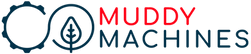
Altium Customer Success
Shaping the Future of Intelligent Agriculture with Muddy Machines and Altium
“As a startup, you have to be able to move faster and iterate quickly. That’s what we’re trying to do, and why we choose the software we do. We’ve made that bet with Altium and Altium 365 knowing that it is a robust tool, a scalable tool, and we can continue adding users as we expand and having all of that data accessible to them as we move forward.”
Discover how Muddy Machines is revolutionizing agriculture with advanced farming robots. Their collaboration with the UK's largest asparagus grower tackles labor shortages, ensuring sustainable food production and a secure future for all.
- Altium 365 has been proven to save 159 hours per engineer in year 1 of adoption (Learn More). This success story reveals some of the time and cost-saving capabilities that Muddy Machines benefitted from by using Altium 365.
- The team designed an advanced electronics system and cabling for their electric farming robot with Altium Designer’s Multi-board System Design and Harness Design capabilities.
- As a pre-revenue startup, the team had access to industry-leading ECAD software at an affordable price through Altium’s Launchpad Program.
Muddy Machines is addressing a critical challenge that has long plagued the agricultural sector—labor shortages. In the UK alone, the agricultural industry requires over 80,000 seasonal workers annually to harvest fresh produce. However, recent factors such as Brexit and the COVID-19 pandemic have severely impacted the availability of labor, exacerbating the need for a sustainable solution to ensure food security and resilience in domestic production. Muddy Machines was established to overcome these challenges with the latest AI and robotics technology.
“What this will do, is it will help us meet our commitment to produce 60% of the food we eat here in the UK, and it will also make the most of the innovations in AI technology across all of our farms.”
Revolutionizing Farming with Intelligent Robotics
Muddy Machines’ vision is to replace our current reliance on large, diesel-powered farming machinery with a fleet of small, lightweight, battery-powered robots. These robots can operate in herds, allowing one person to supervise multiple machines and significantly reducing the need for extensive human labor.
At the heart of this vision is Sprout, a four-wheel-drive electric farming robot that minimizes soil compaction while harvesting and can be monitored through a custom app. This app provides live harvest performance data to machine operators and farm owners, enabling informed decision-making based on real-time information.
Sprout is powered by lithium batteries, boasting a charge time of 4.5 hours and an impressive 16-hour runtime. Each robot is equipped with two harvesting tools and multiple 3D cameras that ensure precise cutting according to a grower’s specifications. It has the capacity to store up to 28kg of produce and features advanced navigation systems that include GPS tracking, obstacle detection, and autonomously returning to base.
One of Sprout's key applications is harvesting green asparagus. It operates efficiently in both fields and polytunnels, utilizing cutting-edge AI to evaluate each spear of asparagus, and selectively harvesting those that are ripe while leaving the immature ones to grow further. The integrated vision system and AI algorithms not only perform selective harvesting but also predict crop yields, providing valuable forecasts to growers.
Managing the Complexity of Interconnected Systems
One of the primary challenges faced by Muddy Machines in developing Sprout was designing its complex multi-board electronics architecture. Sprout's functionality depends on a sophisticated system consisting of a main power control board and 2 PCBs that support auxiliary functions including steering and safety ultrasonic sensor systems. This complexity necessitated the creation of a multi-board system and harnesses to connect all of the PCBs, ensuring reliable communication across all of the robot’s interconnections.
Altium Designer's Multi-board System Design was instrumental in designing the interconnections between multiple PCBs within Sprout. The tool's intuitive design approach, which mirrors the process used for single-board designs, allowed the Muddy Machines’ engineering team to effectively design the function and verify the fit of the PCBs within Sprout’s multi-board assembly. Additionally, the team was able to update data in their multi-board project with their latest PCB design changes in a few clicks. Altium Designer’s unified environment enabled straightforward identification and synchronization of every change in individual PCBs and the overall multi-board system design.
