Tutorial Steps
Created: декабря 16, 2024 | Updated: сентября 13, 2018
This page contains the contents of the collapsible sections of the From Idea to Manufacture - Driving a PCB Design through CircuitStudio tutorial.
Adding a schematic
- On the ribbon, click the Home | Project | Project » Add New Schematic menu entry. A blank schematic sheet named
Sheet1.SchDoc
will open in the design window and an icon for this schematic will appear linked to the project in the Projects panel under the Source Documents folder icon. - To save the new schematic sheet, select File » Save As. The Save As dialog will open, ready to save the schematic in the same location as the project file. Type the name Multivibrator in the File Name field then click Save. Note that files stored in the same folder as the project file itself (or in a child/grandchild folder) are linked to the project using relative referencing, and files stored in a different location are linked using absolute referencing.
- Since you have added a schematic to the project, the project file also has changed. Right-click on the project filename in the Projects panel then select Save Project to save the project.
Configuring the Document Options
- On the ribbon, click Project | Content | Document Options to open the Document Options dialog.
- For this tutorial, the only change that needs to be made is to set the sheet size to A4 in the Standard Styles field of the Sheet Options tab of the dialog.
- Confirm that both the Snap and Visible Grids are set to 10.
- Click OK to close the dialog and update the sheet size.
- To make the document fill the viewing area, click View | Zoom Document.
- Save the schematic by selecting File » Save (shortcut: Ctrl+S).
Searching through libraries
- If it is not visible, display the Libraries panel (View | System | Libraries).
- Press the Search button in the Libraries panel to open the Libraries Search dialog, as shown above.
- Ensure that the dialog options are set as follows:
- For the first Filter row, the Field is set to
Name
, the Operator is set tocontains
, and the Value is3904
. - The Scope is set to Search in
Components
and Libraries on path. - The Path is set to point to the installed Altium libraries, which will be similar to
C:\Users\Public\Documents\Altium\CS\Library
.
- For the first Filter row, the Field is set to
- Click the Search button to begin the search. The Query Results are displayed in the Libraries panel. There should be one component found, as shown in the image below. It may be listed multiple times, depending on how many models it has linked to it.
- You can only place components from Libraries that are installed in the software. If you attempt to place from a library that is not currently installed, you will be asked to Confirm the installation of that library when you attempt to place the component.
Finding and Placing the Transistors
- Select View | Zoom | Zoom Document (shortcut: V, A) to ensure your schematic sheet takes up the full window.
- Using the search techniques just described, locate the transistor BC547 in the Vaults panel.
- When you search the Vault, it will first cluster the results to show the folders that contain possible components. For the transistor search, all results are in the same folder titled
General Purpose Transistors
. Click the hyperlink to open the search results for that folder then click theCMP-1048-01437-1
Item. - That component will be presented in the Vaults panel, where you can display the Preview at the bottom and examine the symbol, footprint and component parameters (you might need to resize the lower section to display all of the Preview content).
- Right-click on the transistor's Item-Revision number to display the context menu (as shown above), then select Place CMP-1048-01437-1 from the menu. The cursor will change to a cross hair and you will have an image of the transistor floating on your cursor. You are now in part placement mode. If you move the cursor around, the transistor will move with it.
Do not place the transistor yet!
- Before placing the part on the schematic you can edit its properties, which can be done for any object floating on the cursor. While the transistor is still floating on the cursor, press the Tab key to open the Component Properties dialog. Set up the dialog to appear as shown below.
- In the Properties section of the dialog, type in the Designator
Q1
. - Enable the Visible checkbox for the Comment field.
- Leave all other fields at their default values then click OK to close the dialog.
- Move the cursor, with the transistor symbol attached, to position the transistor a little to the left of the middle of the sheet. Note the current snap grid that is displayed on the left of the Status bar near the bottom of the application. It defaults to 10; press the G shortcut to cycle through the available grid settings during object placement. It is strongly advised to keep the snap grid at 10 or 5 to keep the circuit neat and make it easy to attach wires to pins. For a simple design such as this, 10 is a good choice.
- Once you are happy with the transistor's position, left mouse click or press Enter on the keyboard to place the transistor onto the schematic.
