Summary
The Interactive Properties panel provides universal editing access to the properties of documents and objects in design editors. The panel dynamically determines its content based on the document or object that is currently selected and presents specific properties and settings that relate to that document/object.
Panel Access
The Properties panel is available in all editors and can be accessed in the following ways:
- Click the Panels button at the bottom right of the design workspace, then click Properties.
- Choosing View » Panels » Properties from the main menus.
- Double-click on an object in the workspace.
- Using the F11 keyboard shortcut.
Schematic Support
When the active document is a schematic document (*.SchDoc) and no design object is selected in the design workspace, the Properties panel presents the Document Options.
The following collapsible sections contain information about the options and controls available under the panel's General tab:
Selection Filter
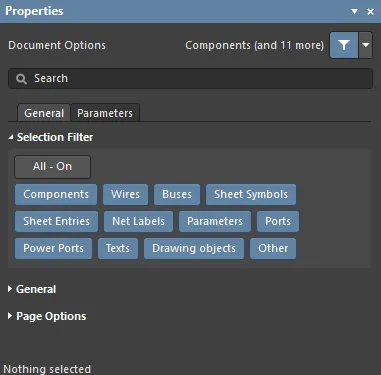
The options in this section of the panel determine which schematic objects may be selected in the workspace.
- All - On button – select to remove object filtering so that all types of objects may be selected.
- Object buttons – toggle each object button to enable/disable the ability to select that object type.
General
Page Options
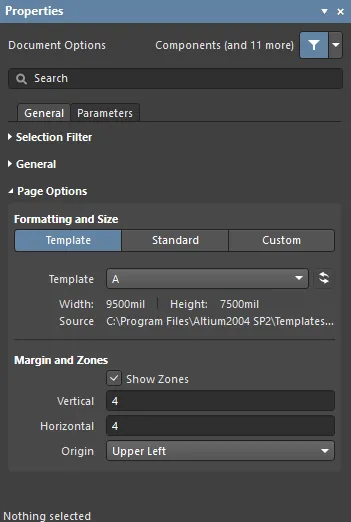
- Formatting and Size
- Template mode – set the page size and format by selecting from a range of predefined schematic sheet templates. The list includes templates found in the location specified in the Data Management - Templates page of the Preferences dialog. Note that a default schematic sheet to be used for new schematic documents can be defined in the System - New Document Defaults page of the Preferences dialog.
- Template – use the drop-down menu to select from a list of standardized page templates, and if required, use the
button to refresh the template.
- Width/Height – the dimensions of the current page size shown in the current document units (see the General section above).
- Standard mode – set the sheet size to a standard page format.
- Sheet Size – use the drop-down menu to select from a list of standard page dimensions.
- Width/Height – the dimensions of the current page size in the current document units.
- Orientation - use the drop-down to select the desired orientation.
- Title Block - enable this option to display one of two predefined title blocks on the schematic sheet. Use the associated drop-down to choose from either a Standard or ANSI title block style.
- Custom mode – set the sheet size to specified custom dimensions.
- Width – enter the required sheet width measurement.
- Height – enter the required sheet height measurement.
- Orientation - use the drop-down to select the desired orientation.
- Title Block - enable this option to display one of two predefined title blocks on the schematic sheet. Use the associated drop-down field to choose from either a Standard or ANSI title block style.
- Margin and Zones - defines the size of the sheet border graphics and its zone divisions. Uncheck the Show Zones box to hide the zone divisions in the border graphics.
- Vertical – set the number of divisions (rows) in the vertical sheet margin. The alpha-numeric zone labeling type is defined by the Origin setting.
- Horizontal – set the number of divisions (columns) in the horizontal sheet margin.
- Origin – sets which corner of the document sheet(s) the perimeter zone alpha-numeric indicators will begin from (zone position
A-1
or 1-A
).
- Margin Width – set the distance (in the current units) between the page edge and each of the four border lines as indicated by the arrows associated with each entry field.
The following collapsible section contains information about the options and controls available under the panel's Parameters tab:
Parameters
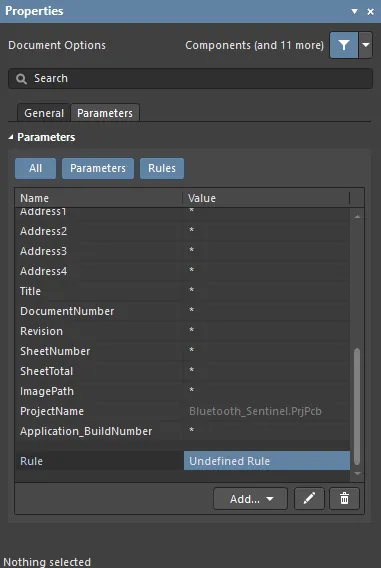
The Properties panel Parameters tab lists all available Parameters and Rules available in the current project document.
- All button - Select to view both Parameters and Rules.
- Parameters button - Select to only view Parameters.
- Rules button - Select to only view Rules.
- Parameters
- Name and Value columns – lists the available parameters grouped by type.
- Rules
- Name and Value columns – these list the current specified rules and their values.
- Add - use the drop-down menu to select to add a Parameter or a Rule. Selecting to add a new Rule will open the Choose Design Rule Type dialog to specify the type of rule to be used when adding a parameter as a rule to a supported design object in the schematic domain or a schematic document.
-
- only accessible when a rule is selected. Click to open the Edit PCB Rule dialog to edit the selected rule.
-
- click to delete the currently selected parameter or rule.
When a design object is selected, the panel will present options specific to that object type. The following table lists the object types available for placement on a schematic sheet - click a link to access the properties page for that object.
Modifying Data Strings
Using Formulas
The Properties panel has the ability to modify data strings using formulas in the Schematic Editor. Formulas and expressions offer a convenient method of modifying attribute parameters of multiple selected objects to change their location or string-based values such as the Designator and Comment. This allows you to apply a specific expression to the selected string objects. The expression can include any built-in arithmetic operators and functions that apply to strings (found in Pascal). If you want to use the current value for the attribute as part of the expression, you will need to make reference to this original value either by using the full name of the attribute or by using the exclamation character (the supported substitute for the name of the attribute currently being modified). When using attribute names, if any names contain spaces, these must be replaced by the underscore character. For example, use of the Component Designator field within a formula should be entered as Component_Designator
.
Using the Smart Edit Feature
Some parameter string fields also provide access to the Smart Edit dialog when multiple objects are selected, which is opened from the associated
button.
The Properties panel offers further support for string modification through its Smart Edit feature. Select the cell entries pertaining to the attribute that you want to modify for all required objects, right-click then choose Smart Edit from the menu that appears. The Smart Edit dialog will open.
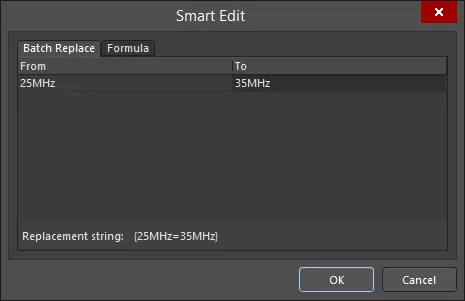
The dialog offers two methods for performing string modification accessed from the Batch Replace and Formula tabs.
Schematic Library Support
When the active document is a Schematic Library document (*.SchLib), choose the Tools » Document Options command from the main menus - the Properties panel presents the Library Options. The following collapsible sections contain information about the options and controls available:
Selection Filter
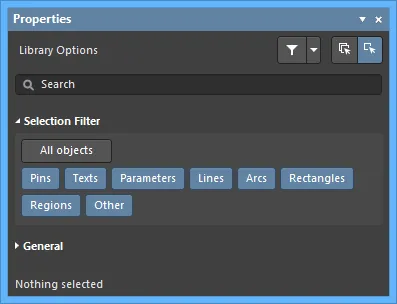
The options in this section of the panel determine which schematic library objects may be selected in the workspace.
- All Objects button – select remove object filtering so that all types of objects may be selected.
- Object buttons – toggle each object button to enable/disable the ability to select that object type.
General
When a design object is selected, the panel will present options specific to that object type. The following table lists the object types available for placement within the library workspace. Click a link to access the properties page for that object.
PCB Support
When the active document is a PCB document (*.PcbDoc) and when no design object is currently selected in the design workspace, the Properties panel presents the Board mode. The following collapsible sections contain information about the options and controls available:
Selection Filter
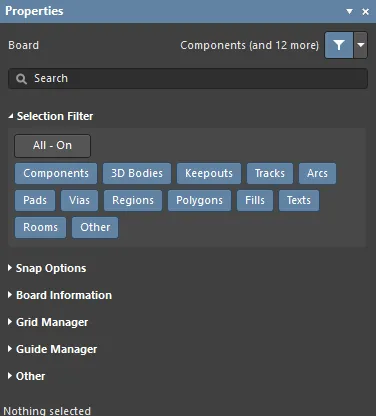
The options in this section of the panel determine which PCB objects may be selected in the workspace.
- All On button – select to remove object filtering so that all types of objects may be selected.
- Object buttons – toggle each object button to enable/disable the ability to select that object type.
Snap Options
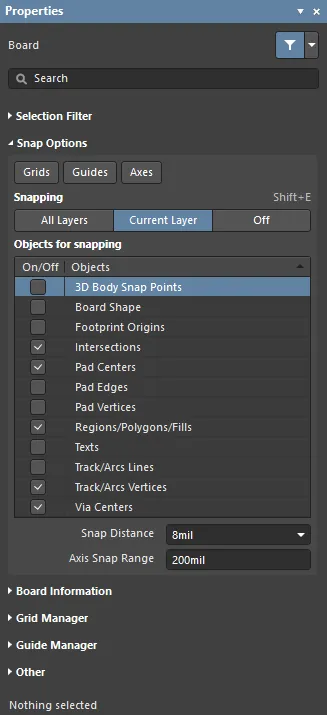
- Grids - used to toggle whether the cursor will snap to the active workspace grid. When this option is enabled the cursor will pull, or snap, to the nearest snap grid location. The active snap grid is displayed on the Status bar, and in the PCB editor Heads Up display.
- Guides - used to toggle whether the cursor will snap to manually placed linear or point Snap Guides. A Snap Guide will override the Snap Grid.
- Axes - used to toggle whether the cursor will axially-align (in either the X or Y direction) to the enabled Objects for snapping. The Axis Snap Range defines the distance within which X or Y axial-alignment will occur. A dynamic alignment guide line is displayed when alignment is achieved, from the current cursor location to the axially-aligned object snap point (hotspot).
- Snapping - select directly or use the Shift+E shortcut to select whether you want to snap to objects on:
- All Layers - enable this option to allow the cursor to snap to any electrical object on any visible layer.
- Curent Layer - enable this option to allow the cursor to only recognize and snap to objects placed on the currently selected layer.
- Off - enable this option to turn off snapping to hotspots.
- Objects for snapping
- On/Off - check to enable snapping for the desired objects.
- Objects - a list of the available objects.
- Snap Distance - when the cursor is within this distance from an enabled object snap point (and snapping is enabled for the active layer), the cursor will snap to that point.
- Axis Snap Range - when the cursor is axially-aligned and within this distance from an enabled object snap point (and the Axes feature is enabled), a dynamic guide line will display to indicate that alignment has been achieved.
Board Information
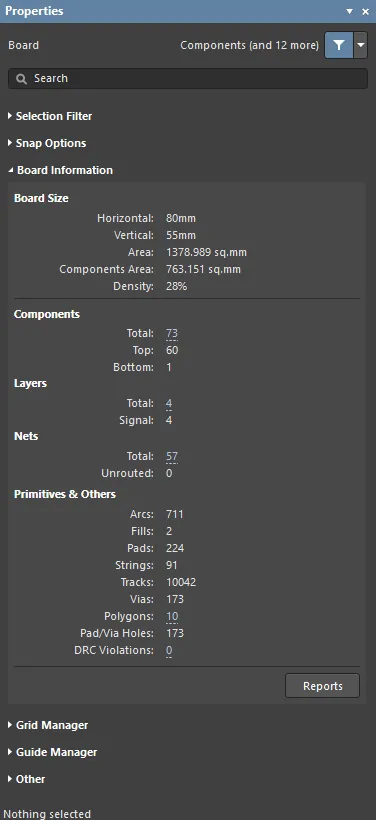
- Board Size
- Horizontal/Vertical: the overall length of the board in the horizontal (X) and vertical (Y) directions.
- Area: the area of the board as defined by the board shape (the black region).
- Components Area: the sum total area occupied by all components on the board. Refer to the Component Area topic for details on how the component area is defined.
- Density: the percentage of the board Area occupied by the Components Area.
The automatically calculated area is the area that highlights when you click to select the component. The selection area is determined from the geometries on the Courtyard layer, i.e. when that layer is not present, the combination of the geometries on the Silkscreen, 3D Body objects, and Copper layers (strings are excluded).
- Components/Layers/Nets/Primitives & Others - displays information for each listed category such as the total number of the listed item.
- Reports - click to open the Board Report dialog in which you can specify the content to be included when generating a detailed report for the board.
Grid Manager
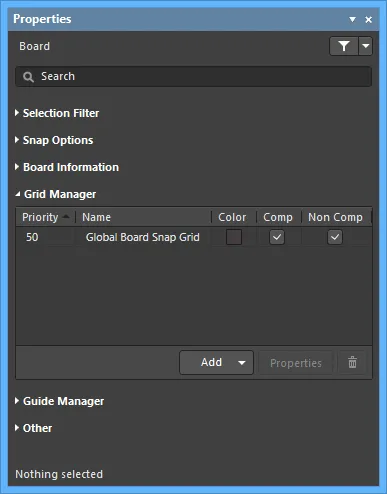
- Grid Manager - where local customized grids can be defined and managed, as well as the default Snap Grid for the board.
- Priority - in the workspace, priority is distinguished by drawing order. The highest priority grid (priority
1
) will be drawn in front of all other grids, then the grid with priority level 2
, etc., down to the default Global Board Snap Grid
, which is drawn behind all other custom grids.
- Name - displays the name of the grid.
- Color - click to open a drop-down to set/change the color of the associated grid.
- Comp - enable to apply the selected grid to only components.
- Non Comp - enable to apply the selected grid to objects that are not components.
- Add
- Add Cartesian Grid - click to add a Cartesian grid.
- Add Polar Grid - click to add a Polar grid. Polar grids enable you to more easily design non-rectangular features and boards.
- Properties - click to open the respective grid editor dialog (Cartesian Grid Editor or Polar Grid Editor) to modify properties for the selected grid.
-
- click to delete the currently selected grid.
Guide Manager
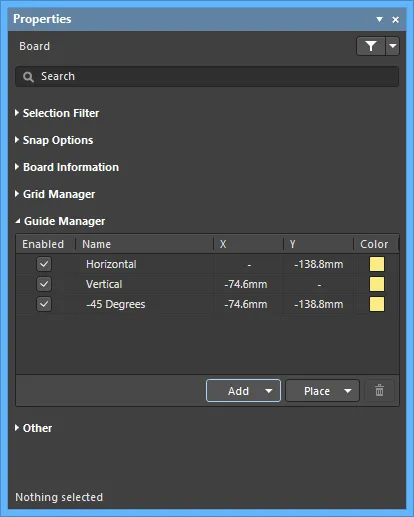
- Guide Manager - where a range of manual Snap Guides and Snap Points for the board can be defined and managed.
