the routing.
Tips for interactive sliding:
- Configure the Interactive Sliding options to suit the routing style used on the board - for example the Hugging Style should be
45 Degree
if your routing has diagonal corners. Press the Shift+Spacebar shortcut keys to cycle through the Hugging Style modes during sliding.
- To more easily see the objects that make up the current routing, adjust the Transparency of the routing objects in the View Configuration panel (
show image ).
- When you click and drag on a vertex the current Vertex Action setting is applied, use the
Deform
mode if you want to reshape the corner. Press the Spacebar to cycle through the modes as you drag the vertex.
- If you find that the routing will not slide how you want, try lowering the Routing Gloss Effort setting. Press the Ctrl+Shift+G shortcuts to cycle through the modes during sliding.
► The Interactive Sliding options are described with the Interactive Routing options, in the Interactive Routing and Interactive Sliding Options section.
Modifying T-Junctions
There are specific algorithms included to support interactively modifying a T-junction - click and drag on the junction point to modify a T-junction.

Examples of the T-Junction dragging capabilities.
Interactive Routing and Interactive Sliding Options
Whether you're interactively routing a connection or dragging an existing route to make way for more routing, the same set of routing technolgies are applied. This section summarizes the options available in the Interactive Routing and the Interactive Sliding modes of the Properties panel. The default settings for many of these options are configured in the PCB Editor - Interactive Routing page of the Preferences dialog.
Interactive Routing and Interactive Sliding Options
Routing Gloss Effort
During a route event, such as interactive routing, interactive sliding, or ActiveRouting, the software runs the glossing engine. The glossing engine constantly reviews all of the segments placed or impacted by the current route event, attempting to improve the quality of the results. Measures of quality include: reducing the number of corners, reducing the number of segments, removing acute angles and reducing the overall route length.
Glossing has three settings; Off, Weak and Strong. These settings are discussed in the Glossing - Smoothing the Routes section.
Hugging Style
This option controls how corner shapes are to be managed during interactive sliding and will affect both the tracks being slid and the tracks being pushed. During sliding use the Shift+Spacebar shortcut to cycle through the three modes.
- 45 Degree - always use straight orthogonal/diagonal segments to create corners during sliding (use this mode for traditional orthogonal/diagonal routing behavior).
- Mixed - use straight track segments when the objects being moved/pushed against are straight, use arcs when they are curved.
- Rounded - use arcs at each vertex involved in the move/push. Use this mode for snake routing, and to use arcs + any angle routes when glossing (during interactive routing and manual glossing).
Routing Mode / Sliding Mode
This option determines how you want the routing/sliding objects to react when they encounter an existing object. Use the Shift+R shortcut to cycle through the available modes during sliding.
These are the modes that are referred to as the Routing Conflict Resolution modes in the PCB Editor - Interactive Routing page of the Preferences dialog.
Vertex Action
To better support the designer's need to easily manipulate and re-shape the existing routing, there are specific options that are applied when you click and drag on a vertex rather than a track or arc (the vertex is the corner location where two segments meet). Use the Spacebar shortcut to cycle through the available modes during sliding.
- Deform - break or lengthen the track segments attached to the moving vertex so that the vertex follows the cursor movement.
- Scale - hold the corner shape and resize and move the incoming track segments, keeping the vertex attached to the cursor.
- Smooth - reshape the corner smoothly, inserting arcs to create a curved corner when dragging inward (in Mixed or Rounded Hugging Style), at every vertex impacted by the sliding process. Also add arcs when dragging outward in Rounded Hugging Style.
Checkbox Options
- Automatically Terminate Routing - when the current connection being routed reaches the target pad, automatically stop routing that net but remain in the Interactive Routing command, ready to start routing another net.
- Automatically Remove Loops - when this option is enabled you can route a new path for an existing route - when the new route path comes back to meet the existing path the redundant loop is automatically removed. Learn more about Modifying the Routing.
- Remove Net Antennas - a net antenna is a short, unterminated track (arc) segment. These are automatically removed if the current routing impacts on an object that the antenna is touching.
- Allow Via Pushing - during routing/sliding in Push or Hug & Push modes, allow existing vias to also be pushed.
- Display Clearance Boundaries - display the no-go area around existing objects, defined by the applicable Clearance design rule(s).
- Reduce Clearance Display Area - reduce this display to a circular zone around the current cursor location.
- Show Length Gauge - the length gauge indicates how well the current route is meeting applicable Length and Matched Length design rules. Learn more about Length Tuning.
Pad Entry Stability
The Pad Entry Stability slider protects centered pad entries, preventing Glossing from un-centering a centered track (it holds a centered track on-center, it does not center an un-centered track). Use the slider bar to configure the level of protection:
Off =
no protection
Max =
maximum protection
Miter Ratio
The Miter Ratio controls the minimum corner tightness. The Miter Ratio multiplied by the current track width equals the separation between walls of the tightest U-shape that can be routed for that ratio, as shown in the Mitered Corners description, earlier on this page. Enter a positive value equal to or greater than zero (the x multiplier is added automatically).
Min Arc Ratio
The Min Arc Ratio is applied during any angle interactive routing and also during interactive sliding with Mixed Hugging Style. The ratio is used to determine the minimum radius arc allowed, when the arc radius falls below this minimum the arc is replaced by track segments, where:
Min Arc Radius = Min Arc Ratio x Arc Width
- This setting is not applied during any arc in corner routing or interactive sliding with Rounded Hugging Style, as these modes do not use segmented arcs.
- Set the Minimum Arc Ratio to 0 (zero) to always use arcs.