- Move the cursor and you will find that a copy of the transistor has been placed on the schematic sheet, but you are still in part placement mode with the part outline floating on the cursor. This feature allows you to place multiple parts of the same type. Now on to placing the second transistor. This transistor is the same as the previous one, so there is no need to edit its attributes before it is placed. The software will automatically increment the component designator when you place multiple instances of the same part. In this case, the next transistor will automatically be designated Q2.
- If you refer to the rough schematic diagram shown before, you will notice that Q2 is drawn as a mirror of Q1. To flip the orientation of the transistor that is floating on the cursor, press the X key on the keyboard. This flips the component horizontally (along the X axis).
- Move the cursor to position the part to the right of Q1. To position the component more accurately, press the PgUp key twice to zoom in two steps. You should now be able to see the grid lines.
- Once you have positioned the part, left mouse click or press Enter to place Q2. Once again, a copy of the transistor you are "holding" will be placed on the schematic and the next transistor will be floating on the cursor ready to be placed.
- Since all the transistors have been placed, exit part placement mode by clicking the right mouse button or pressing the Esc key. The cursor will revert back to a standard arrow.
Finding and Placing the Resistors
- Using the search techniques just described, search for a suitable
100K 5% 0805
resistor in the Vaults panel. The search should return the Item CMP-1013-00122-1. - Right-click on the resistor's Item number to display the context menu, then select Place CMP-1013-00122-1 from the menu.
- While the resistor is still floating on the cursor, press the Tab key to open the Component Properties dialog.
- In the Properties section of the dialog, type in the Designator
R1
. - Enable the Visible checkbox for the Comment field.
- Ensure that the footprint Model is set to
RESC0805(2012)_N
. Using the drop-down next to the model name, you will see that there are three footprint models attached to this component, IPC Low Density (_M
), IPC Medium Density (_N
) and IPC High Density (_L
). The footprint selected will be transferred to the PCB during design synchronization. - Leave all other fields at their default values then click OK to close the dialog; the resistor will be floating on the cursor.
- Press the Spacebar to rotate the component in 90° increments until it has the correct orientation.
- Position the resistor above and to the left of the base of Q1 (refer to the schematic diagram shown earlier) then click the left mouse button or press Enter to place the part.
- Next place the other 100k resistor, R2, above and to the right of the base of Q2. The designator will automatically increment when you place the second resistor.
- Exit part placement mode by clicking the right mouse button or pressing the Esc key. The cursor will revert back to a standard arrow.
- The remaining two resistors, R3 and R4, have a value of 1K; search for a suitable
1K 5% 0805
resistor in the Vaults panel. - This search will return all resistors whose values start with 1K, including 1K1, 1K2, 1K3, etc. Using the Description field, click in the search results to open the
1K 5% 0805
resistor, then right-click and Place it. - Using the steps just given, set the Designator to
R3
, enable the visibility of the Comment, and set the footprint Model toRESC0805(2012)_N
. - Position and place R3 directly above the Collector of Q1, then place R4 directly above the Collector or Q2 as shown in the image above.
- Right-click or press Esc to exit part placement mode.
Finding and Placing the Capacitors
- Return to the Vaults panel and search for a suitable
22nF 16V 0805
capacitor. The search will return a number of potential capacitors. Click on ItemCMP-1036-04042-1
to use in this design. - Right-click on the capacitor's Item number then select Place CMP-1036-04042-1 from the menu.
- While the resistor is still floating on the cursor, press the Tab key to open the Component Properties dialog.
- In the Properties section of the dialog, type in the Designator
C1
. - Enable the Visible checkbox for the Comment field.
- Ensure that the footprint Model is set to
CAPC0805(2012)145_N
. - Leave all other fields at their default values then click OK to close the dialog. The capacitor will be floating on the cursor.
- Press the Spacebar to rotate the component in 90° increments until it has the correct orientation.
- Position the capacitor above the transistors but below the resistors (refer to the schematic diagram shown earlier) then click the left mouse button or press Enter to place the part.
- Position and place capacitor C2.
- Right-click or press Esc to exit placement mode.
Finding and Placing the Connector
- The last component to be placed is the connector, which is located in Miscellaneous Connectors.IntLib. This integrated library is normally already installed. If it is not, install it then select it at the top of the Libraries panel.
