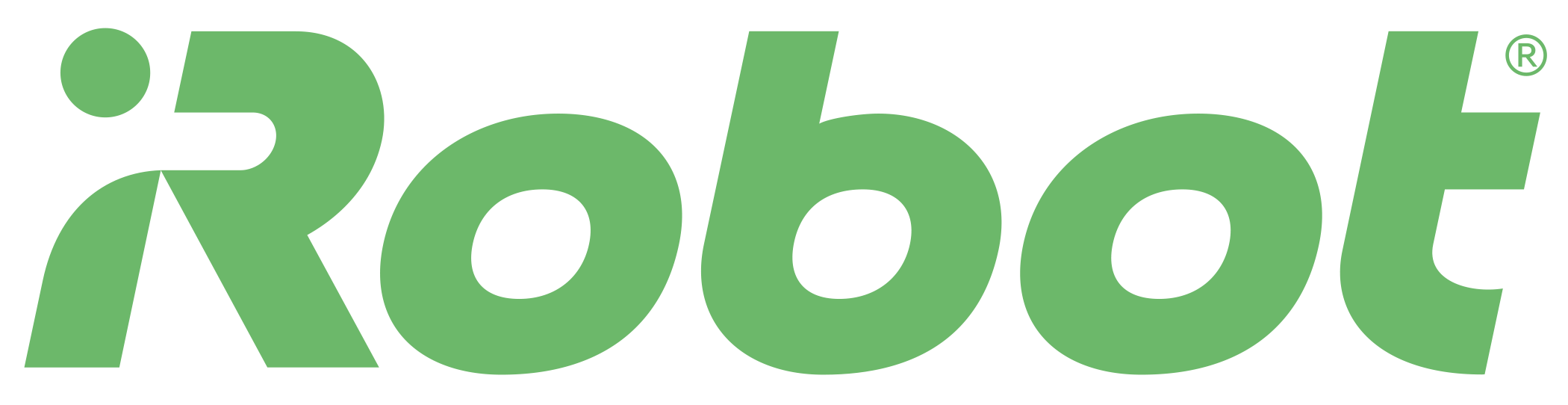
Altium Customer Success
iRobot Overcomes PLM Integration Challenges with Altium
"This is what we've always been waiting for. The library parts are right here. I don't have to go anywhere. I don't have to sync. I can create my own projects. I can set up permissions for projects. We can work in smaller teams. We can do design reviews ourselves. All built into the tool."
Find out how the electronics team at iRobot, the leading global consumer robot company, maximizes their PLM investment with Altium.
iRobot is the leading global consumer robot company with a long history of robotic innovation. The company is constantly pushing the boundaries of technology to design and build the world's most thoughtful robots and intelligent home innovations that make life better.
"iRobot's culture is one that challenges us to be innovative and not just come up with ideas but reduce those ideas to practice and change the world with those ideas."
iRobot has long embraced digital transformation to push the envelope in robotics innovation. To stay competitive and address business challenges, iRobot has invested in digitization initiatives. By digitizing its operations and improving collaboration across enterprise organizations, iRobot can streamline processes, engineering changes, and product complexity while improving data quality and integrity.
The Challenge of Disconnected ECAD Data
Even after their strategic digital initiatives were well underway, iRobot still had to deal with a missing element. It is all too common for corporate digital initiatives to lack a plan to implement digital integration between the electronics design domain (ECAD) and the rest of the business. Linking ECAD to the rest of the enterprise organization is the last mile of digital transformation. A particular challenge the electronics engineers at iRobot had to overcome was importing data from their ECAD applications into their corporate Windchill PLM system. The process, which was overly manual and complicated, lacked intelligent integration between the two systems or any kind of automation. It was time-consuming and frustrating to manage data and keep track of changes. Engineers had to interrupt their regular workflows to check their data into Windchill using an ad-hoc upload tool.
"It was the [Windchill] check-in process that you had to understand. I do this. I do this. I do this. It was a real challenge for our engineers to break from their usual working processes to perform the upload to Windchill PLM."
Because the engineers wanted to avoid this frustration and disruption to their workflows, promptly sharing ECAD data with the broader team became a problem. Engineers would hold their data until they absolutely needed to share it. Engineers also shared data outside the PLM, creating additional risks associated with disconnected data. These factors created a more significant problem with the lack of timely and accurate data in the PLM system needed by various stakeholders, creating additional communication and collaboration problems between design team members and adjacent product domains. As a result, design teams struggled to work together efficiently, especially early in the design process, when the opportunity to resolve issues earlier was relatively easy.
COVID Accelerated the Need for Better Collaboration and Automation
The COVID-19 pandemic exacerbated electronics design and ECAD data management challenges at iRobot. Before the pandemic, engineers took the benefit of working together in the same office for granted. But with COVID lockdowns and new work-from-home policies, everything changed.
"When COVID really hit the company hard in year two, and we realized we can't get any of the parts we need to make these products, the EE team split in half. Half of them were researching parts, and half of them were doing cost-downs and replacement designs. It was just all hands on deck to figure out how to do this stuff."
Before COVID, in-person collaboration among engineers was the norm and highly productive for solving occasional part obsolescence or shortage problems. By working together face-to-face, they could quickly identify and address any issues. But once everyone worked off-site, finding efficient and productive ways to collaborate from remote locations became just as complicated as finding or redesigning critical out-of-stock parts affected by unprecedented global supply chain issues. To keep product development on track, engineers and stakeholders needed timely and easy access to the latest digital data and reference points to continue working and addressing issues during unforeseen circumstances.
Digitally Integrating ECAD and Automating Workflows
The electronics team at iRobot turned to Altium for comprehensive, digitally integrated solutions to manage their ECAD data and workflows and connect all design team members and stakeholders. With Altium Enterprise Solutions, iRobot was able to streamline its entire design process, making it more efficient and effective. Altium Enterprise Solutions provided unique capabilities that digitally integrated existing tools and workflows. The iRobot electronics development teams could continue to work as they always had, but without the frustration and disruption of manual and ad-hoc processes. The automated workflows allowed the team access and visibility to needed ECAD data in real-time and the ability to work and collaborate more effectively on every design.
"This is what we've always been waiting for. The library parts are right here. I don't have to go anywhere. I don't have to sync. I can create my own projects. I can set up permissions for projects. We can work in smaller teams. We can do design reviews ourselves. All built into the tool."
Altium helped iRobot develop a more robust digital thread and continuity running through its ECAD applications and processes. That strong digital thread is now critical for iRobot's newest challenge: moving to a joint development and manufacturing model. This new model relies on third parties for ECAD and MCAD design, as well as for manufacturing. The Altium enterprise solutions iRobot engineers efficiently collaborate with internal and external stakeholders worldwide to develop the next generation of iRobot products.
"The idea that we can get people onboarded and connected quickly and easily through the Altium enterprise solutions …beautiful."
The Last Mile of Digital Transformation
Altium is transforming electronics design by offering companies like iRobot, the link to bring digital transformation to life with comprehensive, digitally-integrated electronic design solutions for enterprises of all sizes and maturities.
Altium Enterprise Solutions are the most lightweight, easy-to-implement electronics design solutions for enterprise organizations of all sizes or maturity, making the last mile of digital transformation not only possible – but easy.