Controlling the Routing Width and Via Size as You Route
When you run the Interactive Routing command and click to start routing, a series of track objects are created from the nearest pad up to the current cursor location. The width of these tracks is determined by the current Track Width Mode setting, which is displayed on the status bar during routing (shown in the video below).
There are four possible Routing Width Source settings:
- the designer's preferred width, referred to as User Choice (which must be within the range allowed by the applicable Routing Width design rule); or
- the Minimum, Preferred, or Maximum value of the applicable Routing Width design rule.
The selection of User Choice / Min rule / Preferred rule / Max rule is stored in and can be selected using
the Track Width Mode drop-down on the PCB Editor - Interactive Routing page of the Preferences dialog.
Changing the Track Width Mode While Routing
You can cycle through the four routing width options by pressing the 3 shortcut key during interactive routing, as shown in the video below. The current mode is displayed on the Status bar. If you forget any of the in-command shortcuts, press Shift+F1 to display a list while running the command.
To change the track width source while routing, press the 3 key on the keyboard. Press Shift+W to select a different value for the User Width.
When you change the track width mode, you move between the values defined in the applicable design rule (Min/Preferred/Max), and User Choice.
If you select User Choice, the track width will be:
- the width of existing routing if the
Pickup Track Width from Existing Routing option is enabled and the click location is on an existing route, or
- the last-used User-Choice width if it falls within the range defined by the applicable rule for the net you are routing. If it does not, the width will be clipped to the nearest value that is within the range allowed by the rule.
Changing the User Choice Routing Width While Routing
To change the width while routing, the following shortcuts are used. Note that if the Interactive Routing Width Sources options were set to one of the Rule-based width options, that option is changed to User Choice whenever one of these shortcuts is used.
- Shift+W - use this shortcut during routing to open the Choose Width dialog. Click on a new width to close the dialog and continue routing at the chosen width. Available widths can be edited by clicking the Favorite Interactive Routing Widths button on the PCB Editor - Interactive Routing page of the Preferences dialog.
- Tab - use this shortcut if the required width is not defined as a favorite. Pressing Tab will open the Properties panel in Interactive Routing mode. The current editing session will pause and the panel will open with the current Width selected. Type in a new width value then press Enter to continue routing at the new width. Alternatively, after typing in a new width value, click the pause button overlay to resume routing. To resume routing without editing the value, press Esc.
Remember, if you use one of these techniques to change the width during routing, the Track Width Mode is automatically changed to User Choice.
The routing track width must be between the minimum and maximum values specified in the applicable Routing Width design rule. If you attempt to change the width to a value that is outside the range defined by the rule's Minimum and Maximum settings, the software will automatically clip it back to within Min-Max range.
Changing Layers and adding a Via While Routing
There are two approaches to interactively change layers during routing:
- Press the * key on the numeric keypad. Each press of that key will move you down to the next available signal layer.
- Use the Ctrl+Shift+Wheel Scroll shortcut combination. Hold the Ctrl+Shift keys then scroll the mouse wheel forwards to move down through the available signal layers; scroll the mouse wheel backwards to move up through the available signal layers. Note that this shortcut can be used at any time to change layers. If you are not currently routing, this shortcut combination will step through all enabled layers.
A via is automatically added at the last corner where the last two segments meet. As with the routing width, the size of the via is determined by the current Via Size Mode as shown in the video below. The mode can be pre-configured in the
Interactive Routing Width Sources option.
Use the Ctrl+Shift+Scroll shortcut to change layers, and the 4 shortcut key to cycle through the via size choices.
Changing the Via Size Mode While Routing
As with the routing width, there are four possible options for selecting the via size during interactive routing:
- the designer's preferred via size (User Choice); or
- the Minimum, Preferred or Maximum value of the applicable Routing Via Style design rule.
You can cycle through the four via size options by pressing the 4 shortcut key during interactive routing. The current mode is displayed on the Status bar as shown in the video above.
Changing the User Choice Via Size While Routing
To change the User Choice via size while routing:
- Shift+V - press this shortcut during interactive routing to open the Choose Via Size dialog. The dialog will automatically list all via sizes currently used in the design. Select a via size then click OK to make that the User Choice via size.
- Tab - as well as changing the track width during routing, when you press Tab to
open the Properties panel in Interactive Routing mode you can also change the Via Diameter. As with the track width, the size you enter must be between the minimum and maximum values defined in the applicable Routing Via Style design rule.
Changing the Via Type While Routing
If there are multiple Via Types defined, during a layer change there may be more than one Via Type available for the layers being spanned. An example would be when there is a blind via available between the top and mid1 layers and there is also a top-bottom Via Type available. If you are performing a layer change and there is more than one Via Type available, you can press the 6 shortcut to cycle through the possible Via Type options (or press the 8 shortcut to display a list). Refer to the Defining the Via Types page for more detailed information. Additionally, the last-used via stack is retained as the default for the next net you route. The default via stack is retained for the current editing session only.