- The connector is a two-pin header; type
header
into the Libraries panel filter field. Note that the wildcard * is not used for this search since you are only searching for components that start with the stringheader
. If the wildcard is included at the start of the search string, all components that have the stringheader
anywhere in their name or description will be returned. - Select
Header 2
from the list then click the Place button. - While it is floating on the cursor, press Tab to edit the attributes; set the Designator to
Y1
and check that the PCB footprint model is HDR1X2. - Before placing the connector, press X to flip it horizontally so that it is in the correct orientation. Click to place the connector on the schematic as shown in the image above.
- Right-click or press Esc to exit part placement mode.
- Save your schematic (Ctrl+S).
Wiring the schematic
- To make sure you have a good view of the schematic sheet, press the PgUp key to zoom in or PgDn to zoom out. Alternatively, hold down the Ctrl key and roll the mouse wheel to zoom in/out or hold Ctrl + Right Mouse button down and drag the mouse up/down to zoom in/out. There are also a number of useful View commands in the right-click View submenu, such as Fit All Objects (Ctrl+PgDn).
- First, wire the lower pin of resistor R1 to the base of transistor Q1 in the following manner. Click the
button (Home | Circuit Elements | Wire) to enter the wire placement mode. The cursor will change to a cross hair.
- Position the cursor over the bottom end of R1. When you are in the right position, a red connection marker (large cross) will appear at the cursor location. This indicates that the cursor is over a valid electrical connection point on the component.
- Click the Left Mouse Button or press Enter to anchor the first wire point. Move the cursor and you will see a wire extend from the cursor position back to the anchor point.
- Position the cursor over the base of Q1 until you see the cursor change to a red connection marker. Click or press Enter to connect the wire to the base of Q1. The cursor will release from that wire.
- Note that the cursor remains a cross hair, indicating that you are ready to place another wire. To exit placement mode completely and go back to the arrow cursor, you would Right-Click or press Esc again - but don't do this just now.
- Next, wire from the lower pin of R3 to the collector of Q1. Position the cursor over the lower pin of R3 then click or press Enter to start a new wire. Move the cursor vertically till it is over the collector of Q1 then click or press Enter to place the wire segment. Again, the cursor will release from that wire and you remain in wiring mode, ready to place another wire.
- Wire up the rest of your circuit as shown in the animation above.
- When you have finished placing all the wires, right-click or press Esc to exit placement mode. The cursor will revert to an arrow.
Adding net labels
- Click the
button (Home | Circuit Elements | Net Label). A net label will appear floating on the cursor.
- To edit the net label before it is placed, press Tab key to open the Net Label dialog.
- Type
12V
in the Net field then click OK to close the dialog. - Place the net label so that the bottom left corner of the net label touches the upper most wire on the schematic as shown in the image below. The cursor will change to a red cross when the net label is correctly positioned to connect to the wire. If the cross is light gray, it means there will not be a valid connection made.
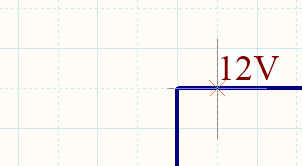
The net label in free space (left image) and positioned over a wire (right image); note the red cross.
- After placing the first net label, you will still be in net label placement mode. Press the Tab key again to edit the second net label before placing it.
- Type
GND
in the Net field then click OK to close the dialog. - Place the net label so that the bottom left of the net label touches the lower most wire on the schematic as shown in the image below. Right-click or press Esc to exit net label placement mode.
- Save your schematic and the project as well.
Changing the Connection Matrix
- To change one of the settings, click the colored box; it will cycle through the four possible settings. Note that you can right-click in the matrix area to display a menu that lets you toggle all settings simultaneously, including an option to restore all to their Default state (handy if you have been toggling settings and cannot remember their default state).
- Your circuit contains only Passive Pins (on resistors, capacitors and the connector) and Input Pins (on the transistors). Let's change this so that the connection matrix detects unconnected passive pins. Find the Passive Pin row on the right. Look across the column labels to find Unconnected. The square where these entries intersect indicates the error condition when a passive pin is found to be unconnected in the schematic. The default setting is green, indicating that no report will be generated.
- Click on this intersection box until it turns Orange (as shown in the image above) so that an error will be generated for unconnected passive pins when the project is compiled. You will purposely create an instance of this error to check this later in the tutorial.
