Advanced Design Technologies_AD
This document is no longer available beyond version 20.2. Information can now be found using the following links:
Today's compact electronic products are delivered in compact and unusually shaped enclosures. Often powered by batteries they are light-weight and portable, requiring lower signal voltages and power consumption. And these compact designs use the latest device technologies with fast switching speeds, speeds so fast that the routing is no longer a set of simple copper paths that carry a current and expresses a voltage, now the routes are an array of transmission lines - turning the routing process into an engineering analysis and design challenge in its own right.
All of this brings many new challenges for the design and implementation phase of electronic product development. Various design technologies have emerged to help, many of which are available in Altium Designer.
Designing with Touch Controls
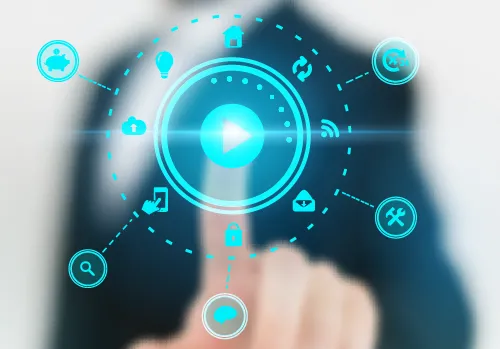
Touch sensitive electronics are on the forefront of technology. As the user interface becomes more important to the success of your product, clean and modern controls are now considered essential.
Adding a touch sensor to your electronic product is a process that starts at the beginning of a design, and extends into the board design process. Altium Designer's touch sensor support allows you do to easily integrate touch sensors into your design workflow.
Altium Designer's touch control support includes:
- Configurable touch sensor libraries that let you set the controls and parameters of your device from the start.
- Automatically generate the complex land patterns and footprints required for touch sensors.
- Model and verify your designs in Native 3D to make sure they are aligned and fit correctly.
- Atmel® QTouch® and QMatrix® libraries; Cypress® Capsense® libraries; & Microchip® mTouch® libraries
► Learn more about Designing with Touch Controls
Rigid-Flex Design
Rigid-flex is the name given to a printed circuit that is a combination of both flexible circuit(s) and rigid circuit(s). Initially developed for the space program to save space and weight, flexible and rigid-flex PCBs are popular in today's portable devices, such as mobile phones and tablets.
As well as helping reduce the size of a product, they can also:
- Reduce packaging complexity by substantially reducing the need for interconnect wiring
- Improve product reliability due to reduced interconnection hardware and improved assembly yields
- Reduce cost, when considered as part of the overall product manufacture and assembly costs
Altium Designer's strong support for rigid-flex includes the ability to perform 3D collision detection, within Altium Designer's native 3D PCB editor. You can also generate 3D STEP-format output of the folded board, ready to load into your MCAD software.
► Learn more about Rigid-flex Design
High Speed Design
In a high-speed digital design the routing cannot be considered as simple interconnections. With a fast switching signal, energy can reflect from the target pin back towards the source, interacting with and distorting the original signal.
The way that the energy in the signal interacts with the materials that carry the signal changes too. No longer contained within the routing copper, some of the energy travels in the surrounding insulation. This energy can radiate from the route and couple into adjacent routes, or radiate further and become electromagnetic interference (EMI), resulting in the product failing to meet mandatory emission standards.
These challenges are managed by applying suitable high-speed design techniques, including:
- Careful material selection, layer stack design, and via design and use
- Use of differential pairs and controlled impedance routing, with well defined signal return paths
- Signal integrity and impedance analysis, with length tuning to ensure the signal timing requirements are met
► Learn more about High Speed Design
Designing with Embedded Components
The ever-increasing demand for smaller and more integrated electronic products, combined with the higher frequencies of the signals within these devices, drives the ongoing research into better ways to fabricate and assemble a circuit.
One technique that delivers both higher density and improved support for higher signal frequencies, is to embed components within the layers of the circuit structure. For example, embedding discrete components directly under an integrated circuit can result in: shorter signal lengths; reduced resistance and parasitic inductance, leading to lower noise and EMI; and improved integrity of the circuit signals. These improvements deliver smaller and more reliable products, supporting faster signal speeds and higher bandwidths. Combined with the on-going improvements being achieved in fabrication processes and technologies, they can also lead to a reduction in the product size, and lower fabrication and board level assembly costs.
Embedding components places a number of unusual demands on each stage of the process: from design, to fabrication, to assembly, to testing and maintenance of the finished product.
► Learn more about Embedded Components
Printed Electronics
An exciting evolution in the design and development of electronic products is the ability to print the electronic circuit directly onto a substrate, such as a plastic molding that becomes a part of the product.
Printed electronics will become a pivotal technology, allowing the integration of electronics into new markets. Printed electronics allow an intimate connection between the circuit and the product. From a flexible sensor that attaches directly to the body, through to a multi-sensor, finger tip-shaped molding that allows a robotic hand to hold a soft plastic cup as liquid is poured into it, printed electronics will allow innovative new solutions to be developed across many market segments.
► Learn more about Printed Electronics
Where to Next?
Designing with Embedded Components
Designing Systems with Multiple Boards
The Advantage of 3D in ECAD-MCAD Integration