- Enabled - whether the guide is visible in the workspace (checked) or not (unchecked).
- Name - the name of the guide.
- X - the x-coordinate (where applicable) specified in the workspace that the guide is to pass through or point is to be located at.
- Y - the y-coordinate (where applicable) specified in the workspace that the guide is to pass through or point is to be located at.
A coordinate can be defined by clicking on the relevant field then entering the value. Alternatively, and where applicable/available, click

to the right of the field then specify the required point directly in the PCB workspace.
- Color - click to open a drop-down to set/change the color of the associated guide.
- Add - click to add a new snap guide or snap point. Choose the corresponding command for the required guide type from the associated menu; an entry for the new guide/point will be added to the grid. The following guide types are available:
- Add Horizontal Guide - use this command to add a horizontal guideline at the desired Y-coordinate location in the workspace.
- Add Vertical Guide - use this command to add a vertical guideline at the desired X-coordinate location in the workspace.
- Add +45 Guide - use this command to add a 45 degree (
y=x
) guideline that passes through the desired X,Y coordinate location in the workspace.
- Add -45 Guide - use this command to add a -45 degree (
y=-x
) guideline that passes through the desired X,Y coordinate location in the workspace.
- Add Snap Point - use this command to add a point snap guide. This is a hotspot that you manually mark within the confines of the default snap grid. During an interactive process such as placing or moving an object, that objects' hotspot will 'snap' to a point snap guide when it passes into close proximity with it.
- Place - click to place a guide. Select the guide type from the drop-down:
- Place Horizontal Guide - use this command to place a horizontal guideline at the desired Y-coordinate location in the workspace.
- Place Vertical Guide - use this command to place a vertical guideline at the desired X-coordinate location in the workspace.
- Place +45 Guide - use this command to place a 45 degree (
y=x
) guideline that passes through the desired X,Y coordinate location in the workspace.
- Place -45 Guide - use this command to place a -45 degree (
y=-x
) guideline that passes through the desired X,Y coordinate location in the workspace.
- Place Snap Point - use this command to place a point snap guide. This is a hotspot that you manually mark within the confines of the default snap grid. During an interactive process such as placing or moving an object, that objects' hotspot will 'snap' to a point snap guide when it passes into close proximity with it.
-
- click to delete the currently selected guide.
Other
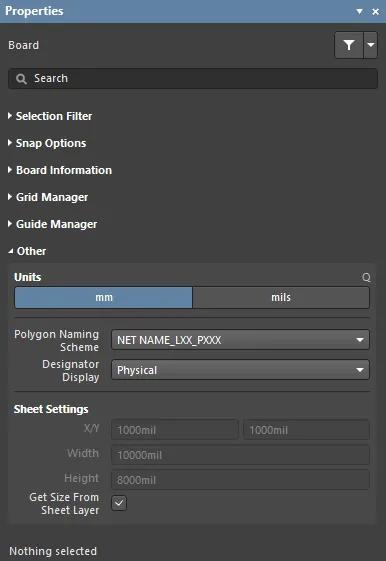
- Units - use to select the default measurement units for the current PCB document. Default units are used to display any distance related information on screen or in reports. The default units are always used if a unit's suffix (mm or mil) is not entered when specifying any distance related information.
- Polygon Naming Scheme - select a naming system from the dropdown menu. There are four choices of naming templates:
NET NAME_LXX_PXXX
LXX_NET NAME_PXXX
NET NAME_LAYER NAME_PXXX
LAYER NAME_NET NAME_PXXX
where:
NET NAME
- name of the net to which the polygon is connected. If the polygon is not connected to a net, the name NONET
is used.
LAYER NAME
- user-defined name of that layer from the Layer Stack.
LXX
- system assigned copper layer number based on the current order of layers in the Layer Stack where Top Layer is L01
. This value is updated whenever the order of copper layers is changed.
PXXX
- system-assigned numerical index; unique for each polygon on the board.
Design changes, such as moving a layer in the layer stack, renaming a net,l or changing the naming scheme will result in the automatic name changing. Affected design rules are automatically updated.
- Designator Display - use this field to determine how designators are to be displayed. It can be difficult positioning the designator strings in a multi-channel design, as they can end up being quite long. As well as choosing a naming option that results in a short name, another option is to display just the original, logical component designation instead. For example, C30_CIN1 would display as C30. This would of course necessitate some other notation being added to the board to indicate the separate channels, such as a box being drawn around each channel on the component overlay. The following options are available:
- Physical - choose to display the physical designators. These are the designators displayed on the compiled tab views of the schematic source documents. For multi-channel designs, designator format is determined by the Designator Format field on the Multi-Channel tab of the Project Options dialog. Physical designators are unique, e.g., R1_CH1.
- Logical - choose to display the logical designators. These are the designators displayed on the Editor tab views of the schematic source documents. Logical designators are not unique; for example, the R1_CH1 physical designator will become simply R1.
- Sheet Settings - use this region to configure the PCB sheet.
- X/Y - enter the X and Y coordinates for the bottom left corner of the sheet. This distance is measured from the absolute origin, which is the bottom left corner of the workspace. The distance can be defined in either metric or imperial units regardless of the default units (which are determined by the Units setting). To specify the units when entering a size, add the mm or mil suffix to the value.
- Width - enter a width for the sheet here. The sheet provides an area that emulates the traditional drawing sheet and is useful for placing information such as dimensions, notes and title blocks. Information placed on mechanical layers can be linked to the sheet so that they only display when the sheet is being displayed. Sheet size can be defined in either metric or imperial units regardless of the default units (which are determined by the Units setting). To specify the units when entering a size, add the mm or mil suffix to the value.
- Height - eEnter a height for the sheet here. The sheet provides an area that emulates the traditional drawing sheet and is useful for placing information such as dimensions, notes and title blocks. Information placed on mechanical layers can be linked to the sheet so that they only display when the sheet is being displayed. Sheet size can be defined in either metric or imperial units regardless of the default units (which are determined by the Units setting). To specify the units when entering a size, add the mm or mil suffix to the value.
- Get Size From Sheet Layer - enable this option to size the sheet from the sheet layer.
When a design object is selected, the panel will present options specific to that object type. The following table lists the object types available for placement within a PCB document - click a link to access the properties page for that object.
Although
Tracks and
Lines are actually the same object, the difference is how the software behaves during their placement, which is why there are different commands.
After launching the Place » Line command, the cursor will change to a cross-hair and the editor will enter line placement mode. Placement is made by performing the following actions:
- Click to define the starting position of the line.
- Move the cursor to set the length and angle the line then click again to complete placement.
- Continue placing further lines, or right-click or press Esc to exit the placement mode.
Database Component Library Synchronization
When signed in to your Altium 365 Workspace, select File » New » Components Synchronization Configuration in Altium Designer to create a synchronization document.
Component Type Table
The image above shows three states of parameter mapping in the Properties panel. On the left is when no Component Template is applied, the center image is the result when a template has been specified, and the image on the right demonstrates modified parameter mapping and Revision control.
- General
- Component Type - lists the identified component type.
- Component Template - lists the identified component template, which determines the target server folder, component Naming Scheme and applied Lifecycle definition.
- Key Parameter - lists the key parameter matched to the source database entry using a unique identifier.
- Advanced
- Folder - the target server folder in which the component resides.
- Revision Naming Scheme - the naming arrangement used for the object's server revisions, as set by the applied template or selected from the entry's drop-down menu options. Only those schemes enabled by the system will be available as an option.
- Lifecycle Definition - the Lifecycle system that is used for the object, as set by the applied template or selected from the entry's drop-down menu options. Only those definitions enabled by the system will be available as an option.
- Parameter Mapping - offers a grid listing of the relationship between target server parameters and source database parameters (fields). Also available are settings for the transferred parameter Type (text or unit-aware) and control of new Revision creation for updated parameters. In terms of parameter mapping, the table columns represent the workspace target (Parameter) and the source/master database fields (Column).
- Add - use to add an additional parameter.
-
- use to delete specified parameter.
- Reset to Default - used to revert all changes made.
Table Inclusion
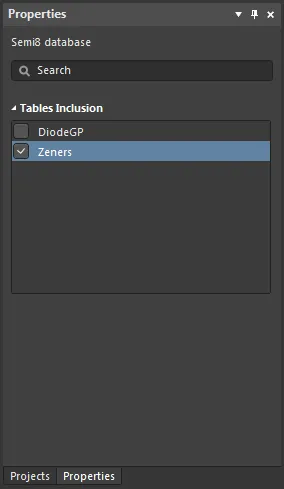
- Table Inclusion - lists inclusion of database tables that you may check to be synchronized in the Properties panel, which is then accessed as a parametric data source that populates the Components Preview listing in the Component Synchronization Configuration menu.
For more information on Component Synchronization Configuration, see the Component Database to Server Data Synchronization page.
PCB Library Support
When the active document is a PCB Library document (*.PcbLib) and when no design object is currently selected in the design space, the Properties panel presents the Library Options. The following collapsible sections contain information about the options and controls available.
Selection Filter
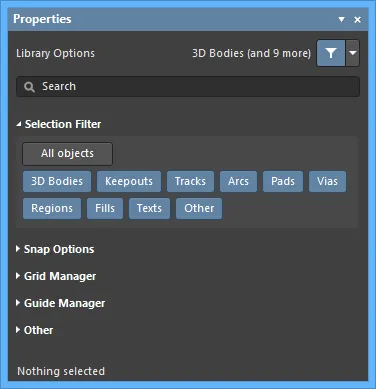
The options in this section of the panel determine which PCB library objects may be selected in the workspace.
- All Objects button – select remove object filtering so that all types of objects may be selected.
- Object buttons – toggle each object button to enable/disable the ability to select that object type.
Snap Options
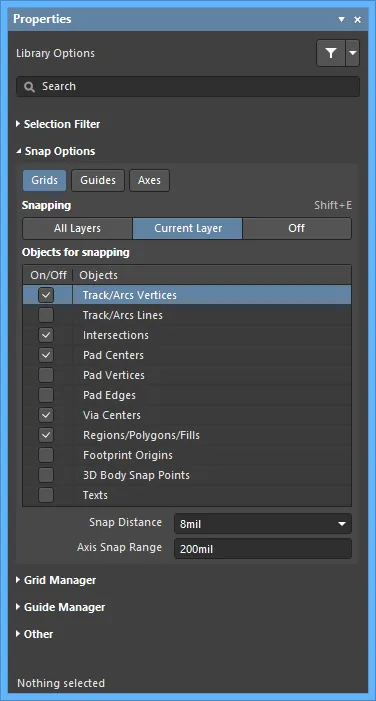
- Grids - used to toggle whether the cursor will snap to the active workspace grid. When this option is enabled the cursor will pull, or snap, to the nearest snap grid location. The active snap grid is displayed on the Status bar, and in the PCB editor Heads Up display (Shift+H shortcut to toggle on/off).
- Guides - used to toggle whether the cursor will snap to manually placed linear or point Snap Guides. A Snap Guide will override the Snap Grid.
- Axes - used to toggle whether the cursor will axially-align (in either the X or Y direction) to the enabled Objects for snapping. The Axis Snap Range defines the distance within which X or Y axial-alignment will occur. A dynamic alignment guide line is displayed when alignment is achieved from the current cursor location to the axially-aligned object snap point (hotspot).
- Snapping - select directly or use the Shift+E shortcut to select whether you want to snap to objects on:
- All Layers - enable this option to allow the cursor to snap to any electrical object on any visible layer.
- Curent Layer - enable this option to allow the cursor to only recognize and snap to objects placed on the currently selected layer.
- Off - enable this option to turn off snapping to hotspots.
- Objects for snapping
- On/Off - check to enable snapping for the desired objects.
- Objects - a list of the available objects.
- Snap Distance - when the cursor is within this distance from an enabled object snap point (and snapping is enabled for the active layer), the cursor will snap to that point.
- Axis Snap Range - when the cursor is axially-aligned and within this distance from an enabled object snap point (and the Axes button is enabled), a dynamic guide line will display to indicate that alignment has been achieved.
Grid Manager
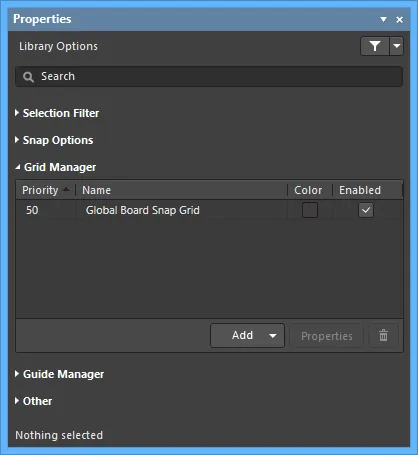
- Grid Manager - where local customized grids can be defined and managed, as well as the default Snap Grid for the board.
- Priority - in the workspace, priority is distinguished by drawing order. The highest priority grid (priority
1
) will be drawn in front of all other grids, then the grid with priority level 2
, etc., down to the default Global Board Snap Grid
, which is drawn behind all other custom grids.
- Name - displays the name of the grid.
- Color - click to open a drop-down to set/change the color of the associated grid.
- Enabled - check to enable the associated grid.
- Add
- Add Cartesian Grid - click to add a Cartesian grid.
- Add Polar Grid - click to add a Polar grid. Polar grids enable you to more easily design non-rectangular features and boards.
- Properties - click to open the respective grid editor dialog (Cartesian Grid Editor or Polar Grid Editor) to modify properties for the selected grid.
-
- click to delete the currently selected grid.
Guide Manager
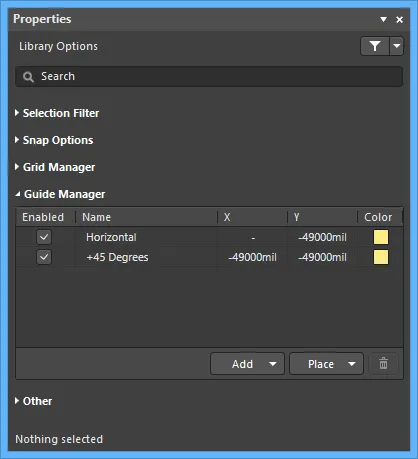
- Guide Manager - where a range of manual Snap Guides and Snap Points for the board can be defined and managed.
- Enabled - whether the guide is visible in the workspace (checked) or not (unchecked).
- Name - the name of the guide.
- X - the x-coordinate (where applicable) specified in the workspace that the guide is to pass through or point is to be located at.
- Y - the y-coordinate (where applicable) specified in the workspace that the guide is to pass through or point is to be located at.
A coordinate can be defined by clicking on the relevant field then entering the value. Alternatively, and where applicable/available, click

to the right of the field, then specify the required point directly in the PCB Library workspace.
- Color - click to open a drop-down to set/change the color of the associated guide.
- Add - click to add a new snap guide or snap point. Choose the corresponding command for the required guide type from the associated menu; an entry for the new guide/point will be added to the grid. The following guide types are available:
- Add Horizontal Guide - use this command to add a horizontal guideline at the desired Y-coordinate location in the workspace.
- Add Vertical Guide - use this command to add a vertical guideline at the desired X-coordinate location in the workspace.