Compiling and checking for errors
- To compile the Multivibrator project, select Home | Project | Project » Compile.
- When the project is compiled, all warnings and errors are displayed in the Messages panel. The panel will only appear automatically if there are errors detected (not when there are only warnings). To open it manually, click View | System | Messages.
- If your circuit is drawn correctly, the Messages panel should not contain any errors, only the message Compile successful, no errors found. If there are errors, work through each one, checking your circuit and ensuring that all wiring and connections are correct.
You will now deliberately introduce an error into the circuit and recompile the project:
- Click on the Multivibrator.SchDoc tab at the top of the design window to make the schematic sheet the active document.
- Click in the middle of the wire that connects R1 to the base wire of Q1. Small, square editing handles will appear at each end of the wire and the selection color will display as a dotted line along the wire to indicate that it is selected. Press the Delete key on the keyboard to delete the wire.
- Recompile the project (Home | Project | Project » Compile) to check for errors. The Messages panel will display warning messages indicating you have unconnected pins in your circuit.
- The Messages panel is divided horizontally into two regions, as shown in the image above. The upper region lists all messages, which can be saved, copied, cross probed to, or cleared via the right-click menu. The lower region details the warning/error currently selected in the upper region of the panel.
- When you double-click on an error or warning in either region of the Messages panel, the schematic view will pan and zoom to the object with the error.
Before you finish this section of the tutorial, let's fix the error in our schematic.
- Make the schematic sheet the active document.
- Undo the delete action (Ctrl+Z) to restore the deleted wire.
- To check that there are no longer any errors, recompile the project (Home | Project | Project » Compile).The Messages panel should show no errors.
- Save the schematic and the project file as well.
Adding a New Board to the Project
- A new PCB can be added to the project using the Home | Project | Project » Add new PCB command.
- The PCB will appear as a Source Document in the Project as shown below. Right-click on the PCB icon in the Projects panel to select the Save As command and name it
Multivibrator.CSPcbDoc
. Note that you do not need to enter the file extension in the Save As dialog; this is automatically appended.
- Adding the PCB has changed the project. Save the project (right-click on the project filename in the Projects panel then select Save Project).
Setting the Origin and the Grid
- There are two origins used in the software: the Absolute Origin, which is the lower left of the workspace, and the user-definable Relative Origin, which is used to determine the current workspace location. Before setting the origin, keep zooming in to the lower left of the current board shape until you can easily see the grid. To do this, position the cursor over the lower-left corner of the board shape then press PgUp until both the Coarse and Fine grids are visible as shown in the images below.
- To set the Relative Origin, select Home | Grids and Units | Origin » Set, position the cursor over the bottom left corner of the board shape then left click to set it.
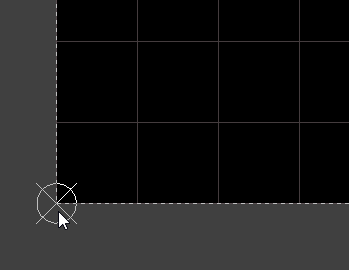
Select the command, position the cursor over the lower-left corner of the board shape (left image) then click to define the origin (right image).
- The next step is to select a suitable snap grid, which is summarized in the table above. The grid is set in the Grids and Units section of the Home tab of the Ribbon. During the course of design, it is quite common to change grids. For example, you might use a coarse grid during component placement, and a finer grid for routing. Grids can be changed by selecting a new value from the Snap Grid drop-down list or typing the required value directly in the Snap Grid field then pressing Enter to have your value accepted.
- For this tutorial, you will be using a Metric grid; click the
button to switch to Metric.
- The first grid you will be using is
5mm
; enter this value into the Snap Grid field.
Redefining the Board Shape
- The default board shape is 4x4 inch. For this tutorial, the board size is 30mm x 30mm.
- To zoom back out and show the all of the workspace currently being used, click View | Zoom | Zoom All (Ctrl+PgDn). Your design should look much like the left image below.
- The next step is to change the board shape to 30mm x 30mm. Your choice now is to either redefine the board shape (draw it again, or edit the existing board shape. For a simple square or rectangle, it is more efficient to edit the existing board shape. To do this, select Home | Board | Board Shape » Edit Board Shape.