As a pre-revenue startup, Muddy Machines also needed a cost-effective solution to design Sprout's connective harnesses without the need for expensive third-party software. With Altium Designer’s Harness Design capabilities, the team was able to design cabling in the same familiar environment where they already designed their PCBs and multi-board system. With Draftsman documents available for Harness projects, the team was also able to quickly generate technical documentation, including a general view of the cable assembly, dimensions, notes, and connection tables.
“All of our designs are done in Altium Designer, with Altium 365 supporting all of that, from the PCB design element all the way through cabling design, system design, and speccing off the shelf parts and systems.”
Accelerating Iteration with Enhanced Integration Across Disciplines
Another significant challenge for the team was reducing the length of their hardware iteration cycles. As Christopher Chavasse, Founder & CEO at Muddy Machines explains, “Whilst software is really easy to iterate, build new versions and push it out, hardware iterations can be 2, 3, or 4 weeks. Having software and the right tools in place allows us to integrate mechanics, electronics, and software, and reduce the iterative cycle time to get new products, new technologies, and new ideas out into the field and tested as quickly as possible.”
Altium 365’s ECAD Data Management solution enabled the team to centralize all their hardware design data, component libraries, and manufacturing packages. By consolidating these resources in a single, secure location accessible from any device with a browser, Muddy Machines' engineers could access and review schematics and wiring diagrams out in the field while they were debugging issues with their robots without having to install any additional software.
Contextual Commenting further enhanced collaborative efforts across Muddy Machine’s teams. Project stakeholders were able to engage in detailed technical conversations directly within the context of their PCB, harness, and multi-board projects without having to install any ECAD software. By digitally capturing and pinning comments to specific design assets, feedback was never lost or misplaced.
Lastly, Altium 365’s Assembly Assistant enabled the team to do fast and accurate manual board assembly for their prototypes from any device with a browser. Components were displayed on-screen for quick assembly, identifying location and orientation, and reducing errors and costly reworks. Any changes made to design files were automatically synced with Assembly Assistant, ensuring that the team was always looking at the latest BOM and board layout.
“[Altium 365] streamlines things. It means I don’t get emails 24/7 asking for various bits of information. We’ve got people who can access harness drawings, either to review them or make the cables. Access to PCB assembly instructions that they can follow step-by-step, or access to our schematics if we’re trying to debug an issue in the field.”
Navigating Strategic Component Selection for a Pre-Revenue Startup
Operating as a pre-revenue startup imposed stringent financial constraints on Muddy Machines, necessitating meticulous planning and budget-conscious decisions. This was particularly crucial in the sourcing and selection of their electronic components.
With the Manufacturer Part Search in Altium Designer, the team had access to sophisticated search capabilities based on categories and parametric filtering that allowed them to zero in on the exact manufactured components they needed, and also select a preferred supplier of that physical part based on cost and availability. Once a part was chosen, they could then instantly add it to their design and library.
Additionally, ActiveBOM provided Muddy Machines with a powerful tool for managing the complexities of sourcing components across multiple PCBs in their multi-board system. The team had a centralized view of BOM cost and availability, and ActiveBOM automatically calculated the cost of their project’s components with price breaks for order quantity. With the most up-to-date data provided by their preferred suppliers, it was also easy to rank supplier choices and set target prices for parts.
A Pioneer in Agricultural Innovation
Muddy Machines stands at the forefront of agricultural technology, addressing crucial labor shortages with its innovative robotics technology. Utilizing Altium Designer and Altium 365’s powerful capabilities has enabled the team to iterate quickly and ensure that the UK has a secure and sustainable domestic food production system for the generations ahead.
A pivotal element in Muddy Machines' journey has been their participation in the Altium Launchpad Program. Christopher Chavasse, Founder & CEO of Muddy Machines, highlighted the strategic importance of this support: “As a really ambitious startup we know that we’re going to grow and scale our engineering team, and making sure we choose the right software now and don’t have to spend a lot of time converting everything into a new software package is really important to us. Having something that takes care of all of that for us through the Altium Launchpad program has been invaluable.”