- Add +45 Guide - use this command to add a 45 degree (
y=x
) guideline that passes through the desired X,Y coordinate location in the workspace.
- Add -45 Guide - use this command to add a -45 degree (
y=-x
) guideline that passes through the desired X,Y coordinate location in the workspace.
- Add Snap Point - use this command to add a point snap guide. This is a hotspot that you manually mark within the confines of the default snap grid. During an interactive process such as placing or moving an object, that objects' hotspot will 'snap' to a point snap guide when it passes into close proximity with it.
- Place - click to place a guide. Select the guide type from the drop-down:
- Place Horizontal Guide - use this command to place a horizontal guideline at the desired Y-coordinate location in the workspace.
- Place Vertical Guide - use this command to place a vertical guideline at the desired X-coordinate location in the workspace.
- Place +45 Guide - use this command to place a 45 degree (
y=x
) guideline that passes through the desired X,Y coordinate location in the workspace.
- Place -45 Guide - use this command to place a -45 degree (
y=-x
) guideline that passes through the desired X,Y coordinate location in the workspace.
- Place Snap Point - use this command to place a point snap guide. This is a hotspot that you manually mark within the confines of the default snap grid. During an interactive process such as placing or moving an object, that objects' hotspot will 'snap' to a point snap guide when it passes into close proximity with it.
-
- click to delete the currently selected guide.
Other
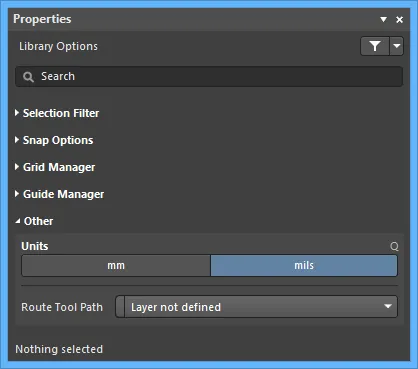
- Units - use to select the default measurement units for the current PCB Library document. Default units are used to display any distance related information on screen or in reports. The default units are always used if a unit's suffix (mm or mil) is not entered when specifying any distance related information.
- Route Tool Path - use the drop-down to choose the mechanical layer (from all those currently enabled for use in the design) on which to define the route tool path for the board.
When a design object is selected, the panel will present options specific to that object type. The following table lists the object types available for placement within the library workspace - click a link to access the properties page for that object.
Interactive Routing Support
When the active document is a PCB document (*.PcbDoc) and you are currently using the interactive routing tool, the Properties panel presents options pertinent to that tool. The following collapsible sections contain information about the options and controls available:
Net Information
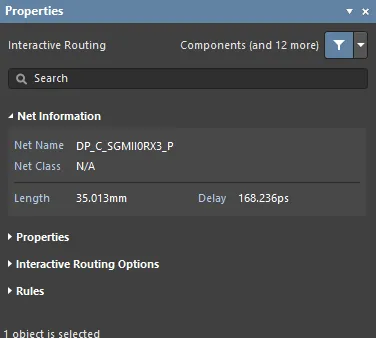
- Net Name - displays the name of the net to which the interactive routing is connected.
- Net Class - displays the net class that the interactive routing belongs to (if it is a member of a net class).
- Length - the total Signal Length. The Signal Length is the accurate calculation of the total node-to-node distance. Placed objects are analyzed to: resolve stacked or overlapping objects and wandering paths within pads; and via lengths are included.
- Delay - the total delay of the selected segments, including those unrouted.
Select the clickable links of the
Net Name,
Net Class,
Length,
and
Delay from the
Interactive Routing mode of the
Properties panel to be redirected to the
PCB - Nets panel, where you may view and change details of the nets associated.
Properties
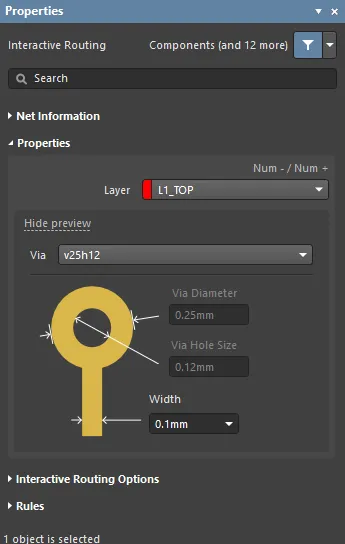
- Layer - use the drop-down to specify on which layer the routing is located.
- Via - if the via is associated with a template, the template name is displayed here.
- Via Diameter - specify the via diameter.
- Via Hole Size - specify the via hole size.
- Width - use the drop-down to specify the width.
- Min - signifies that the design rule minimum width defined for the current net will be used
- Preferred - signifies that the design rule preferred width defined for the current net will be used.
- Max - signifies that the design rule maximum width defined for the current net will be used.
Interactive Routing Options
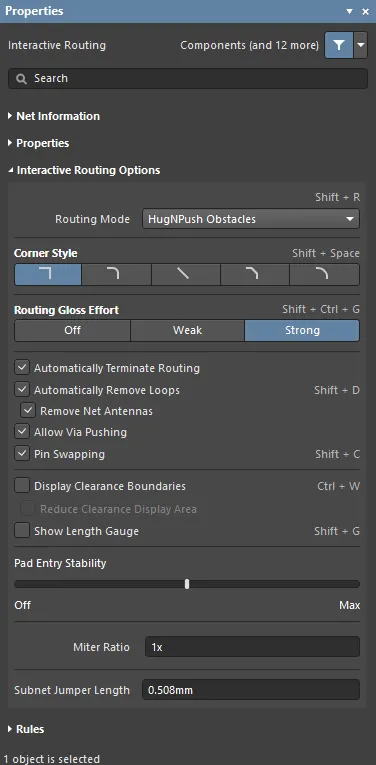
- Routing Mode - use the drop-down or use the Shift+R shortcut to cycle through the desired routing modes. The following choices are available:
- Ignore Obstacles - select to ignore existing objects (routing can be freely placed). Violations are highlighted.
- Walkaround Obstacles - select to have the Interactive Router route around existing tracks, pads and vias. If this mode cannot walk around an obstacle without causing a violation, an indicator appears to show that the route is blocked.
- Push Obstacles - select to have the Interactive Router move existing tracks out of the way. This mode can also push vias to make way for the new routing. If this mode cannot push an obstacle without causing a violation, an indicator appears to show that the route is blocked.
- HugNPush Obstacles - select to have the Interactive Router hug existing tracks, pads, and vias as closely as possible and where necessary, push obstacles to continue the route. If this mode cannot hug or push an obstacle without causing a violation, an indicator appears to show that the route is blocked.
- Stop At First Obstacle - in this mode, the routing engine will stop at the first obstacle that gets in the way.
- AutoRoute Current Layer - select to enable auto-routing only on the current layer.
- AutoRoute MultiLayer - select to enable auto-routing on multiple layers.
- Corner Style - select the desired routing corner style or use the Shift+Spacebar shortcut to cycle through the corner styles.
- Routing Gloss Effort - select the desired gloss level directly from the panel or use the Shift+Ctrl+G shortcut to cycle through the following choices:
- Off - in this mode, glossing is essentially disabled. Note, however, that cleanup is still run after routing/dragging occurs to eliminate, for example, overlapping track segments. This mode is typically useful at the end stage of board layout when the ultimate level of fine-tuning is required (for example, when manually dragging tracks, cleaning pad entries, etc.).
- Weak - in this mode, a low level of glossing is applied with the Interactive Router considering only those tracks directly connected to or in the area of the tracks that you are currently routing (or tracks/vias being dragged). This mode of glossing is typically useful for fine-tuning track layout or when dealing with critical traces.
- Strong - in this mode, a high level of glossing is applied with the Interactive Router looking for shortest paths, smoothing out tracks, etc. This mode of glossing is typically useful in the early stages of the layout process when the aim is to get a good amount of the board routed quickly.
- Automatically Terminate Routing - when enabled, when you complete a route to the target pad, the routing tool does not continue in routing mode from the target pad but rather resets and is ready for you to click on the next source pad from which to route. If this option is disabled, after you route to the target pad, the tool will remain in routing mode and use the previous target pad as the source for the next route.
- Automatically Remove Loops - enable to automatically remove any redundant loops that are created during manual routing. This allows you to re-route a connection without having to manually remove redundant tracks. However, there are times when you need to route nets such as power nets and you need loops. You can toggle this option for a selected net by using the Shift+D shortcut to override this global setting for the same net.
- Remove Net Antennas - enable this option to remove any track or arc end that is not connected to any other primitive and forms an antenna.
- Allow Via Pushing - check this option to allow pushing a Via when in Push Obstacles or HugNPush Obstacles mode.
- Pin Swapping - check this option to enable pin swapping or use the Shift+C shortcut.
- Display Clearance Boundaries - enable to have the no-go clearance area defined by the existing objects and the applicable clearance rule displayed as shaded polygons within a local viewing circle or use the Ctrl+W shortcut to toggle on or off during routing. This option is not available in the Ignore Obstacles routing mode.
- Reduce Clearance Display Area - enable to use a smaller clearance boundary. This option is available only when the Display Clearance Boundaries option is enabled.
- Show Length Gauge - enable to display the length gauge, which shows the current routed length. The gauge settings are calculated from the set of constraints defined by the applicable design rules. Use the Shift+G shortcut to toggle the display on or off during routing.
- Pad Entry Stability - protects centered pad entries. Use the slider bar to configure the level of protection:
Off =
no protection
Max =
maximum protection
- Miter Ratio - controls the minimum corner tightness. The Miter Ratio multiplied by the current track width equals the separation between walls of the tightest U-shape that can be routed for that ratio. Enter a positive value equal to or greater than zero (the x multiplier is added automatically).
- Subnet Jumper Length - specify the desired Subnet Jumper length.
Jumpers, which are also referred to as wire links, allow the designer to replace routing with a Jumper component. To learn more, see
Working with Jumper Components.
Rules
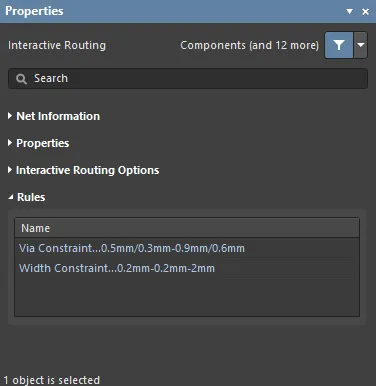
Constraints defined by the applicable design rules will be listed under the Rules section of the Properties panel.
- Via Constraint - click to open the Edit PCB Rule dialog in which you can define PCB rules for via.
- Width Constraint- click to open the Edit PCB Rule dialog in which you can define PCB rules for routing width.
Interactive Differential Pair Routing Support
When the active document is a PCB document (*.PcbDoc) and you are currently using the interactive differential pair routing tool, the Properties panel presents options pertinent to that tool. The following collapsible sections contain information about the options and controls available:
Net Information
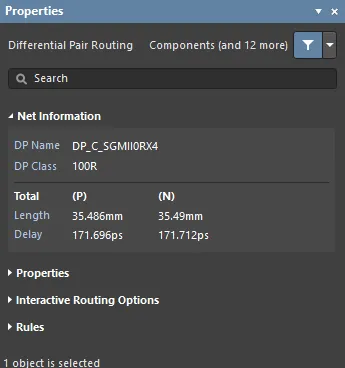
- DP Name - displays the differential pair name.
- DP Class - displays the differential pair class that the routing belongs to (if it is a member of a differential pair class).
- Selected
- Length - the total length sum of the selected segments.
- Delay - the total delay of the selected segments, including those unrouted.
- Total
- Length - the total Signal Length. The Signal Length is the accurate calculation of the total node-to-node distance. Placed objects are analyzed to: resolve stacked or overlapping objects and wandering paths within pads; and via lengths are included. If the net is not completely routed, the Manhattan (X + Y) length of the connection line is also included.
- Delay - the delay of the routed segments of the Total Length.
Select the clickable links of the
DP Name,
DP Class,
Length,
and
Delay from the
Differential Pair Routing mode of the
Properties panel to be redirected to the
PCB - Nets panel, where you may view and change details of the nets associated.
Properties
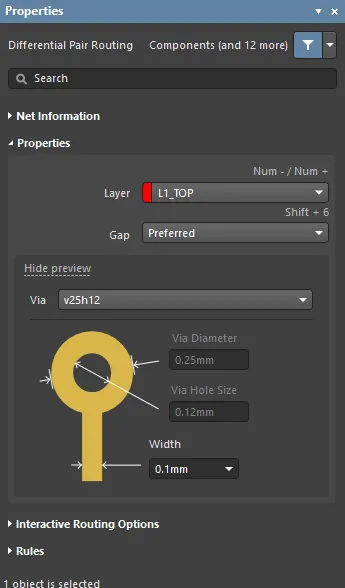
- Layer - use the drop-down to specify on which layer the routing is located.
- Gap - use the drop-down or the Shift+6 shortcut to cycle through the permissible clearances.
- Min - select to specify the minimum permissible clearance between primitives on different nets within the same differential pair.
- Preferred - select to specify the preferred clearance between primitives on different nets within the same differential pair.
- Max - select to specify the maximum permissible clearance between primitives on different nets within the same differential pair.
- Via - if the via is associated with a template, the template name is displayed here.
- Via Diameter - specify the via diameter.
- Via Hole Size - specify the via hole size.
- Width - use the drop-down to specify the width.
- Min - signifies that the design rule minimum width defined for the current net will be used
- Preferred - signifies that the design rule preferred width defined for the current net will be used.
- Max - signifies that the design rule maximum width defined for the current net will be used.
Interactive Routing Options

- Routing Mode - use the drop-down or use the Shift+R shortcut to cycle through the desired routing modes. The following choices are available:
- Ignore Obstacles - select to ignore existing objects (routing can be freely placed). Violations are highlighted.
- Walkaround Obstacles - select to have the Interactive Router route around existing tracks, pads and vias. If this mode cannot walk around an obstacle without causing a violation, an indicator appears to show that the route is blocked.
- Push Obstacles - select to have the Interactive Router move existing tracks out of the way. This mode can also push vias to make way for the new routing. If this mode cannot push an obstacle without causing a violation, an indicator appears to show that the route is blocked.
- HugNPush Obstacles - select to have the Interactive Router hug existing tracks, pads, and vias as closely as possible and where necessary, push obstacles to continue the route. If this mode cannot hug or push an obstacle without causing a violation, an indicator appears to show that the route is blocked.
- Stop At First Obstacle - in this mode, the routing engine will stop at the first obstacle that gets in the way.
- AutoRoute Current Layer - select to enable auto-routing only on the current layer.
- AutoRoute MultiLayer - select to enable auto-routing on multiple layers.
- Corner Style - select the desired routing corner style or use the Shift+Spacebar shortcut to cycle through the corner styles.
- Restrict to 90/45 - enable to restrict the routing to 90 degrees and 45 degrees only.
- Routing Gloss Effort - select the desired gloss level from the panel or use the Shift+Ctrl+G shortcut to cycle through the following choices:
- Off - in this mode, glossing is essentially disabled. Note, however, that cleanup is still run after routing/dragging occurs to eliminate, for example, overlapping track segments. This mode is typically useful at the end stage of board layout when the ultimate level of fine-tuning is required (for example, when manually dragging tracks, cleaning pad entries, etc.).