- The board display will change, with the shape shown in green. Editing handles will appear at each corner and the center of each edge, as shown below.
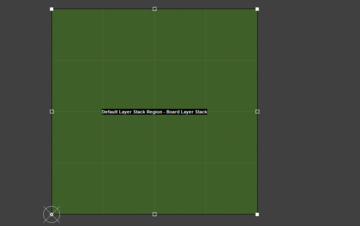
- The objective is to resize the shape to create a 30mm by 30mm board. The Coarse visible grid is 25mm (5x the snap grid), and the Fine visible grid is 5mm - this will be used as a guide. You can now either slide the upper and right edges down and in to create the correct size or move three of the corners in, leaving the one that is at the origin in its current location.
- To slide the top edge down, position the cursor over the edge (but not over a handle), then when the cursor changes to a double-headed arrow, click and hold, then drag the edge to the new location so that the Y cursor location is 30mm on the Status bar.
- Repeat the process to move the right-hand edge in, positioning it when the X cursor location is 30mm on the Status bar.
The board shape has been resized to 30mm x 30mm as indicated by the current grid locations shown on the Status bar.
- Click anywhere in the workspace to drop out of board shape editing mode.
- Save the board.
Transferring the design from schematic capture to PCB layout
- Ensure Multivibrator.SchDoc is the active document.
-
Select Home | Project | Project » Update PCB Document Multivibrator.CSPcbDoc from the Ribbon. The project will compile and the Engineering Change Order dialog will open.
An ECO is created for each change that needs to be made to the PCB so that it matches the schematic.
- Click on Validate Changes. If all changes are validated, a green check will appear next to each change in the Status list. If the changes are not validated, close the dialog, check the Messages panel and resolve any errors.
- Click on Execute Changes to send the changes to the PCB editor.
- When completed, the target PCB opens with the Engineering Change Order dialog open on top of it, and the Done column entries become checked as shown in the image below.
- Click to Close the dialog and complete the transfer process.
- The components will have been positioned outside of the board, ready for placing on the board. There are a few steps before starting the component process, such as configuring the placement grid, the layers and the design rules.
Configuring the Layer Visibility
- Open the View Configurations dialog (View | View | Switch to 3D » View Configurations » View Configuration).
- On the Board Layers And Colors tab, confirm that the two signal layers are visible.
- Note that this dialog is where you control the display of the mask layers, the silkscreen layers and the system layers, such as DRC and grids.
- To have less visual "clutter" during placement and routing, disable the display of the Mechanical Layers, all of the Mask Layers, and the Drill Guide and Drill Drawing layers.
- Switch to the View Options tab.
- Confirm that the Show Pad Nets option is enabled, and the Net Names on Tracks Display is set to
Single and Centered
. - Click OK to accept the settings and close the dialog.
Configuring the board layer stack
- Open the Layer Stack Manager. For a new board, the default stack comprises: a dielectric core, two copper layers, as well as the top and bottom soldermask (coverlay) and overlay (silkscreen) layers as shown in the image above.
- New layers and planes are added below the currently selected layer, which is done using the Add Layer button or the right-click menu.
- Layer properties, such as material, copper thickness and dielectric properties, are included when a Layer Stack Table is placed and are also used for signal integrity analysis. Double-click in a cell to configure that setting. For example, the Thickness settings shown in the image below have been changed slightly to more suitable metric values.
- When you have finished exploring the layer stack options, restore the values to those shown in the image below then click OK to close the dialog.
Defining the component placement snap grid
- Click Home | Grids and Units | Properties to open the Cartesian Grid Editor dialog. You can also access the Cartesian Grid Editor dialog directly using the Ctrl+G shortcut keys.
- Type the value
1mm
into the Step X field. Because the X and Y fields are linked, there is no need to define the Step Y value. - To make the grid visible at lower zoom levels, set the Multiplier to
5x Grid Step
. To make it easier to distinguish between the two grids, set the Fine grid to display as lighter coloredDots
. - Click OK to close the dialog.
Configuring the Routing Width Rule for the signal nets
- With the PCB as the active document, open the PCB Rules and Constraints Editor.
- Each rules category is displayed under the Design Rules folder (left hand side) of the dialog. Double-click on the Routing category to expand the category and see the related routing rules. Then double-click on Width to display the currently defined width rules.