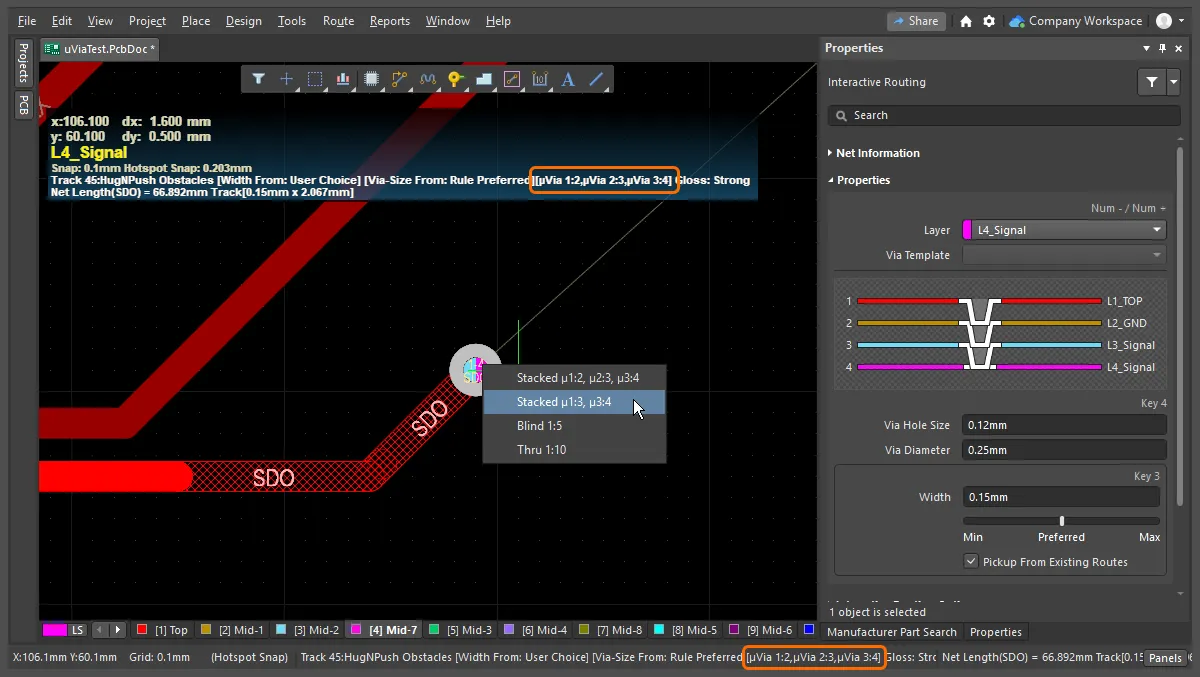
Stacked µVias being placed during a layer change from L1 to L4. The Interactive Routing mode of the Properties panel displays the Via Type(s) that will be placed. Press 6 to cycle through the possible via stacks; press 8 to display a list of possible via stacks.
Via Behavior when using the Look Ahead Routing Segment
During interactive routing the track segments that are yet to be placed are shown as hatched and the commited segments are solid. There is another mode, where the last segment connected to the cursor is displayed as hollow (an outline), this segment is referred to as the Look Ahead segment. When you are routing in Look Ahead mode all hatched segments are placed when you click, but the hollow segment is not. The idea is that you can use the Look ahead segment to accurately place the previous segment(s), without commiting the last segment. Press the 1 shortcut during routing to toggle the Look Ahead mode on and off.
If you toggle the Look Ahead mode on during a layer change the via will jump from the cursor back to the previous corner, because the Look Ahead segment will not be placed when you click. The video below demonstrates the behavior.
If you press 1 to toggle the Look Ahead mode on and off during a layer change, the via will jump back to the end of the last ready-to-place segment.
Controlling SMD Pad Entries
The SMD To Corner and SMD Entry design rules can impact the routing process. You will need to set up the necessary design rules before starting the routing process so that you can control how tracks enter and exit an SMD pad. Open the PCB Rules and Constraints Editor dialog (click Design » Rules from the main menus) to create and configure these design rules.
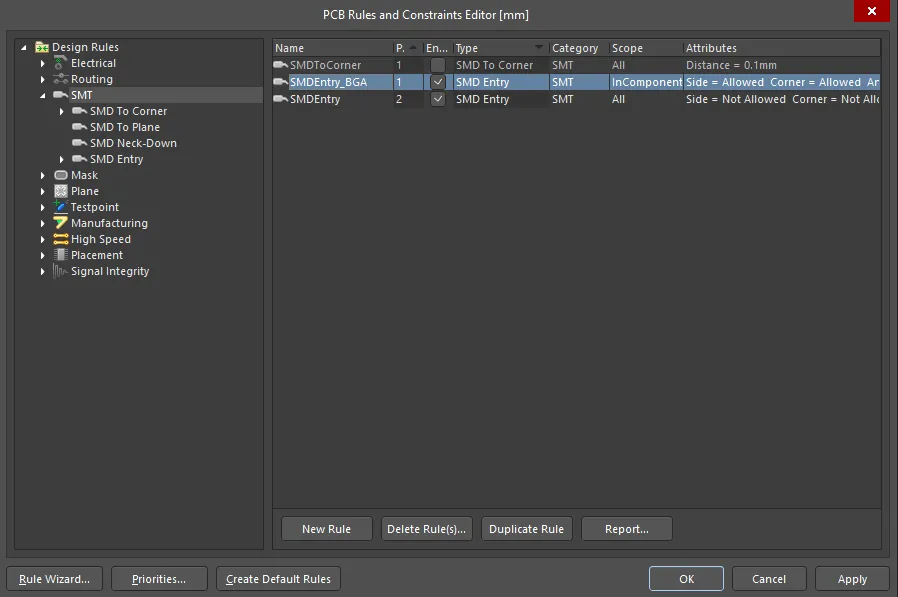
In the SMD to Corner design rule, the distance to corner value should be greater than the width of the track or the applicable clearance rule (whichever is greater). If it must be less than that, there are three ways you can approach this:
- Press the Spacebar while performing the pad entry. This can help align the last track segment along the pad center.
- Commit the routing close to the pad then perform the pad entry without glossing (glossing can be temporary disabled by holding down Ctrl+Shift).