- Weak - in this mode, a low level of glossing is applied with the Interactive Router considering only those tracks directly connected to or in the area of the tracks that you are currently routing (or tracks/vias being dragged). This mode of glossing is typically useful for fine-tuning track layout or when dealing with critical traces.
- Strong - in this mode, a high level of glossing is applied with the Interactive Router looking for shortest paths, smoothing out tracks, etc. This mode of glossing is typically useful in the early stages of the layout process when the aim is to get a good amount of the board routed quickly.
- Automatically Terminate Routing - when enabled, when you complete a route to the target pad, the routing tool does not continue in routing mode from the target pad but rather resets and is ready for you to click on the next source pad from which to route. If this option is disabled, after you route to the target pad, the tool will remain in routing mode and use the previous target pad as the source for the next route.
- Automatically Remove Loops - enable to automatically remove any redundant loops that are created during manual routing. This allows you to re-route a connection without having to manually remove redundant tracks. However, there are times when you need to route nets, such as power nets and when you need loops; you can toggle this option for a selected net by using the Shift+D shortcut to override this global setting for the same net.
- Remove Net Antennas - enable this option to remove any track or arc end that is not connected to any other primitive and forms an antenna.
- Allow Via Pushing - check this option to allow pushing a Via when in Push Obstacles or HugNPush Obstacles mode.
- Pin Swapping - check this option to enable pin swapping or use the Shift+C shortcut.
- Display Clearance Boundaries - enable this option to have the no-go clearance area defined by the existing objects and the applicable clearance rule displayed as shaded polygons within a local viewing circle. This option is not available in the Ignore Obstacles routing mode.
- Reduce Clearance Display Area - enable this option to use a smaller clearance boundary. This option is available only when the Display Clearance Boundaries option is enabled.
- Miter Ratio - controls the minimum corner tightness. The Miter Ratio multiplied by the current track width equals the separation between walls of the tightest U-shape that can be routed for that ratio. Enter a positive value equal to or greater than zero (the x multiplier is added automatically).
- Subnet Jumper Length - specify the desired Subnet Jumper length.
Jumpers, which are also referred to as wire links, allow the designer to replace routing with a Jumper component. To learn more, see
Working with Jumper Components.
Rules
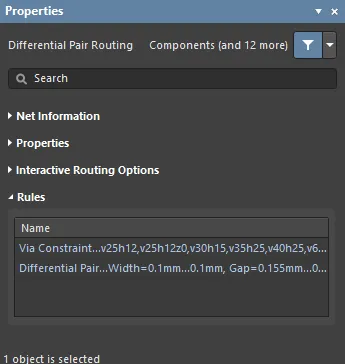
Constraints defined by the applicable design rules will be listed under the Rules section of the Properties panel.
- Via Constraint - click to open the Edit PCB Rule dialog in which you can define PCB rules for via.
- Differential Pair Constraint - click to open the Edit PCB Rule dialog in which you can define PCB rules for the differential pair.
Interactive Sliding Support
When the active document is a PCB document (*.PcbDoc) and you are currently using the interactive sliding tool, the Properties panel presents options pertinent to that tool. The following collapsible sections contain information about the options and controls available:
Net Information
Interactive Sliding mode - press Tab during sliding to access the options in the panel.
- Net Name - displays the name of the net to which the interactive sliding is connected.
- Net Class - displays the net class that the interactive sliding belongs to (if it is a member of a net class).
- Length - the total Signal Length. The Signal Length is the accurate calculation of the total node-to-node distance. Placed objects are analyzed to: resolve stacked or overlapping objects and wandering paths within pads; and via lengths are included.
- Delay - the total delay of the selected segments, including those unrouted.
Select the clickable links of the
Net Name,
Net Class,
Length,
and
Delay from the
Interactive Routing mode of the
Properties panel to be redirected to the
PCB - Nets panel, where you may view and change details of the nets associated
Properties
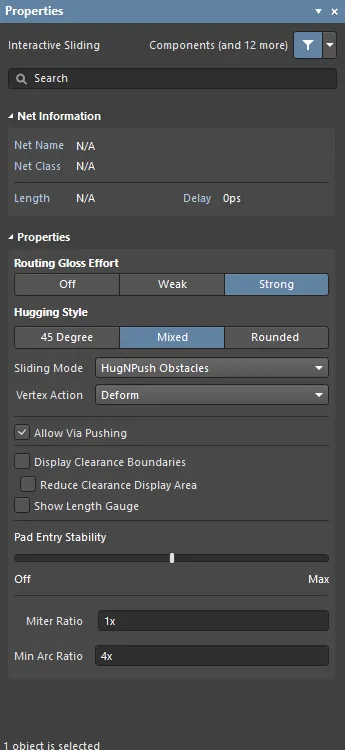
- Routing Gloss Effort - select the desired gloss level from the panel or use the Shift+Ctrl+G shortcut to cycle through the following choices:
- Off - in this mode, glossing is essentially disabled. Note, however, that cleanup is still run after routing/dragging occurs to eliminate, for example, overlapping track segments. This mode is typically useful at the end stage of board layout when the ultimate level of fine-tuning is required (for example, when manually dragging tracks, cleaning pad entries, etc.).
- Weak - in this mode, a low level of glossing is applied with the Interactive Router considering only those tracks directly connected to or in the area of the tracks that you are currently routing (or tracks/vias being dragged). This mode of glossing is typically useful for fine-tuning track layout or when dealing with critical traces.
- Strong - in this mode, a high level of glossing is applied with the Interactive Router looking for shortest paths, smoothing out tracks, etc. This mode of glossing is typically useful in the early stages of the layout process when the aim is to get a good amount of the board routed quickly.
- Hugging Style - controls how corner shapes are to be managed during interactive sliding and will affect both the tracks being slid and the tracks being pushed. During sliding use the Shift+Spacebar shortcut to cycle through the three modes.
- 45 Degree - always use straight orthogonal/diagonal segments to create corners during sliding (use this mode for traditional orthogonal/diagonal routing behavior).
- Mixed - use straight track segments when the objects being moved/pushed against are straight, use arcs when they are curved.
- Rounded - use arcs at each vertex involved in the move/push. Use this mode for snake routing, and to use arcs + any angle routes when glossing (during interactive routing and manual glossing).
- Sliding Mode - determines how you want the sliding objects to react when they encounter an existing object. Use the drop-down or use the Shift+R shortcut to cycle through the desired routing modes. The following choices are available:
- Ignore Obstacles - select to ignore existing objects (routing can be freely placed). Violations are highlighted.
- Walkaround Obstacles - select to have the Interactive Router route around existing tracks, pads and vias. If this mode cannot walk around an obstacle without causing a violation, an indicator appears to show that the route is blocked.
- Push Obstacles - select to have the Interactive Router move existing tracks out of the way. This mode can also push vias to make way for the new routing. If this mode cannot push an obstacle without causing a violation, an indicator appears to show that the route is blocked.
- HugNPush Obstacles - select to have the Interactive Router hug existing tracks, pads, and vias as closely as possible and where necessary, push obstacles to continue the route. If this mode cannot hug or push an obstacle without causing a violation, an indicator appears to show that the route is blocked.
- Stop At First Obstacle - in this mode, the routing engine will stop at the first obstacle that gets in the way.
- AutoRoute Current Layer - select to enable auto-routing only on the current layer.
- AutoRoute MultiLayer - select to enable auto-routing on multiple layers.
- Vertex Action - options that are applied when you click and drag on a vertex rather than a track or arc (the vertex is the corner location where two segments meet). Use the Spacebar shortcut to cycle through the available modes during sliding.
- Deform - break or lengthen the track segments attached to the moving vertex so that the vertex follows the cursor movement. (show animation)
- Scale - hold the corner shape and resize and move the incoming track segments, keeping the vertex attached to the cursor. (show animation)
- Smooth - reshape the corner smoothly, inserting arcs to create a curved corner when dragging inward (in Mixed or Rounded Hugging Style), at every vertex impacted by the sliding process. Also add arcs when dragging outward in Rounded Hugging Style.
- Allow Via Pushing - check this option to allow pushing a Via when in Push Obstacles or HugNPush Obstacles mode.
- Display Clearance Boundaries - enable to have the no-go clearance area defined by the existing objects and the applicable clearance rule displayed as shaded polygons within a local viewing circle. This option is not available in the Ignore Obstacles routing mode.
- Reduce Clearance Display Area - enable to use a smaller clearance boundary. This option is available only when the Display Clearance Boundaries option is enabled.
- Show Length Gauge - enable to display the length gauge, which shows the current routed length. The gauge settings are calculated from the set of constraints defined by the applicable design rules. Use the Shift+G shortcut to toggle the display on or off during routing.
- Pad Entry Stability - protects centered pad entries. Use the slider bar to configure the level of protection:
Off =
no protection
Max =
maximum protection
- Miter Ratio - controls the minimum corner tightness. The Miter Ratio multiplied by the current track width equals the separation between walls of the tightest U-shape that can be routed for that ratio. Enter a positive value equal to or greater than zero (the x multiplier is added automatically).
- Min Arc Ratio - applied during any angle interactive routing and during interactive sliding with Mixed Hugging Style. The ratio is used to determine the minimum radius arc allowed, when the arc radius falls below this minimum the arc is replaced by track segments, where: Min Arc Radius = Min Arc Ratio x Arc Width.
Set the Minimum Arc Ratio to 0 (zero) to always use arcs.
Interactive Multi-Routing Support
When the active document is a PCB document (*.PcbDoc) and you are currently using the interactive multi-routing tool, the Properties panel presents options pertinent to that tool. The following collapsible sections contain information about the options and controls available:
Properties
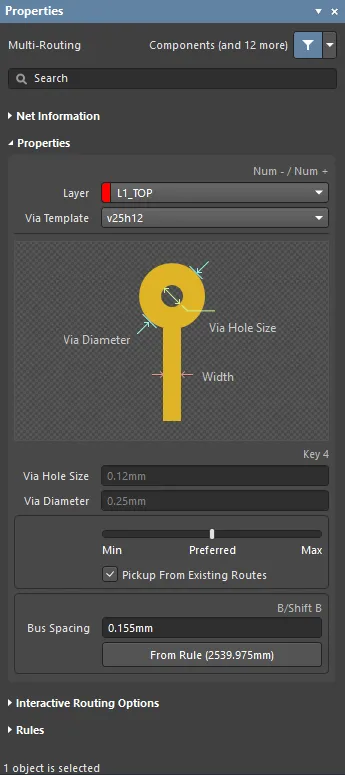
- Layer - use the drop-down to specify on which layer the routing is located.
- Via Template - if the via is associated with a template, the template name is displayed here.
- Via Hole Size - specify the via hole size or use the 4 shortcut key during routing.
- Via Diameter - specify the via hole diameter.
- Width - Use the slider bar to specify the width. Farther to the left (Min) signifies that the design rule minimum width defined for the current net will be used. Preferred signifies that the design rule preferred width defined for the current net will be used. Farther to the right (Max) signifies that the design rule maximum width defined for the current net will be used.
- Pickup From Existing Routes - enable to use the existing track width when routing from a placed track. That is, even if the current routing width is different to the existing track, the existing track width will be adopted when you continue the route from it.
- Bus Spacing - enter the desired bus routing or use the Shift+B shortcut.
- From Rule - click to assign bus spacing based on the existing design rule.
Interactive Routing Options
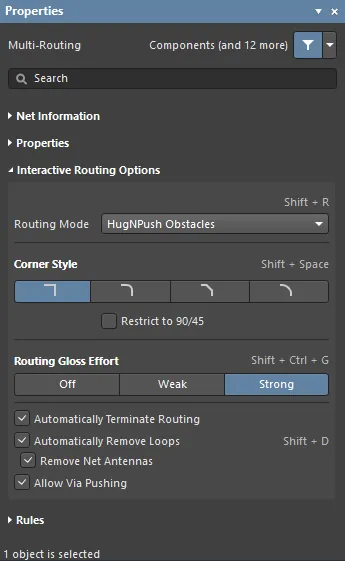
- Routing Mode - use the drop-down or use the Shift+R shortcut to cycle through the desired routing modes. The following choices are available:
- Ignore Obstacles - select to ignore existing objects (routing can be freely placed). Violations are highlighted.
- Walkaround Obstacles - select to have the Interactive Router route around existing tracks, pads and vias. If this mode cannot walk around an obstacle without causing a violation, an indicator appears to show that the route is blocked.
- Push Obstacles - select to have the Interactive Router move existing tracks out of the way. This mode can also push vias to make way for the new routing. If this mode cannot push an obstacle without causing a violation, an indicator appears to show that the route is blocked.
- HugNPush Obstacles - select to have the Interactive Router hug existing tracks, pads, and vias as closely as possible and, where necessary, push obstacles to continue the route. If this mode cannot hug or push an obstacle without causing a violation, an indicator appears to show that the route is blocked.
- Stop At First Obstacle - in this mode, the routing engine will stop at the first obstacle that gets in the way.
- AutoRoute Current Layer - select to enable auto-routing only on the current layer.
- AutoRoute MultiLayer - select to enable auto-routing on multiple layers.
- Corner Style - select the desired routing corner style or use the Shift+Spacebar shortcut to cycle through the corner styles.
- Restrict to 90/45 - enable to restrict the routing to 90 degrees and 45 degrees only.
- Routing Gloss Effort - select the desired gloss level directly from the panel or use the Shift+Ctrl+G shortcut to cycle through the following choices:
- Off - in this mode, glossing is essentially disabled. Note, however, that cleanup is still run after routing/dragging occurs to eliminate, for example, overlapping track segments. This mode is typically useful at the end stage of board layout when the ultimate level of fine-tuning is required (for example, when manually dragging tracks, cleaning pad entries, etc.).
- Weak - in this mode, a low level of glossing is applied with the Interactive Router considering only those tracks directly connected to or in the area of the tracks that you are currently routing (or tracks/vias being dragged). This mode of glossing is typically useful for fine-tuning track layout or when dealing with critical traces.
- Strong - in this mode, a high level of glossing is applied with the Interactive Router looking for shortest paths, smoothing out tracks, etc. This mode of glossing is typically useful in the early stages of the layout process when the aim is to get a good amount of the board routed quickly.
- Automatically Terminate Routing - when enabled, when you complete a route to the target pad, the routing tool does not continue in routing mode from the target pad but rather resets and is ready for you to click on the next source pad from which to route. If this option is disabled, after you route to the target pad, the tool will remain in routing mode and use the previous target pad as the source for the next route.
- Automatically Remove Loops - enable to automatically remove any redundant loops that are created during manual routing. This allows you to re-route a connection without having to manually remove redundant tracks. However, there are times when you need to route nets such as power nets and you need loops - you can toggle this option for a selected net by using the Shift+D shortcut to override this global setting for the same net.
- Remove Net Antennas - enable this option to remove any track or arc end that is not connected to any other primitive and forms an antenna.
- Allow Via Pushing - check this option to allow pushing a Via when in Push Obstacles or HugNPush Obstacles mode.