- Click once on the existing Width rule to select it. When you click on the rule, the right hand side of the dialog displays the settings for that rule including: the rule's Where the Object Matches (also referred to as the rule's scope - what you want this rule to target) in the top section and the rule's Constraints below that.
- Since this rule is to target the majority of nets in the design (the signal nets), confirm that the Where the Object Matches setting is set to
All
. - The settings in this rule are the defaults for a new PCB. Edit the Min Width, Preferred Width & Max Width values and set them to 0.25mm. Note that the settings are reflected in the individual layers shown at the bottom of the dialog. You can also configure the requirements on a per-layer basis.
- The rule is now defined. Click Apply to save it and keep the dialog open.
Adding Routing Width Rules for the power nets
- The next step is to add and configure two new design rules to specify the routing width for the power nets. To add and configure these rules, open the PCB Rules and Constraints Editor.
- With the existing Width rule selected in the Design Rules tree on the left of the dialog, right-click then select New Rule to add a new Width constraint rule.
- A new rule named Width_1 appears. Click on the new rule in the Design Rules tree to configure its properties.
- Click in the Name field on the right and enter the name
Width_12V
in the field. - In the Where the Object Matches setting, select Net from the drop-down, then choose the 12V net from the second drop-down as shown below.
- The last step is to set the Constraints for the rule. Edit the Min Width / Preferred Width / Max Width values
0.25
/0.5
/0.5
, respectively, to allow power net routing widths in the range 0.25mm to 0.5mm, as shown below.
- Repeat this sequence of steps to define another Routing Width Design Rule that targets the
GND
net, with the same Constraints values. The easiest way to do this is to use the Duplicate Rule command in the right-click menu, then change the Name of this new rule toWidth_GND
, and the Net toGND
. - Click Apply to save the rules and keep the dialog open.
Defining the Electrical Clearance Constraint
- Expand the Electrical category in the tree of Design Rules, then expand the Clearance rule-type.
- Click to select the existing Clearance constraint. Note that this rule has two Full Query fields, that is because it is a Binary rule. The rules engine checks each object targeted by the setting Where the First Object Matches and checks it against the objects targeted by the Where the Second Object Matches setting to confirm that they satisfy the specified Constraints settings. For this design, it is suitable to define a single clearance between
All
objects. - In the Constraints region of the dialog, set the Minimum Clearance to
0.25mm
. - Click Apply to save the rule and keep the dialog open.
Defining the Routing Via Style Design Rule
- Expand the Routing category in the tree of Design Rules then select the default RoutingVias design rule under Routing Via Style.
- Since it is highly likely that the power nets can be routed on a single side of the board, it is not necessary to define a routing via style rule for signal nets and another routing via style rule for power nets. Edit the rule settings to the values suggested earlier in the tutorial, that is a Via Diameter =
1mm
and a Via Hole Size =0.6mm
. Set all fields (Minimum, Maximum, Preferred) to the same size. Note that you can press Tab on the keyboard to move from one dialog field to the next. - Click OK to close the PCB Rules and Constraints Editor.
- Save the PCB file.
Setting the component positioning options
- Select File » System Preferences to open the Preferences dialog.
- Open the PCB Editor - General page of the dialog, in the Editing Options section, make sure the Snap To Center option is enabled. This ensures that when you "grab" a component to position it, the cursor will hold the component by its reference point.
- Note the Smart Component Snap option. If this is enabled, you can force the software to snap to a pad center instead of the reference point by clicking and holding closer to the required pad than the component's reference point. This is very handy if you require a specific pad to be on a specific grid point. It can work against you if you are working with small surface mount components though, as it can make it harder to "grab" them by their reference point.
Positioning the components
- Zoom to display the board and the component. One way to do this is to zoom out (PgDn) so the board and the components are all visible, right-click and choose View » View Area then click to define the top left and bottom right of the exact area you want to view.