- If performing the pad entry with more than one possible entry, move the mouse inside the pad. That allows you to choose where you want your SMD entry.
For the SMD Entry rule, the Side of the pad is the longer edge. The Side option in the design rule is only applied when the pad SideLength > 2 * EndLength
. This is done because most SMD discretes have almost-square pads, and for these devices it is often desirable to route into any edge of the pad.
Automatically Changing the Routing Width As You Route
A common challenge with modern component technology is needing to route a net at different widths as the routing travels across the board. For example, routing into or out of a BGA will often require narrower escape routes, switching to the preferred width at the edge of the BGA footprint.
This can be achieved manually during interactive routing using the techniques described previously on this page. You can also automate this width-switching behavior by adding a placement room and a room-based routing width rule. Once this has been done, tracks will automatically neck and expand as the room is entered or exited.
The feature works by:
- Defining a Placement Room rule for the region of the board that requires narrower routes.
- Defining a Width Constraint rule of a higher priority that defines the width of the routes within the room. This rule will use the TouchesRoom scope as discussed below.
Once this has been done, the width will change automatically as you route into or out of the placement room as shown in the videos below.
Width rules are obeyed and track segments are intelligently sized as the room boundary is crossed.
Room-based routing requires a placement room to be defined first. A placement room is also a design rule. While you can create the rule then define the room from the design rule dialog, it can be more efficient to do it the other way around, interactively create the room; Altium Designer creates the design rule for you.
Creating the Room Rule
The Design » Rooms submenu has a number of room definition commands.
Rooms are a useful feature for controlling where components are placed and also for controlling what rules are applied within that area of the board.
A room created around selected components will result in the following:
- A Component Class of the selected components is created. Review the class (Design » Classes) and update the Component Class Name as required.
- A Placement Room Definition design rule is created. The rule is scoped to target the Component Class created in step 1. If you changed the Component Class name, the rule scope (Full Query) must be updated to match.
- The Placement Room Definition design rule is also automatically named. Update the name as required and take note of the name because the room will be referenced in other design rules by its Name.
- If required, resize the room. To do this, click once to select it then click and hold on a vertex to move a corner or an edge. After clicking on a vertex to move it, you can also press Shift to perform a symmetrical resize.
In this example, the rule has been scoped to target a specific BGA footprint ('BGA50P18X18-180') rather than a component class.
A Placement Room Definition design rule is normally scoped to target one or more components. In this situation where it is ultimately being used to control the routing within the area defined by the room, you do not actually have to scope it to target specific components. For example, the scope of the rule (Full Query) could be set to All and the routing would still behave as required. The advantage of scoping it to target the component(s) within it is that if the component(s) needs to be moved, the Design » Rooms » Move Room command can be used to move the room and the components together.
Creating the Room-based Routing Rule
Once the room that defines the area requiring a different routing width has been defined, the routing width rule can then be created. The image below shows an example of a Routing Width rule that is scoped to instruct the PCB editor to set the routing width to 0.075mm whenever the routing touches the room named Room_BGA. Altium Designer's interactive routing engine will automatically terminate the current track segment and start a new segment at the room boundary to satisfy a rule such as this.
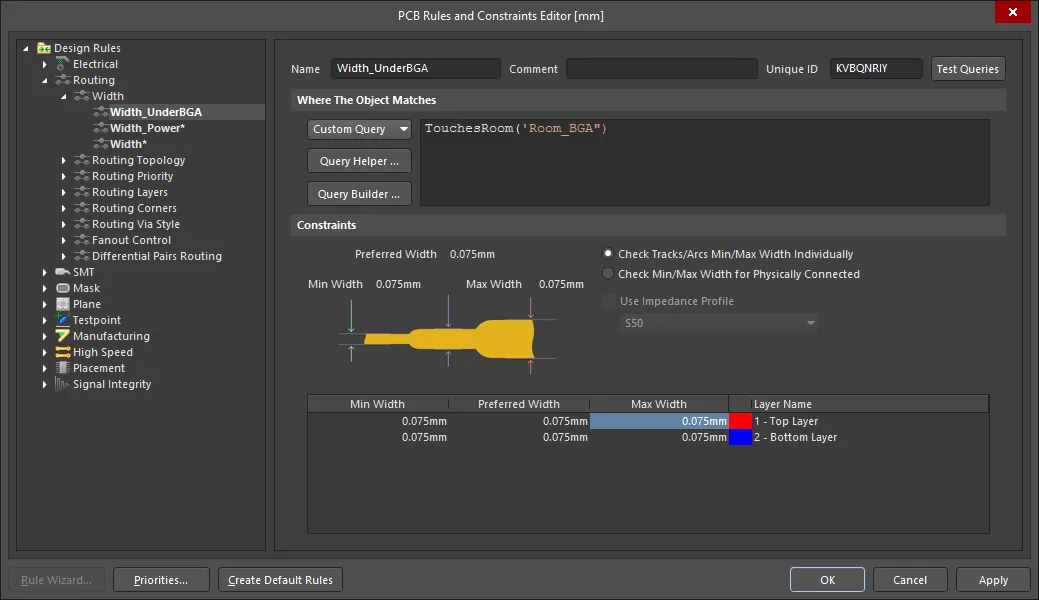
A Routing Width design rule scoped to set the width of all nets to 0.075mm within the room Room_BGA. Note that this rule appears first in the tree indicating that it is the highest priority routing width rule.
► Learn more about the TouchesRoom and WithinRoom query keywords
Connecting Two Nets with a Net Tie Component
It is not uncommon to need to intentionally connect two different nets. An example could be when you need to connect an Analog ground and a Digital ground in a controlled way. This is achieved by connecting the two nets through a Net Tie component. A Net Tie component is nothing more than a controlled short circuit, allowing you to decide the location on the board where the nets connect.