Rules
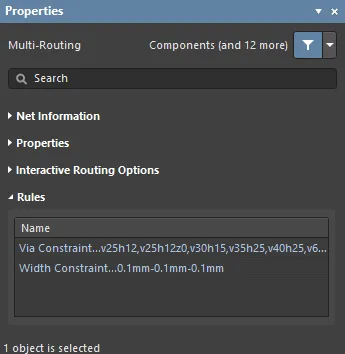
Constraints defined by the applicable design rules will be listed under the Rules section of the Properties panel.
- Via Constaint - click to open the Edit PCB Rule dialog to view/edit the rule.
- Width Constraint - click to open the Edit PCB Rule dialog to view/edit the rule.
Interactive Length Tuning Support
When the active document is a PCB document (*.PcbDoc) and you are currently using the interactive length tuning tool to place an accordion or have interactively selected an accordion object, the Properties panel presents options pertinent to that accordion.
The following collapsible sections contain information about the options and controls available:
Net Information
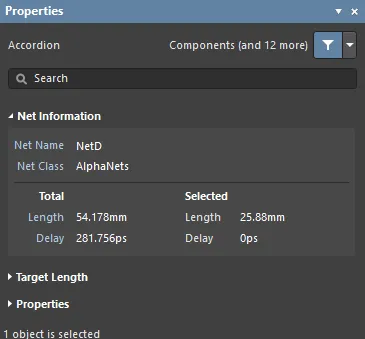
- Net Name - name of the net that the accordion is part of. Displays the * character if multiple accordions are currently selected.
- Net Class - net class that this net belongs to (if it is a member of a net class).
- Selected
- Length - the total length sum of the selected segments.
- Delay - the total delay of the selected segments, including those unrouted.
- Total
- Length - the total Signal Length. The Signal Length is the accurate calculation of the total node-to-node distance. Placed objects are analyzed to: resolve stacked or overlapping objects and wandering paths within pads; and via lengths are included. If the net is not completely routed, the Manhattan (X + Y) length of the connection line is also included.
- Delay - the delay of the routed segments of the Total Length.
The Total Length includes an estimate for the unrouted part of the net, but for the Total Delay it does not.
Select the clickable links of the
Net Name,
Net Class,
Total Length,
and
Total Delay from the
Accordion mode of the
Properties panel to be redirected to the
PCB - Nets panel, where you may view and change details of the nets associated.
Target Length
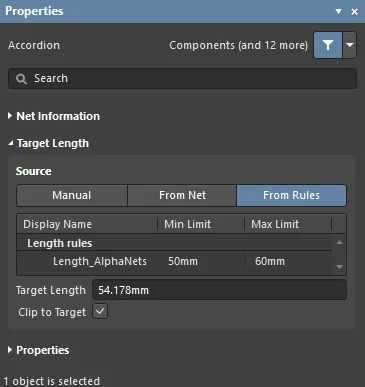
The objective of placing an accordion is to achieve a specific target length for the route whose length is being tuned. That target length is displayed in the Target Length field. The Source buttons are used to control from where that target length value is sourced, and the grid below the buttons displays details about the current choice.
- Source - source of the maximum length value that the Interactive Length Tuning command is attempting to achieve.
- Manual - required length can be entered directly into the Target Length field. A list of Recently Used Lengths will appear when this mode is selected. Click to use one of these lengths.
- From Net - required length is defined by selecting a net name. The list of net names region will include all nets in the design.
- From Rules - applicable Length and/or Matched Length design rules will be listed. If the net is targeted by multiple rules, the most conservative rule is chosen.
- Source List - this grid region changes based on the user-selected Source mode as described above.
- Target Length - overall length that the Interactive Length Tuning command is attempting to achieve with the addition of the accordion being placed.
- Clip to Target - if enabled, the accordion length is automatically clipped once the target length is achieved.
Properties

- Max Amplitude - the maximum accordion amplitude the software is permitted to create as shown by the Max Amplitude label on the image in the panel. The amplitude is automatically decreased if there are placement obstacles. The amplitude can be interactively decreased during length tuning.
- Step - the incremental step value that the Amplitude will be increased/decreased by when the shortcuts are pressed, or when it is automatically resized due to an obstacle.
- Space - the distance between the zero-crossings of the accordion shape as indicated by the Space label on the image in the panel. The Gap can be interactively decreased during length tuning.
- Step - the incremental step value that the Gap will be increased/decreased by when the shortcuts are pressed.
- Miter - percentage of the corner that is removed by the diagonal miter track/arc. The Miter can be interactively decreased during length tuning.
- Step - the incremental step value that the Miter will be increased/decreased by when the shortcuts are pressed.
- Style - select the required shape used to create the accordion from the drop-down menu.
- Mitered Lines - accordion shape is created from vertical and horizontal track segments with the corners mitered by diagonal track segments.
- Mitered Arcs - accordion shape is created from vertical and horizontal track segments with the corners mitered by a 90 degree arc segment.
- Rounded - accordion shape is created from 180 degree arc segments.
The current settings in the Properties panel become the default settings for further accordion placement.
Refer to the
object page to learn more about the Accordion object. Refer to the
Length Tuning page to learn more about interactive length tuning.
Interactive Differential Pair Length Tuning Support
When the active document is a PCB document (*.PcbDoc) and you are currently using the interactive differential pair length tuning tool, the Properties panel presents options pertinent to that tool. The following collapsible sections contain information about the options and controls available:
Differential Pair Information
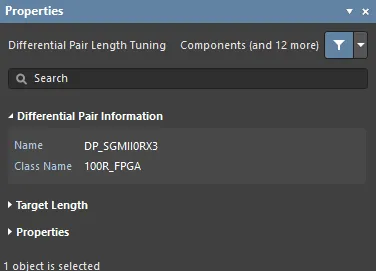
- Name - the name of the differential pair.
- Class Name - the class the pair belongs to (if available).
Select the clickable
Name and
Class Name links from
Differential Pair Information mode of the
Properties panel to be redirected to the
PCB - Nets panel, where you may view and change details of the nets associated.
Target Length
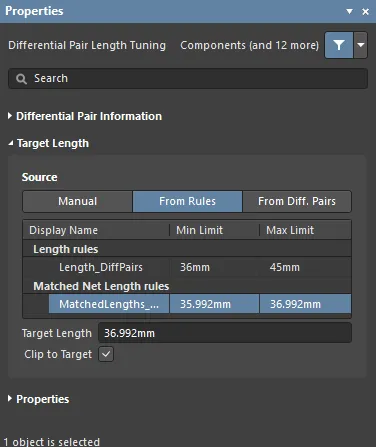
- Source
- Manual - use the manual mode to enter the length in the Target Length field. The Recently Used Lengths region keeps track of the values you have typed in so that you can easily use them again.
- From Rules - one or both of the Length and Matched Length design rules must be defined to use this mode. The software will then obey the most stringent combination of these rules. Double-click on a rule listed in the Display Name region to examine its properties in detail.
- From Diff. Pairs - lists the differential pairs and their lengths on the current PCB. The currently selected differential pair length value is shown in the Target Length field.
- Source List - this grid region changes based on the user-selected Source mode as described above.
- Target Length - overall length that the Differential Pair Length Tuning command is attempting to achieve.
- Clip to Target - enable to ensure that the final length does not exceed the target length.
Properties
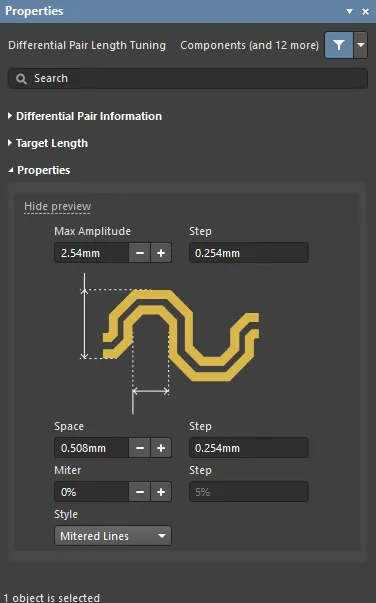
- Max Amplitude - the maximum accordion amplitude the software is permitted to create as shown by the Max Amplitude label on the image in the panel. The amplitude is automatically decreased if there are placement obstacles. The amplitude can be interactively decreased during length tuning.
- Step - the incremental step value that the Amplitude will be increased/decreased by when the shortcuts are pressed, or when it is automatically resized due to an obstacle.
- Space - the distance between the zero-crossings of the accordion shape as indicated by the Space label on the image in the panel. The Gap can be interactively decreased during length tuning.
- Step - the incremental step value that the Gap will be increased/decreased by when the shortcuts are pressed.
- Miter - percentage of the corner that is removed by the diagonal miter track/arc. The Miter can be interactively decreased during length tuning.
- Step - the incremental step value that the Miter will be increased/decreased by when the shortcuts are pressed.
- Style - select the required shape used to create the accordion from the drop-down menu.
- Mitered Lines - accordion shape is created from vertical and horizontal track segments with the corners mitered by diagonal track segments.
- Mitered Arcs - accordion shape is created from vertical and horizontal track segments with the corners mitered by a 90 degree arc segment.
- Rounded - accordion shape is created from 180 degree arc segments.
Rounded is the most compact and Mitered Lines is the least compact.
Layer Stack Support
When the active document is a Layer Stack document (*.PcbDoc [Stackup]), the Properties panel presents options pertinent to that layer stack depending on the chosen tab (located at the bottom of the Layer Stack). Tabs include Stackup, Impedance, Via Types, Back Drills, and Printed Electronics Stackup. The following collapsible sections contain information about the options and controls available for the various Layer Stack tabs:
Stackup Tab
The Stackup tab allows you to edit the layer properties of the Layer Stack.
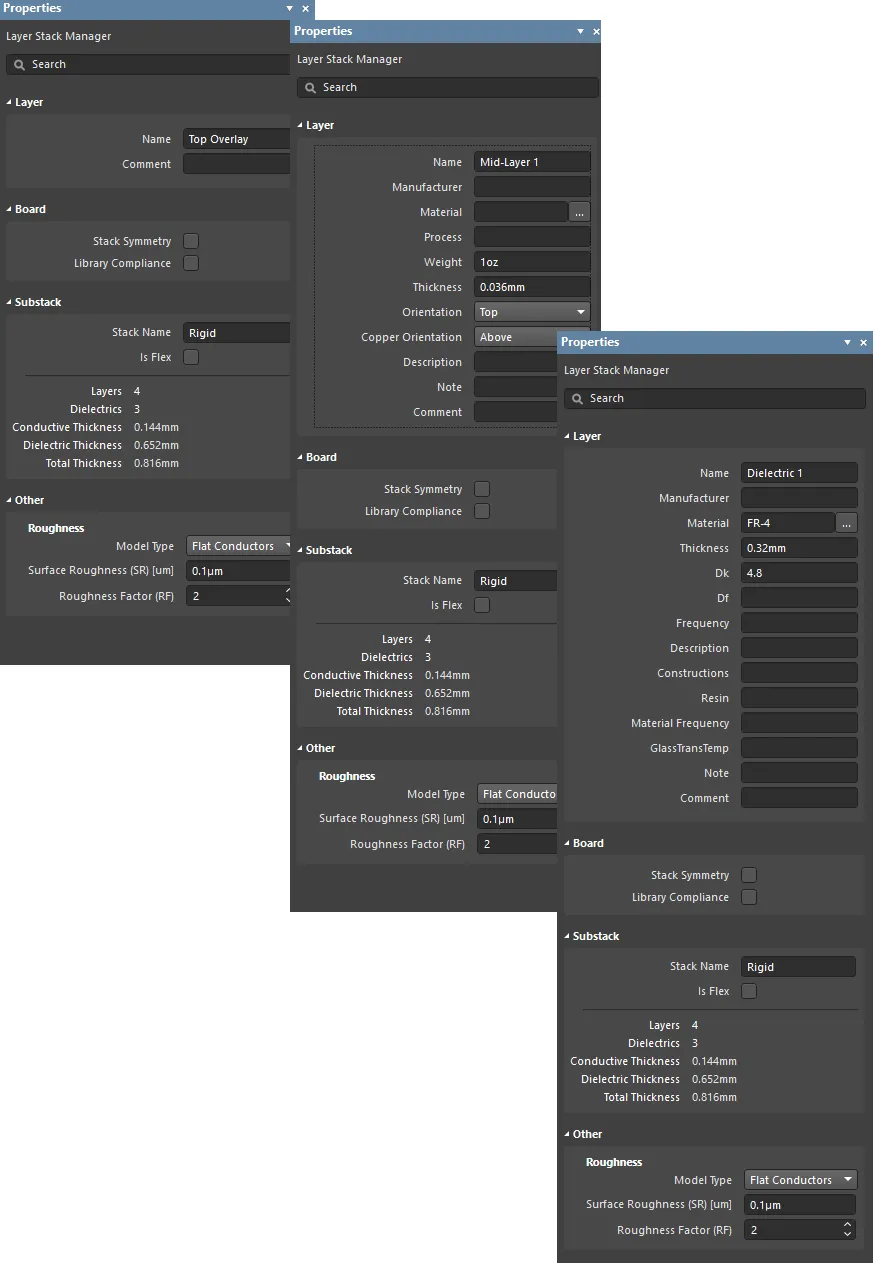
The Layer Stack Manager mode of the Properties panel: an Overlay layer (left image), an inner layer (middle image), and a dielectric layer (right image).
- Layer
- Name - the name of the layer.
- Manufacturer - the layer manufacturer.
- Material - the layer material. This can be pre-defined in the Altium Material Library dialog (Tools » Material Library) in the Constructions field, or user-defined in the Layer Stack. Click
to open the Select Material dialog to choose the desired material for the currently selected layer in the layer stack.
- Thickness - the thickness of the signal layer.
- Dk - this is the Dielectric Constant (also referred to as εr in electromagnetics). This indicates the relative permittivity of an insulator material, which refers to its ability to store electrical energy in an electric field. For insulating purposes, a material with lower dielectric constant is better and in RF applications, a higher dielectric constant may be desirable. In addition, the lower the relative dielectric constant, the closer the performance of the material to that of air. This property is critical to matching the impedance requirements of certain transmission lines.
- Df - this is the Dissipation Factor. This indicates the efficiency of an insulating material by showing the rate of energy loss for a certain mode of oscillation, such as mechanical, electrical, or electromechanical oscillation. In other words, this is the property of a material that describes how much of the energy transmitted is absorbed by the material. The greater the loss tangent, the larger the energy absorption into the material. This property directly impacts the signal attenuation at high speeds.
- Process - displays the copper plating process that is applied to the base copper that makes up the outer signal layers of the PCB (the Top Layer and Bottom Layer).
- Weight - the weight of the copper per unit area, usually expressed in ounces/square foot (e.g., 0.5 oz/ft2).
- Orientation - this defines which way the components point (orient) on that layer. For the top and bottom sides, this is set automatically in a new board. For other signal layers, it is used for:
- Rigid flex designs, where components mount on an inner signal layer that becomes a surface layer on a flex section, the software needs to know which way those components point. Use the drop-down to select the required orientation. Choices include: Not allowed, Top, and Bottom.
- For a design that includes embedded components, the software needs to know which way a component points. Refer to the Embedded Components page for information regarding setting the component orientation in the layer stack. Use the drop-down to select the required orientation. Choices include: Not allowed, Top, and Bottom.
- Copper Orientation - this defines the direction that the copper is laminated onto the core. Use the drop-down to select Above or Below, which determines the direction from which it is etched.