- The components will be positioned on the current Snap Grid. For a simple design such as this, there are no specific design requirements that dictate what placement grid should be used. As the designer, you decide what a suitable placement grid would be. To simplify the process of positioning the components, you can work with a coarse placement grid, for example, 1mm. Confirm that the Snap Grid is set to
1mm
in the Home tab of the Ribbon. - The components in the tutorial can be placed as shown in the image above. To place connector
Y1
, position the cursor over the middle of the outline of the connector then Click-and-Hold the left mouse button. The cursor will change to a cross hair and jump to the reference point for the part. While continuing to hold down the mouse button, move the mouse to drag the component. - Position the footprint towards the left-hand side of the board (ensuring that the whole of the component stays within the board boundary) as shown in the figure above.
- When the connector component is in position, release the mouse button to drop it into place. Note how the connection lines drag with the component.
- Reposition the remaining components using the figure above as a guide. Use the Spacebar to rotate components (in increments of 90º counterclockwise) as you drag them so that the connection lines are as shown in the figure.
- Component text can be repositioned in a similar fashion - click-and-drag the text then press the Spacebar to rotate it.
- The PCB editor also includes powerful interactive placement tools. Let's use these to ensure that the four resistors are correctly aligned and spaced.
- Holding the Shift key, click on each of the four resistors to select them or click and drag the selection box around all four of them. A shaded selection box will display around each of the selected components in the color set for the system color Selections (set in the 2D System Colors dialog).
- Right-click on any of the selected components then choose Align » Align to open the Align Objects dialog.
- Select Space Equally in the Horizontal section and Bottom in the Vertical section; click OK to apply these changes. The four resistors are now aligned (with the lowest component) and equally spaced.
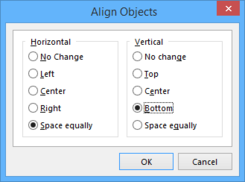
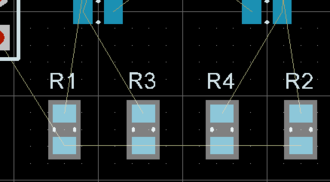
- Click elsewhere in the design window to de-select all the resistors. If required, you also can align the capacitors and transistors, although this might not be required since you currently have a coarse Snap Grid.
Preparing for interactive routing
- Set the Routing Conflict Resolution Current Mode drop-down to
Stop At First Obstacle
. You can cycle through the enabled modes interactively as you route by pressing Shift+R. - In the Interactive Routing Options region, confirm that the Automatically Remove Loops option is enabled. This option allows you to change existing routing by routing an alternate path, i.e. you route a new path until it meets the old path (creating a loop), then right-click to indicate it is complete. The software then automatically removes the old, redundant part of the routing.
- Confirm that the Interactive Routing Width / Via Size Sources options are both set to Rule Preferred.
- Set the Snap Grid to
0.25mm
in the Home | Grids and Units | Snap Grid.
Interactively routing the board
- Check which layers are currently visible by looking at the layer tabs at the bottom of the workspace. If the Bottom Layer is not visible, press the L shortcut to open the View Configurations dialog and enable the Bottom Layer.
- Click on the Top Layer tab at the bottom of the workspace to make it the current, or active layer, on which to route.
- It is often easier to route in single layer mode. You can press Shift+S to toggle to in and out of single layer mode.
- Click Home | Routing | Route » Interactive Routing or right-click then choose Interactive Routing from the context menu. The cursor will change to a crosshair indicating you are in interactive routing mode.
- Position the cursor over the lower pad on connector Y1. As you move the cursor close to the pad, it will automatically snap to the center of the pad; this is the Snap To Object Hotspot feature pulling the cursor to the center of the nearest electrical object (configure the Range of attraction in the Board Options dialog). Sometimes the Snap To Object Hotspot feature pulls the cursor when you do not want it to. In this situation, press the Ctrl key to temporarily inhibit this feature.
- Left-Click or press Enter to anchor the first point of the track.
- Move the cursor towards the bottom pad of the resistor R1 then click to place a vertical segment. Note how track segments are displayed in different ways (as shown in the image below). During routing, the segments are shown as:
- Solid - the segment has been placed.
- Hatched - hatched segments are proposed but uncommitted; they will be placed when you left-click.
- Hollow - this is referred to as the look-ahead segment. It allows you to work out where the last proposed segment should end. This segment is not placed when you click. The look-ahead mode can be toggled on/off using the 1 shortcut during routing.
- Manually route by Left-Clicking to commit track segments, finishing on the lower pad of R1. Note how each mouse click places the hatched segment(s). For the connection that you are currently routing, press Backspace to rip up (remove) the last-placed segment.