The challenge with routing towards a Net Tie pad is the rules engine will see that a violation is about to occur, and prevent you from routing to the Net Tie pad.
To resolve this, either:
- route out from the Net Tie pad, or
- switch the Routing Mode to
Ignore Obstacle
.
To route in to a Net Tie, switch the Routing Mode to Ignore Obstacle.
► Learn more about Intentionally Connecting Two Nets
Automatic Re-Routing of a Moved Component
Component Re-route
While routing the board, it is not uncommon to need to adjust the location of a routed component to create space for new routing. This feature is accessed by enabling the Component re-route checkbox in the Dragging region on the PCB Editor - Interactive Routing page of the Preferences dialog.

During the move process, the following shortcuts can be used to invoke the specified actions:
- Component Re-route Mode (Shift+R) - toggles post-drop connectivity restoration. After the moving set has been released, the software will attempt to re-route the component(s) to reconnect any broken nets. Use the Shift+R shortcut to inhibit the re-route behavior (or disable the Component re-route option on PCB Editor - Interactive Routing page of the Preferences dialog). Current Status is displayed in the Heads Up display and on the Status bar.
- Change Component Selection (Shift+Tab) - while dragging, the set of objects being moved can still be changed. Press Shift+Tab to cycle through the following selection sets:
- Components only, then
- Components +Via Fanouts +Escapes +Interconnects, then
- Initial selection set (if different from the previous two), then
- Back to Components only.
- Display / Hide Connection Lines (N) - the N shortcut cycles through three states: no connection lines, pad-to-pad connection lines, and route-to-route connection lines. The last mode indicates where the connection lines have been severed and will possibly be restored after the selection being moved is released.
- Change Gloss Effort (Ctrl+Shift+G) - cycle through the available Routing Gloss Effort options to control the amount of gloss applied during component re-routing.
Move Component with Relevant Routing
Enable the Move component with relevant routing option in the Dragging region on the PCB Editor - Interactive Routing page of the Preferences dialog to start the move component action with the relevant routing (Components +Via Fanouts +Escapes +Interconnects). Use the Shift+Tab shortcut to cycle the selection set as described in the above section.
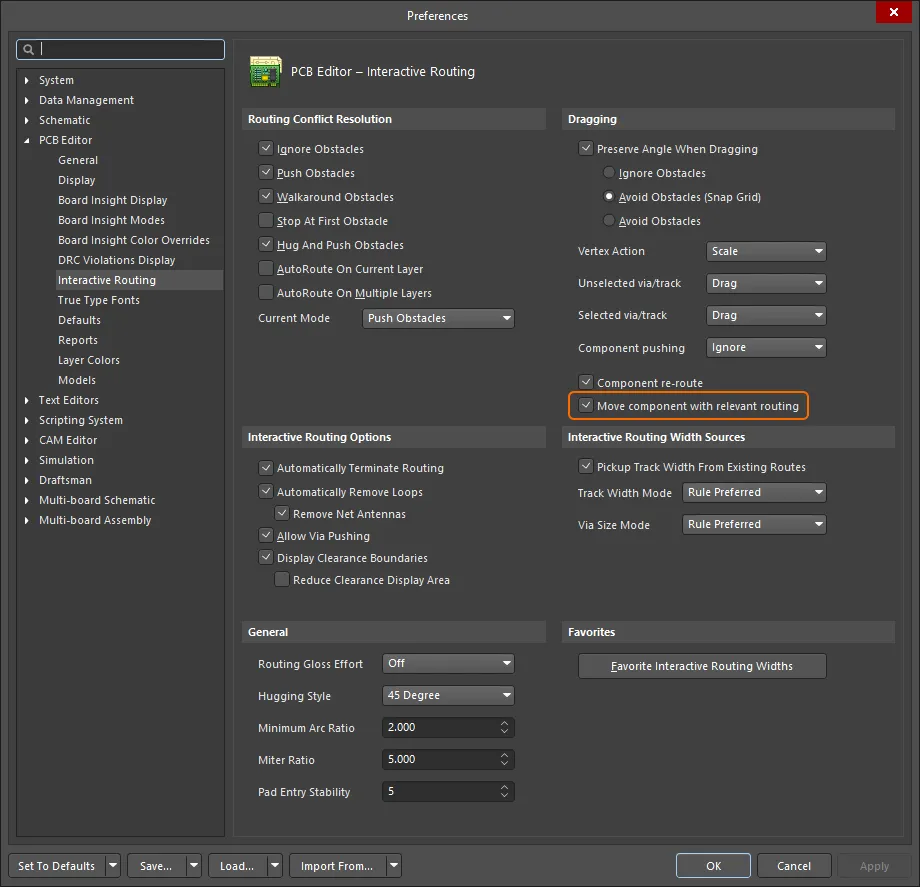
Disable the option to start the move component action with components only selected. Because the set of relevant routing objects is detected prior to the move commencing, it is not possible to use Shift+Tab to cycle through the selection set when the option is disabled.
To make the Move Component behavior routing-friendly, the software detects and fixes violations in both the moving routing and the pre-existing routing. The default handling of violations is to visualize them while moving and attempt to resolve them on drop. Violations are resolved by pushing the pre-existing routing. Violations that cannot be resolved are left.
Tracing an Existing Shape with the Interactive Router Follow Mode
A common requirement during routing is to place a route so that it follows an existing shape or contour. The contour could be an obstacle, a cutout or the board edge, or an existing route.