The
Copper Orientation can also be chosen using the drop-down in the
Copper Orientation column of the
Layer Stack. To enable the column, right-click in the header, choose
Select columns then enable the
Copper Orientation entry in the
Select columns dialog. Also, the
Trace Inverted option in the
Impedance Profile mode of the panel can be used to configure the copper orientation.
The orientation can be configured using the Copper Orientation dropdown in the Stackup mode of the Prop panel, in the Copper Orientation column (if it is currently displayed), or by the Trace Inverted checkbox in the Impedance Profile mode of the Prop panel.
- Frequency - this is the frequency at which the material is tested and the value that Dk / Df correspond to a certain frequency. Frequency is also taken from material references.
- Description - enter a meaningful description.
- Constructions - for dielectric layers, this displays the constructions of the layer. The numerical reference relates to the structure of the woven glass fabric used in the dielectric layer material; these are standard references used by PCB fabricators.
- Resin - displays the resin percentage of the layer.
Notes on Constructions and Resin:
The choice of laminate construction can significantly impact both cost and performance. As should be expected, a single-ply construction will typically represent a cost savings compared to a multiple-ply construction. The magnitude of this savings will depend on the specific glass styles involved and a host of other parameters. Performance can also be affected and should be considered when specifying the constructions to be used. First, single-ply constructions are often lower in resin content. The other main benefit of single-ply constructions is dielectric thickness control, beyond resin content considerations. Tighter thickness tolerances can be achieved using a single-ply construction.
Constructions with relatively lower resin contents are often preferred since they result in less z-axis expansion and can therefore improve reliability in many applications. In addition, lower resin contents can also improve dimensional stability, resistance to warpage, and dielectric thickness control. On the other hand, constructions with higher resin contents result in lower dielectric constant values, which are sometimes preferred for electrical performance. In addition, a certain minimum resin content is required to ensure adequate resin-to-glass wet-out and to prevent voids from occurring within the laminate. The ability to wet out the glass filaments fully with resin is also important for CAP resistance.
- Material Frequency - this is the frequency at which the material is tested and the value that Dk / Df correspond to a certain frequency. Frequency is also taken from material references.
- GlassTransTemp - this is the Glass Transition Temperature (also known as TG) and is the temperature at which the resin changes from a glass-like state to an amorphous state changing its mechanical behavior, i.e. expansion rate.
- Note - enter any pertinent notes for the layer.
- Comment - enter any necessary comments for the layer.
- Library Compliance - when enabled, for each layer that has been selected from the Material Library, the current layer properties are checked against the values of that material definition in the library.
- Substack - this information is for the currently selected substack (layers, dielectric, thicknesses, etc.,). As you switch from one substack to another, this information will update accordingly (for the currently selected substack).
The Substack region will only be available if the Rigid/Flex option is enabled in the Features drop-down.
- Stack Name - enter the substack name. Naming the substack is useful when the X/Y stackup region is being assigned a layer substack.
- Is Flex - enable if the substack is flex.
- Layers - the number of conductive layers.
- Dielectrics - the number of dielectrics.
- Conductive Thickness - this is the sum of the thicknesses of all signal and plane layers (all copper or conductive layers).
- Dielectric Thickness - the thickness of dielectric layer(s).
- Total Thickness - the total thickness of the finished board.
- Other
- Roughness - shows roughness of conductive layers.
- Model Type - preferred model for calculating the impact of surface roughness (refer to the articles below for more information on the various models). Applies to all copper layers in the stack (should it be the substack?).
- Surface Roughness - value of the surface roughness (available from your fabricator). Enter a value between 0 to 10µm, default is 0.1µm
- Roughness Factor - characterizes the expected maximal increase in conductor losses due to the roughness effect. Enter a value between 1 to 100, default is 2.
Impedance Tab
Use the Impedance tab to configure the Impedance Profile requirements. The required Impedance Profile can then be selected in the Routing Width or Differential Pairs Routing design rules.
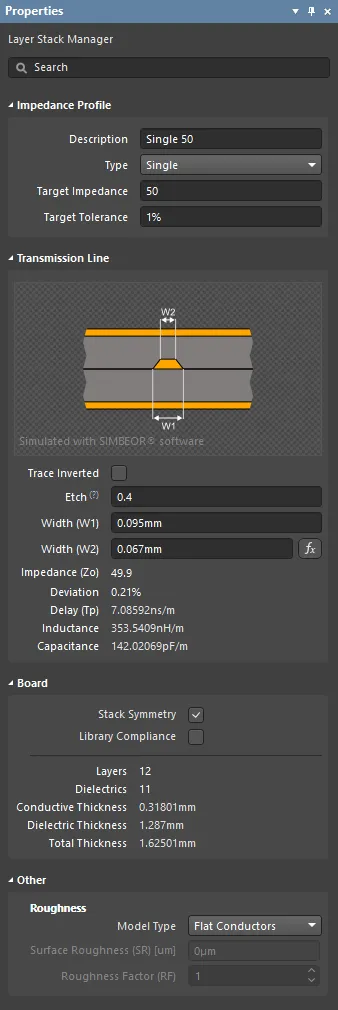
- Impedance Profile
- Description - enter a meaningful description. This field is optional and will be displayed wherever the Impedance Profile name is displayed.
- Type - use the drop-down to choose the impedance type. Choices are: Single, Differential, Single-Coplanar, and Differential-Coplanar.
When working with coplanar structured impedances and the standard single/differential impedances, values for each variable are automatically calculated based on the user-defined Target Impedance and Target Tolerance, and the physical properties of the board layers. These automatically calculated values can be adjusted by entering new values into the edit boxes of the Layer Stack Manager mode of the Properties panel.
- Target Impedance - enter the impedance you want to achieve.
- Target Tolerance - enter the tolerance you want to achieve. You should consult with the fabricator to find a realistic value for tolerance that the fabricator can deliver.
- Transmission Line
- Trace inverted - enable this option to invert the trace, as demonstrated in the Properties panel. This option is the same as the Copper Orientation option displayed when the Stackup tab is active and defines the direction that the copper is laminated onto the core. The copper orientation defines the direction the copper projects away from that substrate. You can also think of it as the direction the copper is etched from, either above or below.
- Etch - the Etch Factor is
= T/[(W1-W2)/2]
, which reduces the total cross-section area of the trace by the thickness of the copper squared. Consult the board fabricator for information about the Etch created by their processes.
To exclude the Etch from the calculations (i.e. assume there is no slope created along the trace edge), set the value to 0.
- Width (W1) / (W2) - W1 is the width of the trace you route, W2 is the width of the upper surface of that trace once it has been etched, with the Etch factor applied. There is a forward/reverse calculation feature available for trace width. The default is for the width to be calculated based on the Target Impedance you entered (forward calculation). That width may be a value that the fabricator may not be able to deliver, such as 5.978, and they will want a more sensible value, such as 6.0. You can enter 6.0 into the Width field and press Enter on the keyboard to recalculate the calculated values (Impedance, Deviation, etc.). The
button turns gray (becomes inactive) and you are now in reverse calculation mode. If you click the button to make it active, you are again in forward mode and the Width (W1) will revert to the calculated value. This feature lets you explore realistic fabricatable width options. Manually entering a value for W2 will update the etch factor to suit.
- Impedance - the software calculates the impedance based on the properties of the materials used to make the board (copper, core and prepreg), and the cross-sectional area of the trace (determined by the width, thickness and etch factor of the trace).
- Deviation - this is a measure of the difference between what you wanted (target impedance) and what you got (calculated impedance). The software calculates the impedance deviation (what you will actually get based on the material and dimensions entered) based on the properties of the materials used to make the board (copper, core and prepreg), and the cross-sectional area of the trace (determined by the width, thickness and etch factor of the trace).
- Delay - this is the amount of time it takes for the signal to travel from the sender to the receiver.
- Inductance - the impedance calculator uses the Impedance value to calculate the inductance per unit length.
- Capacitance - the impedance calculator uses the Impedance value to calculate the capacitance per unit length.
- Board
- Stack Symmetry - enable to add layers in matching pairs, centered around the mid-dielectric layer. When enabled, the layer stack is immediately checked for symmetry around the central dielectric layer. If any pair of layers that are equidistant from the central dielectric reference layer are not identical, the Stack is not symmetric dialog opens.
- Library Compliance - when enabled, for each layer that has been selected from the Material Library, the current layer properties are checked against the values of that material definition in the library.
When Stack Symmetry is enabled:
- An edit action applied to a layer property is automatically applied to the symmetrical partner-layer.
- Adding layers will automatically add matching symmetrical partner-layers.
- Substack - this information is for the currently selected substack (layers, dielectric, thicknesses, etc.,). As you switch from one substack to another, this information will update accordingly (for the currently selected substack).
The Substack region will only be available if the Rigid/Flex option is enabled in the Features drop-down.
- Stack Name - enter a meaningful substack name. This field is useful when the X/Y stackup region is being assigned a layer substack.
- Is Flex - enable if the substack is flex.
- Layers - the total number of layers.
- Dielectrics - the total number of dielectrics.
- Conductive Thickness - the thickness of conductive layer(s). Copper signal layers are referred to as conductive layers.
- Dielectric Thickness - the thickness of dielectric layer(s).
- Total Thickness - the total thickness of the board.
Roughness - shows roughness of conductive layers.
- Model Type - preferred model for calculating the impact of surface roughness (refer to the articles below for more information on the various models). Applies to all copper layers in the stack (should it be the substack?).
- Surface Roughness - value of the surface roughness (available from your fabricator). Enter a value between 0 to 10µm, default is 0.1µm
- Roughness Factor - characterizes the expected maximal increase in conductor losses due to the roughness effect. Enter a value between 1 to 100, default is 2.
Via Types Tab
The Via Types tab is used to define the allowed Z-plane layer-spanning requirements of the via(s) used in the design.
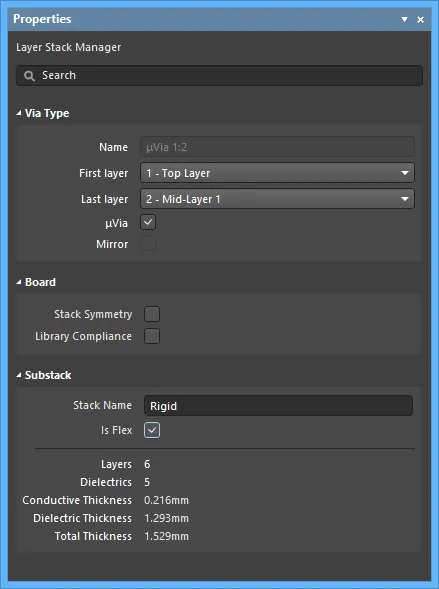
- Via Type
- Name - the name of the via. The software automatically detects the type based on the layers that have been chosen, and names the via accordingly.
- First layer - the first layer the via spans.
- Last layer - the last layer the via spans.
- µVia - enable if a microvia is required.
- Mirror - when enabled, a mirror of the current via that spans the symmetrical layers in the layer stack is created. This option is available only if the Stack Symmetry option is enabled.
- Board
- Stack Symmetry - enable to add layers in matching pairs, centered around the mid-dielectric layer. When enabled, the layer stack is immediately checked for symmetry around the central dielectric layer. If any pair of layers that are equidistant from the central dielectric reference layer are not identical, the Stack is not symmetric dialog opens.
When Stack Symmetry is enabled:
- An edit action applied to a layer property is automatically applied to the symmetrical partner-layer.
- Adding layers will automatically add matching symmetrical partner-layers.
- Library Compliance - when enabled, for each layer that has been selected from the Material Library, the current layer properties are checked against the values of that material definition in the library.
- Substack - this information is for the currently selected substack (layers, dielectric, thicknesses, etc.,). As you switch from one substack to another, this information will update accordingly (for the currently selected substack).
The Substack region will only be available if the Rigid/Flex option is enabled in the Features drop-down.
- Stack Name - enter a meaningful substack name. This field is useful when the X/Y stackup region is being assigned a layer substack.
- Is Flex - enable if the substack is flex.
- Layers - the total number of layers in the substack.
- Dielectrics - the total number of dielectrics in the substack.
- Conductive Thickness - the thickness of conductive layer(s) in the substack. Copper signal layers are referred to as conductive layers.
- Dielectric Thickness - the thickness of dielectric layer(s) in the substack.
- Total Thickness - the total thickness of the substack.
Back Drills Tab
The Back Drills tab is used to define the layer-spans that are required to be back drilled.
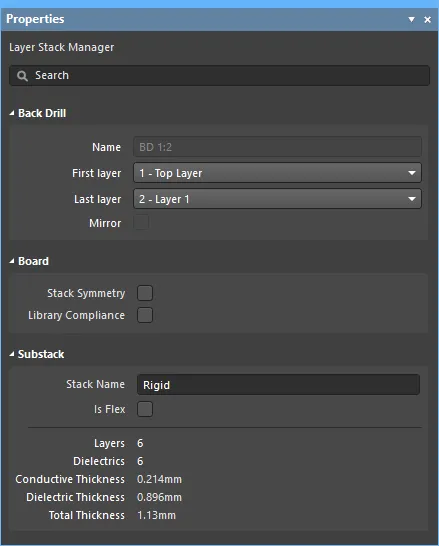
- Back Drill
- Name - the name of the back drill.
- First layer - the first layer the back drill spans.
- Last layer - the last layer the back drill spans.
- Mirror - when enabled, a mirror of the current back drill that spans the symmetrical layers in the layer stack is created. This option is available only if the Stack Symmetry option is enabled.
- Board
- Stack Symmetry - enable to add layers in matching pairs, centered around the mid-dielectric layer. When enabled, the layer stack is immediately checked for symmetry around the central dielectric layer. If any pair of layers that are equidistant from the central dielectric reference layer are not identical, the Stack is not symmetric dialog opens.
When Stack Symmetry is enabled:
- An edit action applied to a layer property is automatically applied to the symmetrical partner-layer.
- Adding layers will automatically add matching symmetrical partner-layers.
- Library Compliance - when enabled, for each layer that has been selected from the Material Library, the current layer properties are checked against the values of that material definition in the library.
- Substack - this information is for the currently selected substack (layers, dielectric, thicknesses, etc.,). As you switch from one substack to another, this information will update accordingly (for the currently selected substack).
The Substack region will only be available if the Rigid/Flex option is enabled in the Features drop-down.
- Stack Name - enter the substack name. Naming the substack is useful when the X/Y stackup region is being assigned a layer substack.
- Is Flex - enable if the substack is flex.
- Layers - the number of conductive layers.
- Dielectrics - the number of dielectrics.
- Conductive Thickness - this is the sum of the thicknesses of all signal and plane layers (all copper or conductive layers).
- Dielectric Thickness - the thickness of dielectric layer(s).
- Total Thickness - the total thickness of the finished board.
Printed Electronics Stackup Tab
The Printed Electronics Stackup tab allows you to edit and configure the layer properties of the Layer Stack for a printed design.