- Rather than routing all the way to the target pad, you can also press Ctrl+Left Click to use the Auto-Complete function and immediately route the entire connection. Auto-complete behaves in the following way:
- It takes the shortest path, which may not the best path since you need to always consider paths for other connections yet to be routed. If you are in Push mode (shown on the Status bar when routing), Auto-complete can push existing routes to reach the target.
- On longer connections, the Auto-Complete path may not always be available since the routing path is mapped section by section and, therefore, complete mapping between source and target pads may not be possible.
- You also can Auto-complete directly on a pad or connection line.
- Continue to route all the connections on the board.
- Use the techniques detailed above to route between the other components on the board. The simple animation above shows the board being interactively routed.
- There is no single solution to routing a board, therefore, it is inevitable that you will want to change the routing. The PCB editor includes features and tools to help you do this and they are discussed in the following sections.
- Save the design when you are finished routing.
Exploring the capabilities of the autorouter
- Un-route the board by selecting Home | Routing | Unroute » All from the Ribbon.
- Select Tools | Autoroute | Autoroute » All. The Situs Routing Strategies dialog opens. The top region of the dialog displays the Routing Setup Report; warnings and errors are shown in red. Always check for warnings and errors! The lower half of the dialog shows the available Routing Strategies; the selected one will be highlighted. For this board, it should default to the Default 2 Layer Board strategy.
- Click the Route All button in the Situs Routing Strategies dialog. The Messages panel displays the process of the autorouting. Because it routes your board directly in the PCB editing window, there is no need to wrestle with exporting and importing route files.
- To route the board single-sided, click the Edit Layer Directions button in the Situs Routing Strategies dialog and modify the Current Setting field. Alternatively, you can modify the Routing Layers design rule.
- Interestingly, the autorouter prefers a challenging board, often giving better results on a dense, more complex design than on a simple board. To improve the quality of the finished result, select Autoroute » All again, except this time select the Cleanup routing strategy. This strategy will attempt to straighten the routes, reducing the number of corners. You can run the Cleanup strategy multiple times if required. If nothing changes you might want to interactively re-route a connection in a convoluted pattern, then try the Cleanup strategy.
- If you want to keep the autorouting results, save the PCB document. Otherwise, use Undo or close/open to return the board to the required routed state.
Preparing for a managed release
- The Generate Output Files dialog can be opened at any time with a schematic open, a PCB open, or no document open. Click the
button on the Project tab to open the dialog. Note that when you open the dialog, the special file that holds the output settings is automatically created in the project folder and therefore, the project file will now be marked as modified.
- Note the list of Outputers that are included. For the tutorial, you will be using the Gerber Files outputer and the Bill of Materials outputer.
- Click Configure... associated with Gerber Files to open the Gerber Setup dialog, which will be configured in the next set of steps.
Configuring Gerber generation
- In the Generate Output Files dialog, click Configure... associated with the Gerber Files output. The Gerber Setup dialog will open as shown in the image above.
- Since the board has been designed in Metric, set the Units to Millimeters on the General tab of the dialog.
- The smallest unit used on the board is 0.25mm for the routing and clearance, but because most of the components have their reference point at their geometric center (and were placed on a 1mm grid), some of their pads will actually be on a 0.01 grid. Set the Format to 4:3 on the General tab. This ensures that the resolution of the output data is more than adequate to cover these grid locations. Note that the NC Drill file must always be configured to use the same Units and Format.
- On the Layers tab, click the Plot Layers button then select Used On. Note that mechanical layers may be enabled; these are not normally 'Gerbered' on their own. Instead they are often included if they hold detail that is required on other layers, for example, an alignment location marker that is required on every Gerber file. In this case, the Mechanical Layer(s) to Add to All Plots options on the right side of the dialog are used to include that detail with another layer. Disable any mechanical layers that were enabled in the Layers To Plot region.
- On the Advanced tab of the dialog, confirm that the Position on Film option is set to Reference to relative origin. Note: the NC Drill file must always be configured to use the same Position on Film option.
- Click OK to accept the other default settings and close the Gerber Setup dialog.
- The Gerber settings are configured. The next step is to configure other outputs. For this tutorial, you will also configure the BoM in the next set of steps.