Rather than having to route "against" the contour using careful and accurate mouse movements and click actions to ensure the new route hugs the contour, in Follow mode, you click to nominate the contour then move the cursor along the contour to define the route direction. In Follow mode, the interactive router will add track and arc segments so that the new route follows the contour in compliance with applicable design rules. This feature is particularly useful when placing curved routes.
To use the feature:
- Launch interactive routing, click to pick a connection to route and switch to the required corner style (Shift+Spacebar).
- To follow a contour, position the cursor over the required object and press Shift+F. The Interactive Router will detect the object under the cursor and switch to Follow Mode.
- Move the cursor in the required direction; the software will automatically place track and arc segments to follow the contour in that direction.
- Left-click to place the Follow segments and drop out of Follow mode.
- Complete the route as required.
Available Routing Conflict Resolution Modes
As mentioned, how the interactive router responds to objects already in the PCB workspace, such as pads on other nets, depends on the current Routing Conflict Resolution mode. Configure which conflict resolution modes are available during routing on the PCB Editor - Interactive Routing page of the Preferences dialog.
Conflict resolution modes include:
- Ignore Obstacles – ignore existing objects (routing can be freely placed). Violations are highlighted.
- Push Obstacles – push existing tracks and vias to make room for the new route.
- Walkaround Obstacles – attempt to find a path around existing objects. The clearance to other objects is defined by the applicable Clearance design rule.
- Stop At First Obstacle – in this mode, the routing engine will stop at the first obstacle that gets in the way.
- Hug And Push Obstacles – in this mode, the routing engine will closely follow existing objects and only push them when there is insufficient room for the track being routed.
- AutoRoute on Current Layer – this mode applies auto-router intelligence to the interactive router, automatically selecting between pushing and walking around to give the shortest overall route length.
- AutoRoute on Multiple Layers – this mode applies auto-router intelligence to the interactive router, automatically selecting between pushing, walking around or switching layers to give the shortest overall route length.
The current Conflict Resolution mode is displayed on the Status bar at the bottom of Altium Designer. Use the Shift+R shortcut keys to cycle through the available modes during interactive routing.

Dynamic Display of Clearance Boundaries During Routing
Have you ever wondered why a route won't fit through a gap during interactive routing? Is it an incorrect rule constraint or is the net being targeted by the wrong rule? Designed to help interpret and understand the impact of design rules, the dynamic display of clearance boundaries feature shows just how much space is available during interactive routing.
The Display Clearance Boundaries feature has two modes: either display the clearance boundaries as a shaded, no-go area around all objects on the entire PCB; or reduce the clearance display area to a circular zone around the cursor.
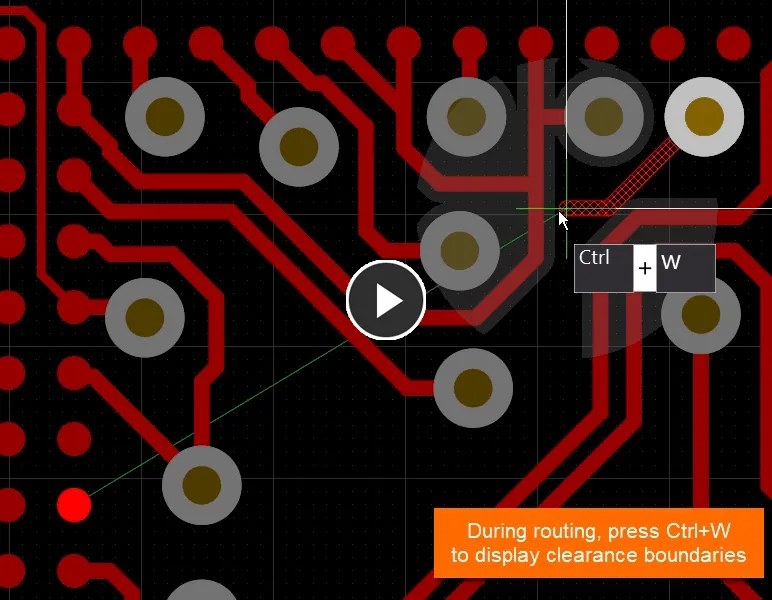
The clearance around existing workspace objects can be displayed dynamically as you route. Use the Ctrl+W shortcut to enable/disable during routing.
- The Ctrl+W shortcut is used to launch Interactive Routing, and can then be used again to toggle the Display Clearance Boundaries feature on or off during routing.
- Press Tab during interactive routing to open the Interactive Routing mode of the Properties panel, where all of the interactive routing options can be configured.
Enabling the Dynamic Display of Clearance Boundaries
Enable the Display Clearance Boundaries option on the PCB Editor - Interactive Routing page of the Preferences dialog.