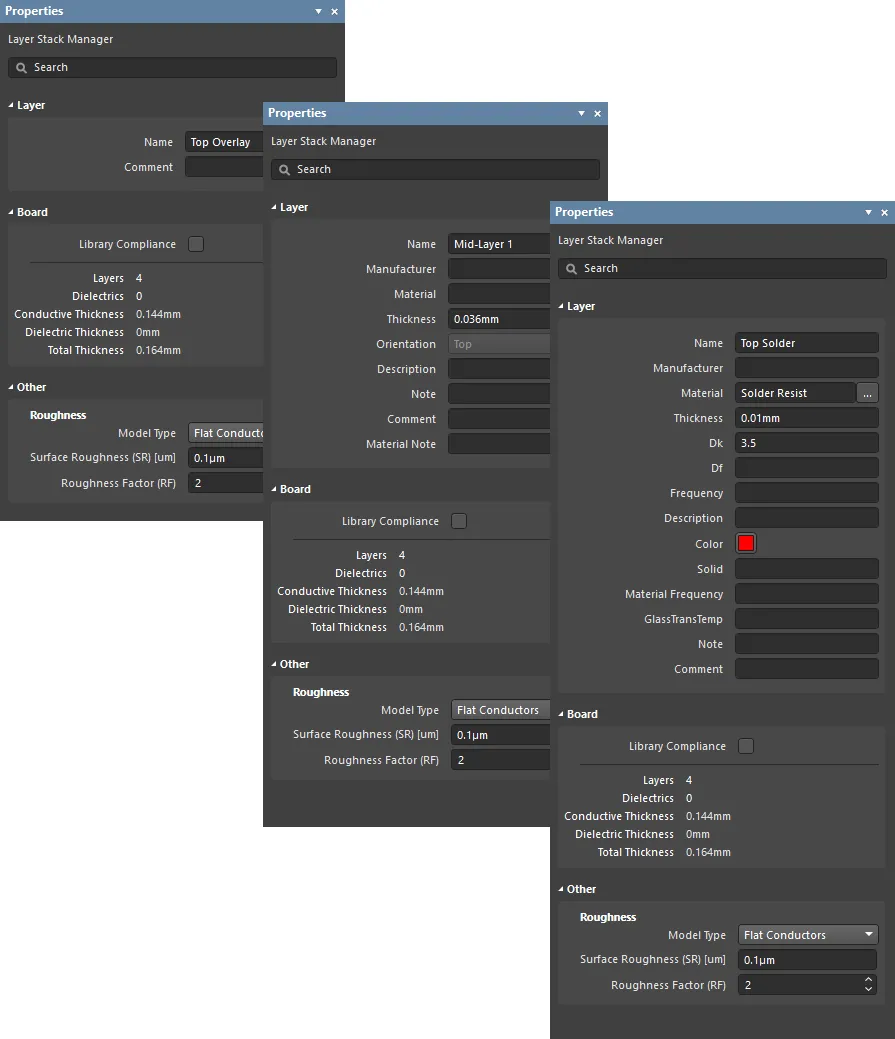
- Layer
- Name - the name of the layer.
- Manufacturer - the layer manufacturer.
- Material - the layer material. This can be pre-defined in the Altium Material Library dialog (Tools » Material Library) in the Constructions field, or user-defined in the Layer Stack. Click
to open the Select Material dialog to choose the desired material for the currently selected layer in the layer stack.
- Thickness - the thickness of the signal layer.
- Dk - this is the Dielectric Constant (also referred to as εr in electromagnetics). This indicates the relative permittivity of an insulator material, which refers to its ability to store electrical energy in an electric field. For insulating purposes, a material with lower dielectric constant is better and in RF applications, a higher dielectric constant may be desirable. In addition, the lower the relative dielectric constant, the closer the performance of the material to that of air. This property is critical to matching the impedance requirements of certain transmission lines.
- Df - this is the Dissipation Factor. This indicates the efficiency of an insulating material by showing the rate of energy loss for a certain mode of oscillation, such as mechanical, electrical, or electromechanical oscillation. In other words, this is the property of a material that describes how much of the energy transmitted is absorbed by the material. The greater the loss tangent, the larger the energy absorption into the material. This property directly impacts the signal attenuation at high speeds.
- Frequency - this is the frequency at which the material is tested and the value that Dk / Df correspond to a certain frequency. Frequency is also taken from material references.
- Description - enter a meaningful description.
- Color - this is the required color of the solder mask. Click to open a drop-down to set/change the color.
- Solid - N/A
- Material Frequency - N/A
- GlassTransTemp - this is the Glass Transition Temperature (also known as TG) and is the temperature at which the resin changes from a glass-like state to an amorphous state changing its mechanical behavior, i.e. expansion rate.
- Note - enter any pertinent notes for the layer.
- Comment - enter any necessary comments for the layer.
- Board
- Library Compliance - when enabled, for each layer that has been selected from the Material Library, the current layer properties are checked against the values of that material definition in the library.
- Layers - the number of conductive layers.
- Dielectrics - the number of dielectrics.
- Conductive Thickness - this is the sum of the thicknesses of all signal and plane layers (all copper or conductive layers).
- Dielectric Thickness - the thickness of dielectric layer(s).
- Total Thickness - the total thickness of the finished board.
- Other
Roughness - shows roughness of conductive layers.
- Model Type - preferred model for calculating the impact of surface roughness (refer to the articles below for more information on the various models). Applies to all copper layers in the stack (should it be the substack?).
- Surface Roughness - value of the surface roughness (available from your fabricator). Enter a value between 0 to 10µm, default is 0.1µm
- Roughness Factor - characterizes the expected maximal increase in conductor losses due to the roughness effect. Enter a value between 1 to 100, default is 2.
Via Shielding Support
When the active document is a PCB document (*.PcbDoc) and you select or double-click on a shielding via, the Properties panel presents options pertinent to that union object. The following collapsible sections contain information about the options and controls available:
The vias in a Via Shielding are members of a Union object. If the Display popup selection dialog option is disabled in the Preferences dialog, a single click on a via in a Via Shielding Union will select just that via. A second click in the same location will select the Via Shielding Union, displaying its properties in the Properties panel.
► See the Add Shielding to Net dialog for more information about the Via Shielding options during initial placement.
► See Via Stitching and Via Shielding for more information about working with Shielding Vias.
After modifying a value in the panel, the message Changes pending, Apply will appear at the bottom of the panel. You must click Apply for the changes to be made to the design.
Shielding Parameters
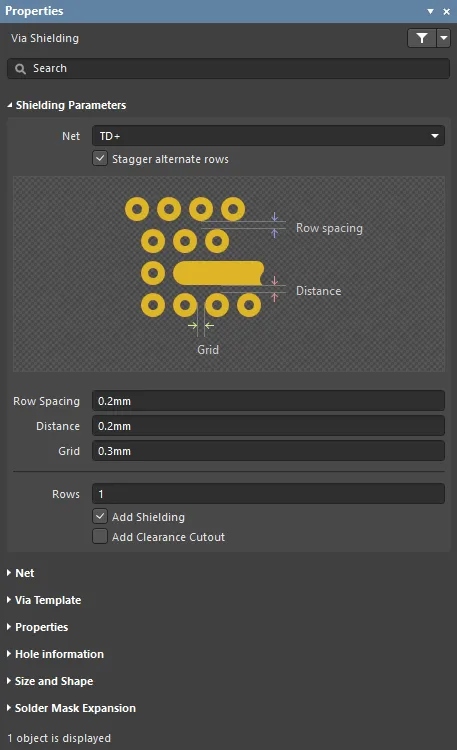
- Net - net to have shielding vias placed around.
- Stagger alternate rows - alternate rows of shielding vias are offset by half of the Grid value when this option is enabled.
- Row Spacing - spacing between rows of shielding vias (edge to edge separation) when the Rows setting is greater than 1.
- Distance - separation from the edge of the shielded net track segments, to the edge of the shielding vias.
- Grid - the distance between the edges of adjacent shielding vias. Shielding vias will not be placed in violation of applicable design rules; if a potential via site would result in a violation then that site is skipped.
- Rows - number of rows of shielding vias.
- Add Shielding - place a polygon over the area occupied by the shielding vias, connected to the net specified in the Via Net field. The polygon is defined in accordance with the applicable Clearance constraint and Polygon Connect Style design rules.
- Add Clearance Cutout - include a polygon cutout around the shielded net, set back from the net by the distance specified in the Distance field. Use this when you require a different clearance from the applicable Clearance constraint design rule.
Net
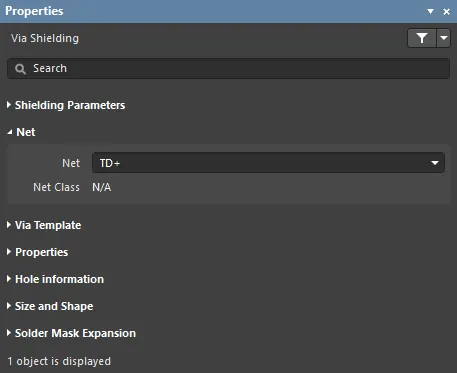
- Net - the net being shielded by the shielding vias.
- Net Class - if the chosen Net is a member of a Net Class, it will be displayed in this field.
Via Template
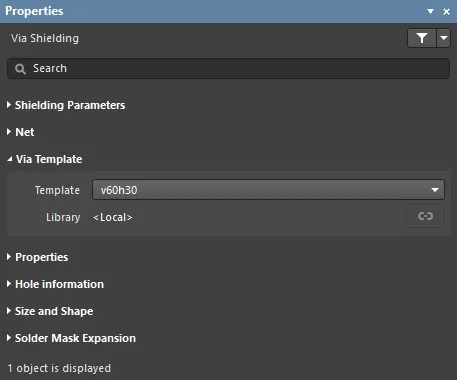
- Template - displays the currently chosen via template. Use the dropdown to change the assigned via template.
- Library - displays to which library the via template is linked and includes the option to Unlink the template from said library.
Properties
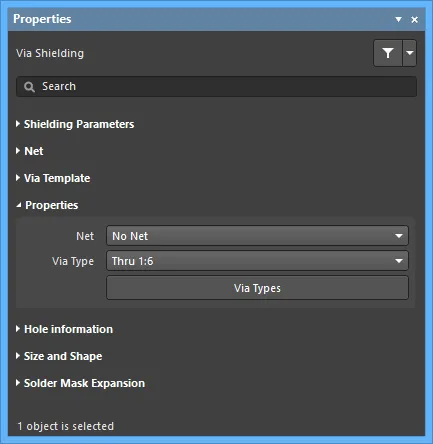
- Net - net that the shielding vias are connected to.
- Via Type - use the drop-down to select the type of via from those available in the layer stack.
- Via Types - click to open the Layer Stack to configure the required via types for the active layer stack.
Hole Information
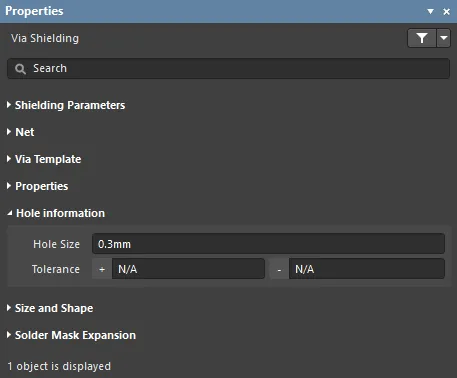
- Hole Size - size of the hole in the shielding vias.
- Tolerance - negative and positive hole size tolerances allowed for the shielding vias.
Size and Shape
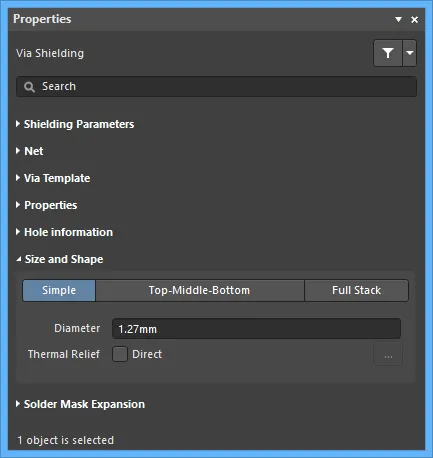
- Size and Shape - vias are one of three styles:
- Simple - the via diameter is the same on all layers
- Top-Middle-Bottom - the via diameter can be specified for the Top layer, Middle (all internal layers), and Bottom layer.
- Full Stack - the via diameter can be specified for every signal layer.
- Diameter - diameter of the shielding vias.
- Thermal Relief - check the Direct box then click the
to open the Connect Style dialog to specify the Connect Style.
Solder Mask Expansion
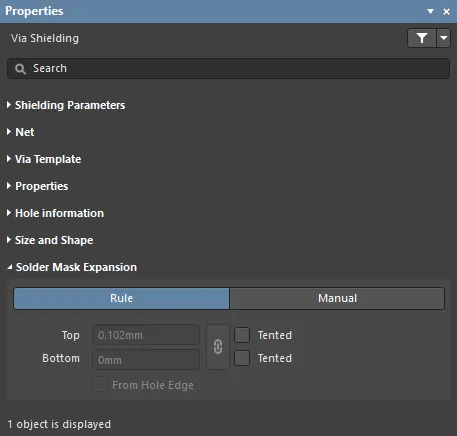
- Rule - enable this option to allow the existing solder mask expansion rule to take effect on the shielding vias. Check the Mask design category from the PCB Rules and Constraints Editor dialog.
- Manual - enable this option to edit the mask expansion values (below) for these shielding vias.
- Top - enter the required mask expansion for the Top Layer.
- Bottom - enter the required mask expansion for the Bottom Layer.
- Top Tented - if this checkbox is enabled, the mask is closed on the Top Layer for these shielding vias.
- Bottom Tented - if this checkbox is enabled, the mask is closed on the Bottom Layer for these shielding vias.
- Linked - if the Linked option is enabled, the same expansion value is used for both the Top and Bottom layers.
- From Hole Edge - enable this option to calculate the mask expansion from the edge of the drill hole instead of the edge of the via donut.
Via Stitching Support
When the active document is a PCB document (*.PcbDoc) and you select or double-click on a stitching via, the Properties panel presents options pertinent to that union object. The following collapsible sections contain information about the options and controls available.
The vias in a Via Stitching are members of a Union object. If the Display popup selection dialog option is disabled in the Preferences dialog, a single click on a via in a Via Stitching Union will select just that via. A second click in the same location will select the Via Stitching Union, displaying its properties in the Properties panel.
► See the Add Stitching to Net dialog for more information about the Via Stitching options during initial placement.
► See Via Stitching and Via Shielding for more information about working with Stitching Vias.
After modifying a value in the panel, the message Changes pending, Apply will appear at the bottom of the panel. You must click Apply for the changes to be made to the design.
Stitching Parameters
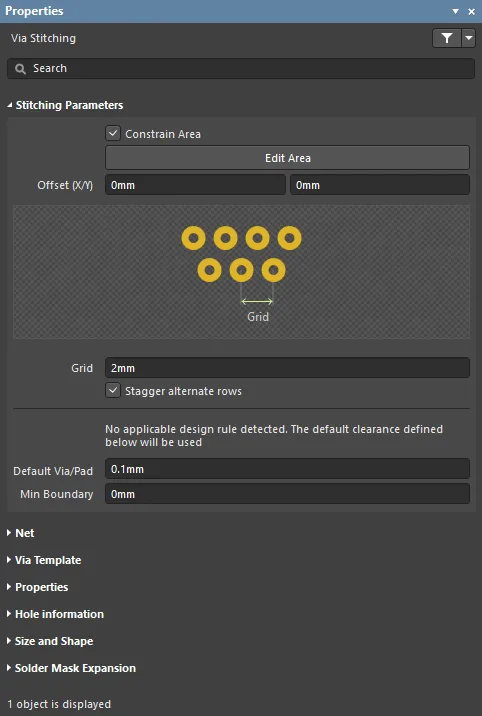
- Constrain Area - enable to constrain via stitching to a specific area. After selecting the option, you will be taken to the design space. After using the cross-hair cursor to define the constrain area, right-click to return to the dialog.