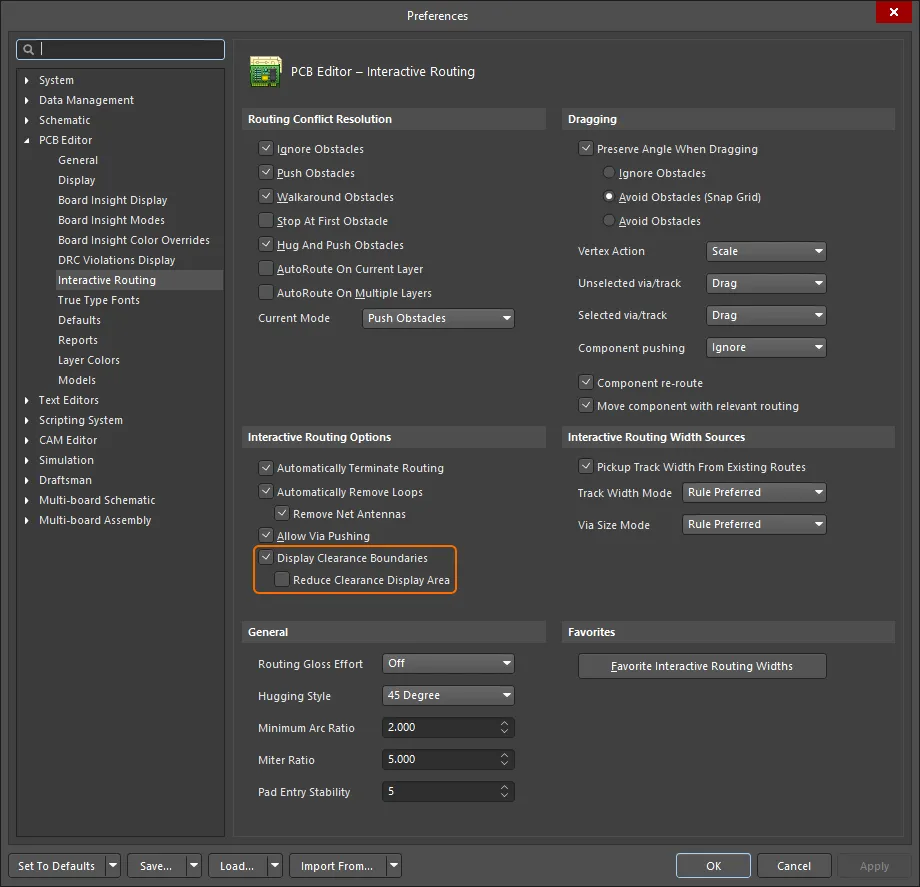
Enable the option on the PCB Editor - Interactive Routing page of the Preferences dialog.
- When the Display Clearance Boundaries option is enabled, the no-go clearance area defined by the existing objects + the applicable clearance rule is displayed as shaded polygons within a local viewing circle as as you interactively route.
- If the Reduce Clearance Display Area option is disabled, the no-go clearance area is displayed for the entire layer as shown in the video below.
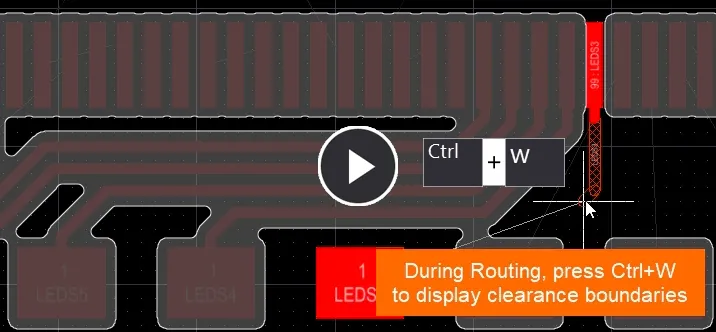
The no-go area can be displayed for all copper objects on the current layer, if preferred.
Clearance boundaries can also be displayed during Interactive Differential Pair Routing and Interactive Multi-Routing. The display of clearance boundaries is available in all routing modes except Ignore Obstacles.
Strategies for Selecting the Routing
Selection is a core activity in all areas of the design process, including working with existing routing. Whether you are about to gloss or you want to delete some routing, the routes need to be selected first.
Select Within or Select Touching
In the PCB editor, selection can either be objects that are Within the selection rectangle or Touching the selection rectangle. This is controlled by the direction you move the mouse as you draw the selection rectangle:
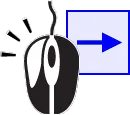 |
Select Within - click and drag a blue rectangle from left to right to select all visible, unlocked objects that are completely within the selection rectangle. |
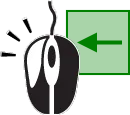 |
Select Touching - click and drag a green rectangle from right to left to select all visible, unlocked objects that touch the selection rectangle. |
Extending the Selection
A common situation is needing to select many objects that are touching, for example, the track segments in a routed net or the connection lines in an un-routed net. It is relatively easy to select a set of track segments that run parallel to each other using the Select Touching technique just described, but interactively selecting entire routes can be difficult.
However, this can easily be achieved by selecting one or more track segments, then extending the selection to include touching track segments. This is done using the Tab key as demonstrated in the video below.
To restrict the selection process to only select connection lines, hold the Alt key as you click or click-and-drag.
Demonstration of Routing Selection Techniques
Demonstration of the selection techniques.
Other Interactive Routing Options and Features
There are a number of other options for the interactive router that are configured on the PCB Editor - Interactive Routing page of the Preferences dialog. It is important to understand the role of these options to get the maximum benefit from the Interactive Router.
Automatically Terminate Routing
- Enable this option to automatically drop the current net when the target pad is reached. If this option is not enabled, use the Right Mouse button or Esc key to drop the current connection (typically this option is enabled).
Automatically Remove Loops
- An existing route path can be redefined by simply routing a new path. Start interactively routing anywhere along the existing route path, route the new path, returning to meet the old path where required. As soon as the new path meets the existing path, all segments in the redundant loop are automatically removed if the Automatically Remove Loops option is enabled (typically this option is enabled).
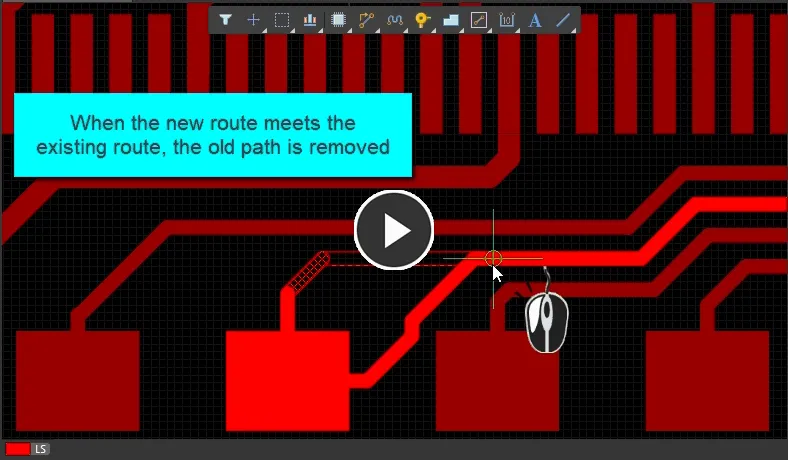
To re-route, simply route the new path. When the new route comes back to meet the existing route, a loop is created. Altium Designer will automatically remove this if Loop Removal is enabled.
- Note that certain nets may require loops (multiple paths to the same point), such as a power or ground net. For these nets, the Automatically Remove Loops feature can be selectively disabled by double-clicking on the net name in the PCB panel (set the panel mode to Nets) to open the Edit Net dialog in which the Remove Loops option can be turned off for only that net.
- Loop Removal - press the Shift+D shortcut while routing to switch to allow loops mode. The interactive router will remain in this mode until toggled off (toggle feature only available during interactive routing). Existing loops will be retained if loop removal is re-enabled and a net containing loops continues to be re-routed.
Routing Gloss Effort
- As the cursor is moved during interactive routing, the routing engine continually attempts to find the shortest path from the last click location up to the current cursor location. How well it can smooth the routing and reduces the number corners is determined by the Routing Gloss Effort.
- The current Routing Gloss Effort setting is displayed on the Status bar. Use the Ctrl+Shift+G shortcut to cycle the setting. Note that the stronger the setting, the fewer corners in the final route. The current mode is shown in the Heads Up display and on the Status bar.
- Gloss can also be temporarily inhibited during interactive routing while holding the Ctrl+Alt keys.
- Glossing is a calculation and an intensive task that runs in the background. It can affect the performance of the Interactive Router particularly when routing multiple nets simultaneously. The stronger the Gloss setting, the more time it takes to perform the calculations.
Look Ahead Behavior
- During interactive routing for the net currently being routed, the track segments are either displayed as hatched or hollow (empty). All hatched segments are placed with the next mouse click.
- The hollow segment is called the Look Ahead segment. Its purpose is to allow designers to plan ahead, i.e. to consider where the next segment might be placed without needing to commit to it. The Look Ahead mode is toggled on and off using the 1 shortcut key (while routing).
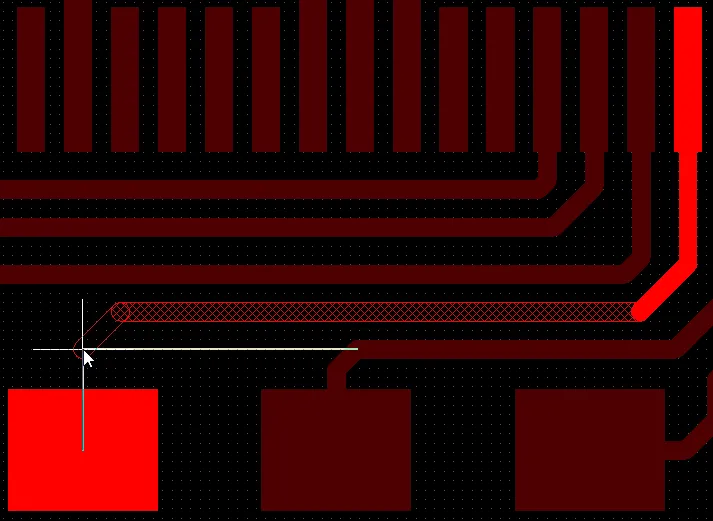
The hollow or empty segment is called the Look Ahead segment. Use it to plan where future segments will be placed.
Press the 1 shortcut during routing to toggle the Look Ahead mode on and off.
Shortcuts Available During Interactive Routing
- Use * on the numeric keypad to switch to the next available routing layer and insert a via.
- Hold Ctrl+Shift while scrolling the mouse wheel to cycle to the next available routing layer and insert a via. Each mouse wheel click moves one layer.
- Use Shift+R to cycle through the available routing conflict resolution modes.
- Use Shift+Spacebar to cycle available corner modes (learn more). For the arc in corner options, use the "," and "." keyboard buttons to decrease or increase the arc size.
- Spacebar toggles the direction of the last corner.
- Use Backspace to "rip up" the last-placed segment(s).
- Use Shift+W to open the Choose Width dialog to change the routing width.
- To switch to the next available signal layer and insert a via:
- Press the * key on the numeric keypad, or
- Use the Ctrl+Shift+Wheel Scroll shortcut combination.
- If you click to start routing from a thru-hole pad or a via and realize you are on the wrong layer, press the L shortcut to step through the available signal layers without adding a via.
- Use Ctrl+Click to instruct the interactive router to attempt to automatically complete the current route.
- Press Shift+F1 while routing to display the interactive routing shortcuts.
- Commands available during a layer change are:
- Use Ctrl+L to open a list of available layers then click to select the target layer.
- Use the 1 to 10 number pad keys to switch immediately to that layer number.
- Open the Properties panel to display a Z-plane view of the via that will be used for the layer change.
For a complete list of shortcuts for all of the editors, refer to the Shortcut Keys article.
Where to Next?