- Edit Area - click to edit the constrain area.
- Offset (X/Y) - enter the X and Y offset distance(s). The stitching pattern will placed within the constrain area, starting at an offset of the specified X and Y amount.
- Grid - the distance between the center of adjacent stitching vias. Stitching vias will not be placed in violation of applicable design rules; if a potential via site would result in a violation that site is skipped.
- Stagger alternate rows - alternate rows of shielding vias are offset by half of the Grid value.
- Default Via/Pad - stitching vias are only placed on potential stitching sites if this much clearance exists. Since potential stitching sites are determined by the stitching grid, it is likely they will be further than apart than this setting.
- Min Boundary - stitching vias are only placed on potential stitching sites if this much clearance exists to the edge of Polygon/Fill/Plane regions.
Net
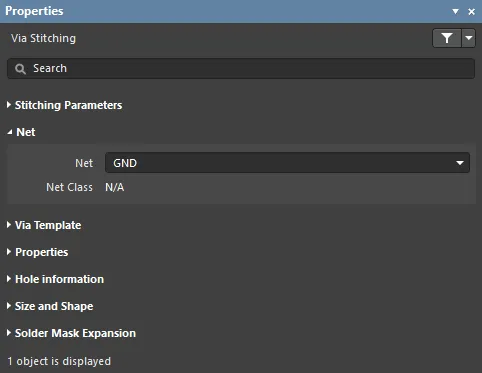
- Net - the net to which the via stitching is currently assigned. Change the net assignment by clicking in the field and choosing a net from the drop down list.
- Net Class - if the chosen Net is a member of a Net Class, it will be displayed in this field.
Via Template
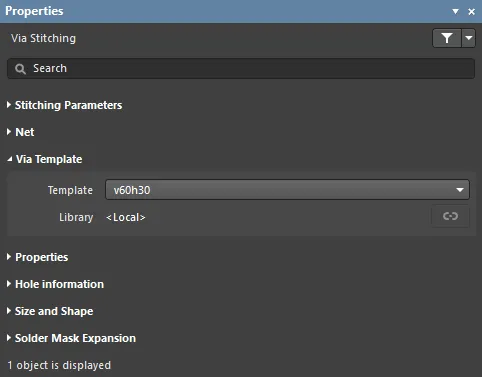
- Template - displays the currently chosen via template. Use the dropdown to change the assigned via template.
- Library - displays to which library the via template is linked and includes the option to Unlink the template from said library.
Properties
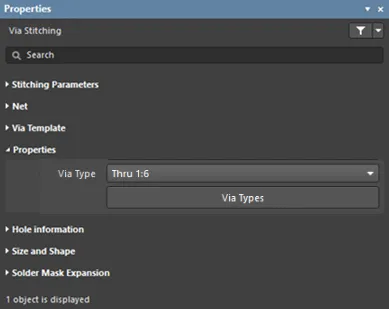
- Via Type - use the drop-down to select the type of via from those available in the layer stack.
- Via Types - click to open the Layer Stack to configure the required via types for the active layer stack.
Hole Information
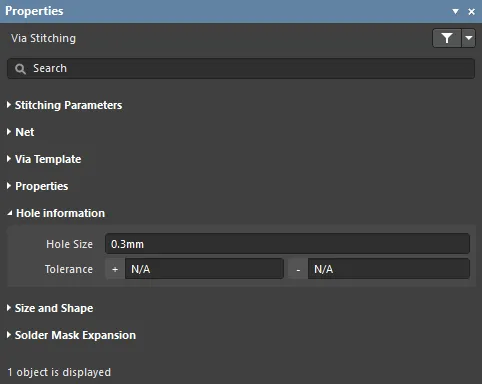
- Hole Size - size of the hole in the stitching vias.
- Tolerance - negative and positive tolerances allowed for the stitching vias.
Size and Shape
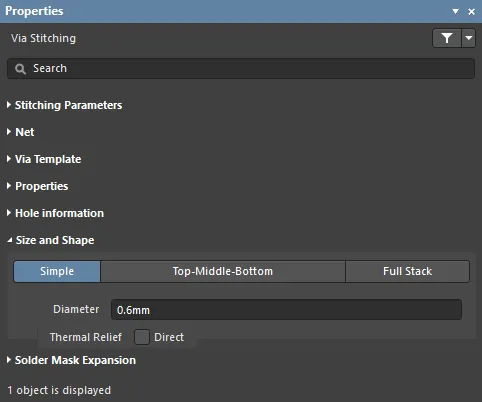
- Size and Shape - vias are one of three styles:
- Simple - the via diameter is the same on all layers
- Top-Middle-Bottom - the via diameter can be specified for the Top layer, Middle (all internal layers), and Bottom layer.
- Full Stack - the via diameter can be specified for every signal layer.
- Diameter - diameter of the stitching vias.
- Thermal Relief - check the Direct box then click the
to open the Connect Style dialog to specify the Connect Style.
Solder Mask Expansion
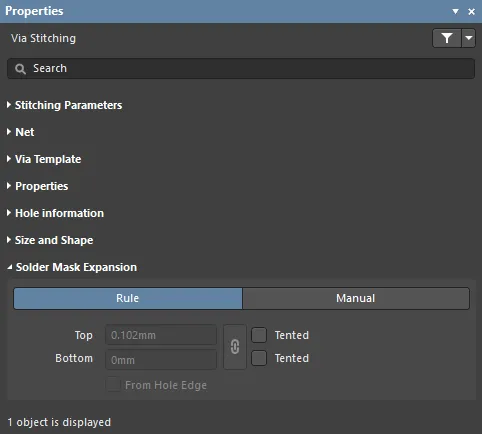
- Rule - enable this option to allow the existing solder mask expansion rule to take effect on the stitching vias. Check the Mask design category from the PCB Rules and Constraints Editor dialog.
- Manual - enable this option to edit the mask expansion values (below) for these stitching vias.
- Top - enter the required mask expansion for the Top Layer.
- Bottom - enter the required mask expansion for the Bottom Layer.
- Top Tented - if this checkbox is enabled, the mask is closed on the Top Layer for these stitching vias.
- Bottom Tented - if this checkbox is enabled, the mask is closed on the Bottom Layer for these stitching vias.
- Linked - if the Linked option is enabled, the same expansion value is used for both the Top and Bottom layers.
- From Hole Edge - enable this option to calculate the expansion from the edge of the drill hole instead of the edge of the via donut.
Multi-board Schematic Support
When the active document is a multi-board schematic document (*.MbsDoc) and when no design object is currently selected in the design workspace, the Properties panel presents the Document Options.
The following collapsible sections contain information about the options and controls available under the panel's General tab:
Selection Filter
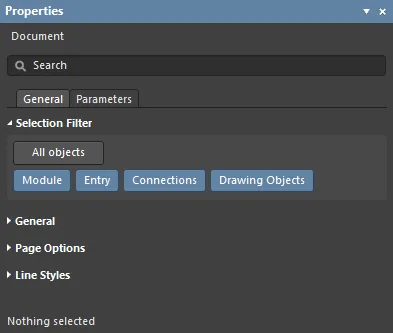
The options in this section of the panel determine which multi-board objects may be selected in the workspace.
- All Objects button – select remove object filtering so that all types of objects may be selected.
- Object buttons – toggle each object button to enable/disable the ability to select that object type.
General
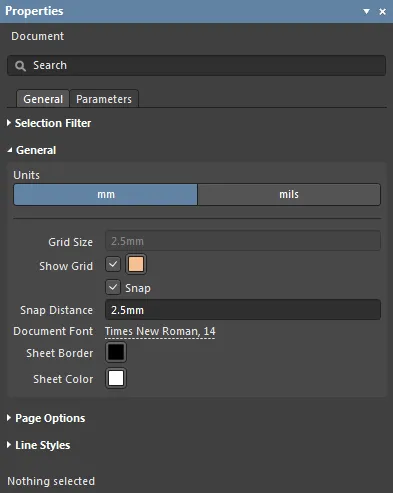
- Units – select the measurement units that apply to the multi-board document and its graphic elements.
- Grid Size – set the measured distance between each sheet grid line. Note: this option is not editable in multi-board documents.
- Show Grid – check to display grid lines at the default Grid Size in the document sheet. Click the associated color button (
) to specify the color of the grid lines in the color selector drop-down, which includes options for preset colors, HEX/RGB color values, and the graphic selection of color shades.
- Snap – when checked, the ghost/preview cursor will snap (jump) to grid line intersections while the editor is in object placement mode. The cursor will also snap to graphic object vertices (corners, etc.,), line midpoints and circle centers.
- Snap Distance – set the distance at which the preview cursor will snap onto the targets outlined above. The preview cursor changes to an orange dot when a midpoint, vertex, or center is snapped to.
- Document Font – set the font size, style and any additional font attributes that will be used for the text associated with all objects in the document sheet. For any given object, the font settings may be overridden in its corresponding Properties panel mode, which is enabled when that object is selected.
- Sheet Border – click the associated color button to set the zone border line and character color for the document sheet.
- Sheet Color – click the associated color button to set the background color for the document sheet.
Page Options
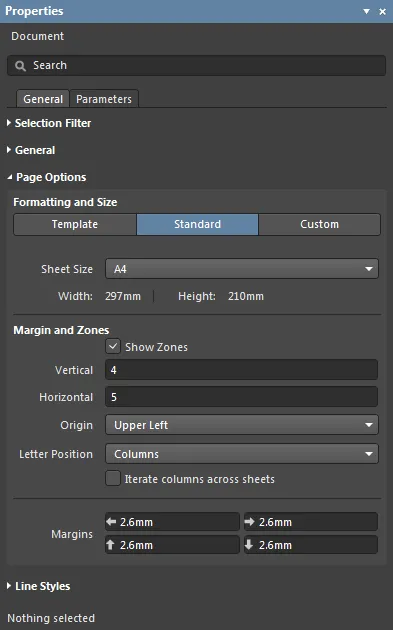
Formatting and Size
- Template mode – set the page size and format by selecting from a range of predefined schematic sheet templates. The list includes templates found in the location specified in the Data Management - Templates page of the Preferences dialog. Note that a default schematic sheet to be used for new multi-board documents may be defined in the System - New Document Defaults page of the Preferences dialog.
- Template – use the drop-down menu to select from a list of standardized page templates, and if required, use the
button to refresh the template and drawing.
- Width/Height – the dimensions of the current page size shown in the current document units (see the General section above).
- Source – use the browse button (
) to navigate to and select an alternative template source in the schematic *.SchDot
format.
- Standard mode – set the sheet size to a standard page format.
- Sheet Size – use the drop-down menu to select from a list of standard page dimensions.
- Width/Height – the dimensions of the current page size in the current document units.
- Custom mode – set the sheet size to specified custom dimensions.
- Width – enter the required sheet width measurement.
- Height – enter the required sheet height measurement.
Margin and Zones
Defines the size of the sheet border graphics and its zone divisions. Uncheck the Show Zones box to hide the zone divisions in the border graphics.
- Vertical – set the number of divisions (rows) in the vertical sheet margin. The alpha-numeric zone labeling type is defined by the Origin and Letter Position settings.
- Horizontal – set the number of divisions (columns) in the horizontal sheet margin.
- Origin – sets which corner of the document sheet(s) the perimeter zone alpha-numeric indicators will begin from (zone position
A-1
or 1-A
).
- Letter Position – set where the letter zone indicators are placed on the document sheet, either in the horizontal perimeter zones (columns) or the vertical zones (rows).
- Margins – set the distance (in the current units) between the page edge and each of the four border lines as indicated by the arrows associated with each entry field.
Line Styles
The following collapsible section contains information about the options and controls available under the panel's Parameters tab:
Parameters
When a design object is selected in the workspace, the Properties panel will present options specific to that object type – the panel changes to that object 'mode'. The following table lists the object types available for placement within a multi-board schematic document, where each listed entry links to its associated properties information (Properties panel mode) page.
Multi-board Assembly Mate Support
When the active document is a Multi-board Assembly document (*.MbaDoc) and a Mate is selected, the Properties panel presents the Mate mode.
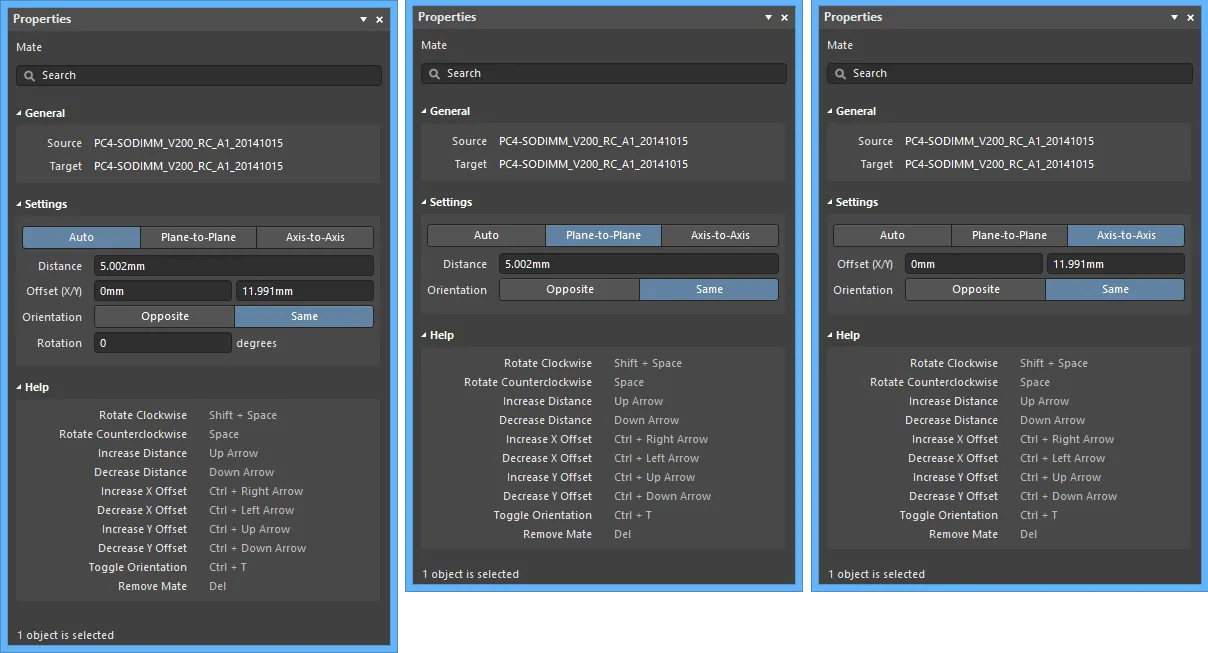
The Properties panel in Mate mode
The following collapsible sections contain information about the options and controls available: